NEMA Motors vs IEC Motors: The Definitive Guide
01/01/2025
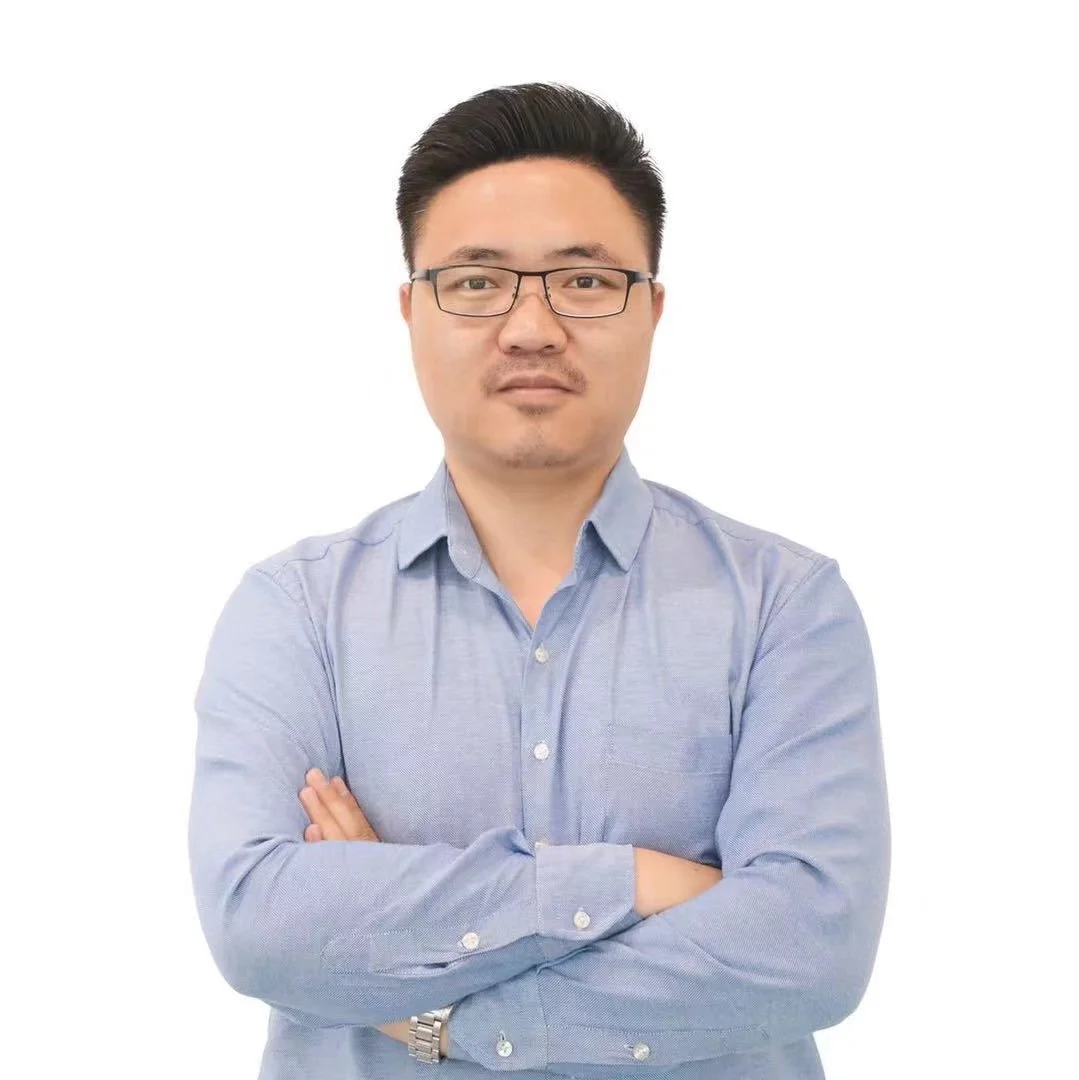
Sam Nie
Hello every one. This is Sam Nie, the CEO of LUPMOTORS. With 10 year's technical and manufacture experience in the field of 3-phase electric motor, I can provide you definitive guides in the knowledge of 3-phase industrial electric motors,which will help you a lot in selecting electric motors for your applications.
Imagine this: you’re in the middle of a critical industrial upgrade, and the motor you’ve chosen doesn’t fit the standard required for your region or application. The result? Costly downtime, compliance issues, and wasted resources. That’s the problem many face when they don’t understand the key differences between NEMA and IEC motors.
Both motor types are vital for powering industries worldwide. NEMA (National Electrical Manufacturers Association) motors are primarily used in North America, while IEC (International Electrotechnical Commission) motors dominate in Europe and many parts of Asia. These two standards impact everything from motor design to operational compatibility.
In this guide, we’ll uncover the critical distinctions, similarities, and practical considerations between these motors. By the end, you’ll know exactly how to choose the right one for your needs. Let’s get started!
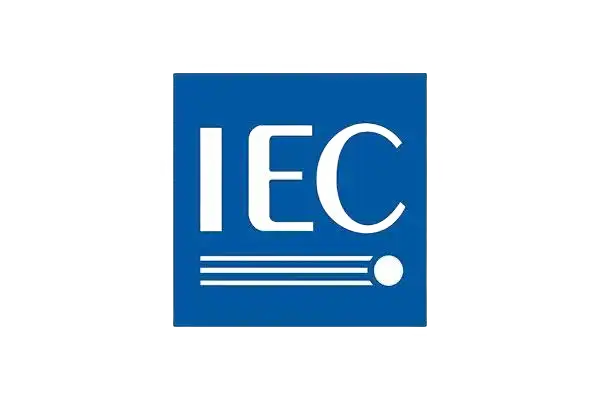

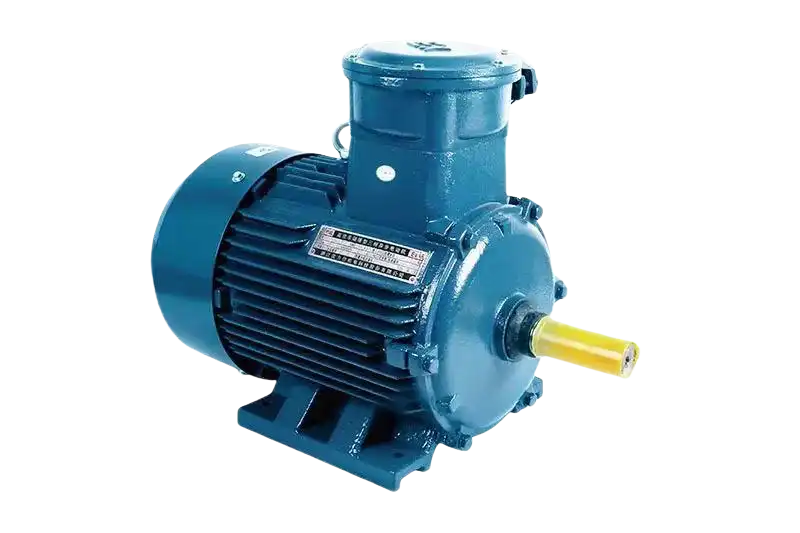
Table of Contents
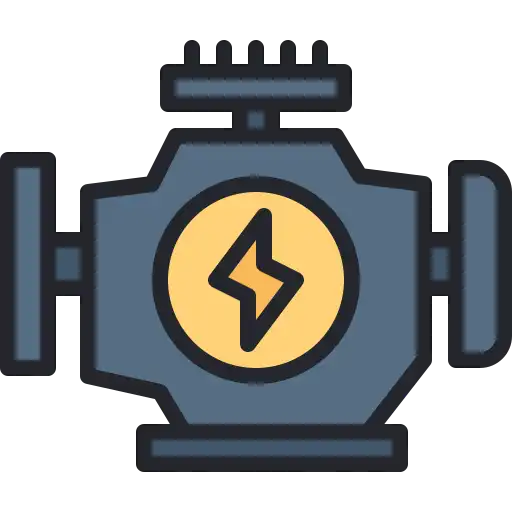
1. What Are NEMA Motors and IEC Motors?

1.1 What Are NEMA Motors?
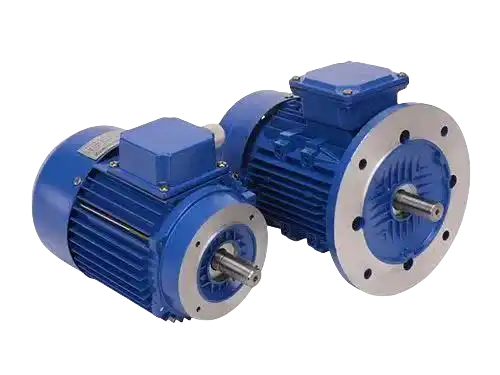
NEMA motors are designed under the standards of the National Electrical Manufacturers Association, a U.S.-based organization that sets guidelines for motor design, safety, and performance.
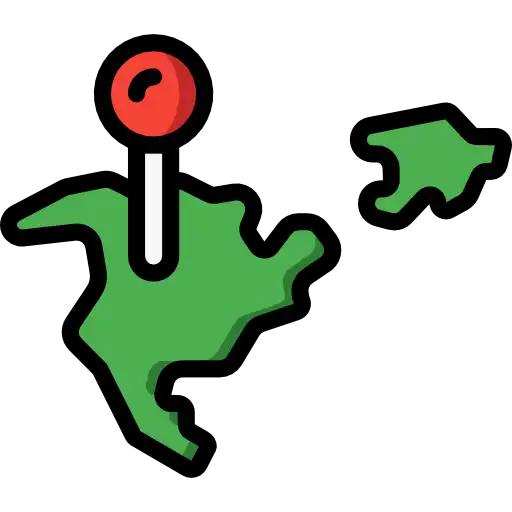
These motors are widely used in North America, where their compatibility with regional voltage and frequency standards (such as 60 Hz) is crucial.
NEMA motors are known for their robust design and ease of replacement. Standardized dimensions and performance ratings ensure that these motors can be easily swapped out without requiring extensive modifications to existing systems. This makes them a go-to choice for many industries, including manufacturing, agriculture, and HVAC systems.
Manufacturing.
Agriculture
HVAC systems

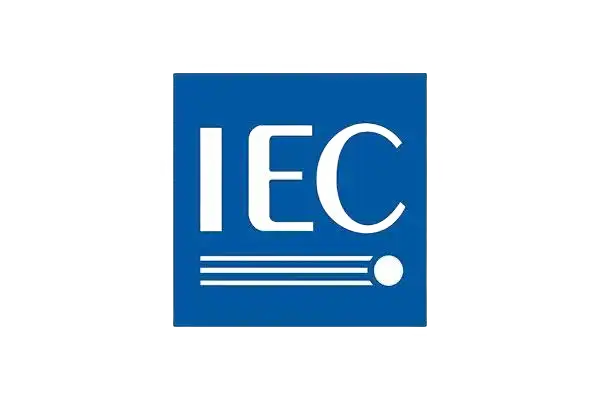
1.2 What is an Induction Motor?

IEC motors, on the other hand, follow the standards set by the International Electrotechnical Commission, a global body that promotes international compatibility.
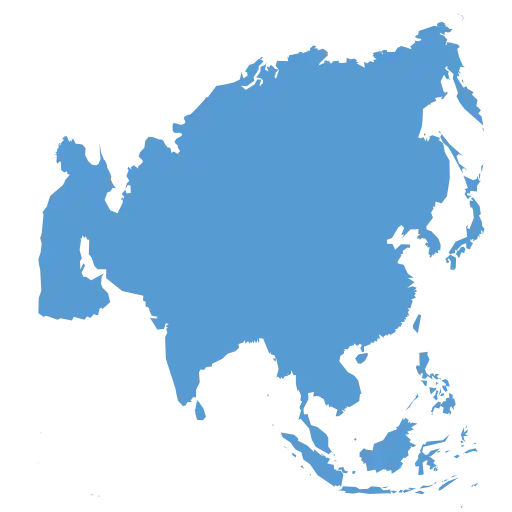
These motors are prevalent in Europe, Asia, and other regions where 50 Hz frequency and different voltage ranges are the norm.
IEC motors emphasize versatility and energy efficiency. With their focus on compact design and global interchangeability, they are widely used in automation, oil and gas, and industrial applications. Unlike NEMA, IEC standards cater to a broader range of operating conditions, making them highly adaptable across markets.
Automation
Oil and gas
Industrial applications

The Similarity Between NEMA Motors and IEC Motors
Despite their differences, NEMA and IEC motors share a core mission: providing reliable and efficient mechanical power. Both adhere to rigorous standards set by their governing bodies to ensure performance, safety, and reliability.
-
Purpose
Both motors are used in industrial, commercial, and residential applications, driving machinery like pumps, compressors, and conveyors.
-
Core Components
They share fundamental parts such as rotors, stators, and enclosures.
-
Energy Conversion
Both types convert electrical energy into rotational motion to power mechanical systems.
Understanding these commonalities helps highlight that the choice between NEMA and IEC motors often comes down to regional requirements and application-specific needs.
Now, let’s dive into the mechanical differences that set these two motor standards apart.
NEMA motors cannot be used outside of North America because they are incompatible with international standards:False
While NEMA motors are primarily designed for North American markets, they can be used in other regions if the power systems (e.g., voltage and frequency) match. However, they may require additional adaptations to fit international applications, as their dimensions and specifications differ from IEC standards.
IEC motors are designed to meet international standards and are widely used across the globe:True
IEC motors are built to comply with internationally recognized standards, making them suitable for use in Europe, Asia, Africa, and other global markets. Their metric-based designs and adaptability to 50 Hz power systems make them a popular choice worldwide, especially in industries requiring compact and efficient solutions.
Tip: To get more knowledge about the National Electrical Manufacturers Association, please read this article.
Tip: To get more knowledge about the International Electrotechnical Commission, please read this article.

Quiz: Test Your Knowledge of Part 1: "Definition of the Synchronous Motor & Induction Motor"
Learn More about Electric Motors?
LUPMOTORS will send you articles to your Email every week.
100% Free! No Credit Card!
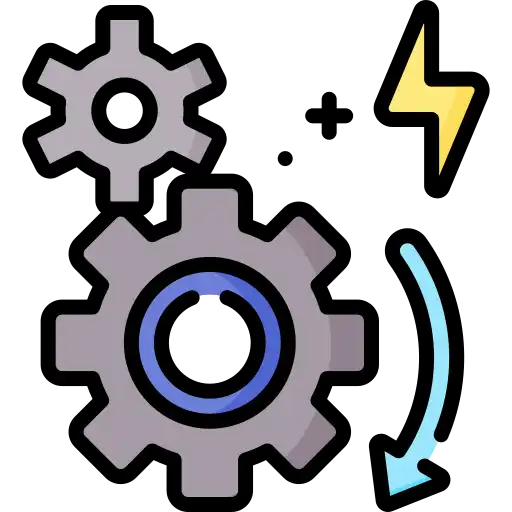
2. Mechanical Differences
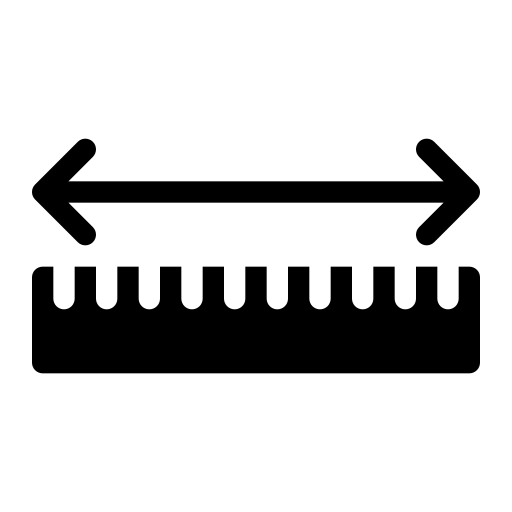
2.1 Frame Sizes: Comparing IEC and NEMA Motors
NEMA and IEC motors differ significantly in their frame sizes and associated mounting dimensions. Below is a comparison table highlighting the frame size and power (kW) standards for three-phase motors under each system:
IEC Frame Size | Shaft Height (mm) | NEMA Frame Size | Equivalent Shaft Height (inches) |
---|---|---|---|
63 | 63 | 56 | 2.5 |
71 | 71 | 143T/145T | 3.5 |
80 | 80 | 182T/184T | 4.5 |
90 | 90 | 213T/215T | 5.25 |
100 | 100 | 254T/256T | 6.25 |
112 | 112 | 284T/286T | 7.0 |
132 | 132 | 324T/326T | 8.0 |
160 | 160 | 364T/365T | 9.0 |
180 | 180 | 404T/405T | 10.0 |
200 | 200 | 444T/445T | 11.0 |
225 | 225 | 447T/449T | 12.25 |
Note: Shaft height is measured from the base of the motor to the centerline of the shaft.
When comparing the frame sizes of IEC and NEMA motors, it’s essential to recognize the fundamental differences in measurement systems and mounting configurations between the two standards.
Measurement Units:

The NEMA standard
NEMA motors,on the other hand, follow the imperial system, with dimensions provided in inches.
For instance, a NEMA frame size 143T motor corresponds to a shaft height of approximately 3.5 inches. This difference in measurement systems can lead to compatibility challenges when replacing motors across standards, particularly in retrofitting scenarios.
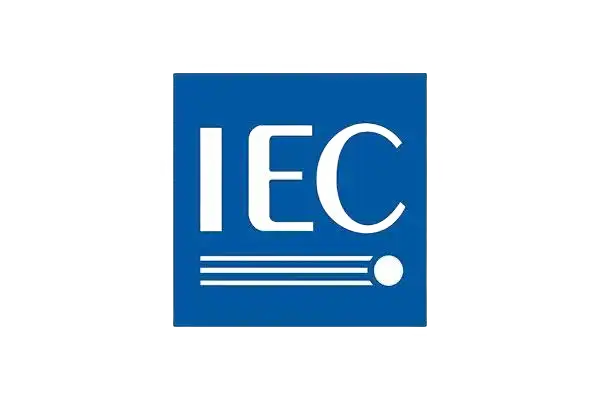
The IEC standard
The IEC standard uses the metric system for frame size specifications, where dimensions are measured in millimeters.
For example, the “shaft height” (the distance from the base of the motor to the center of the shaft) is a key dimension directly tied to the frame size. An IEC motor labeled as frame size 90 has a shaft height of 90 mm.
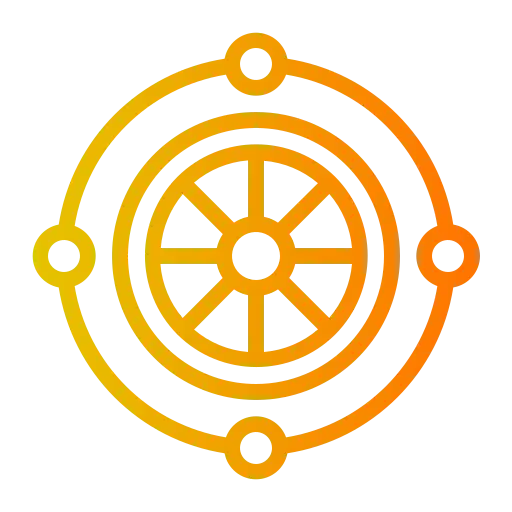
2.2 Mounting Configurations: Fixed vs. Flexible

The NEMA standard
-
NEMA motors typically come in foot-mounted or C-face flange-mounted designs. These configurations are robust and standardized for industrial environments in North America.
-
The dimensions for mounting bolt patterns and shaft heights are consistent across NEMA frame sizes, allowing easy replacement within NEMA-compliant setups.
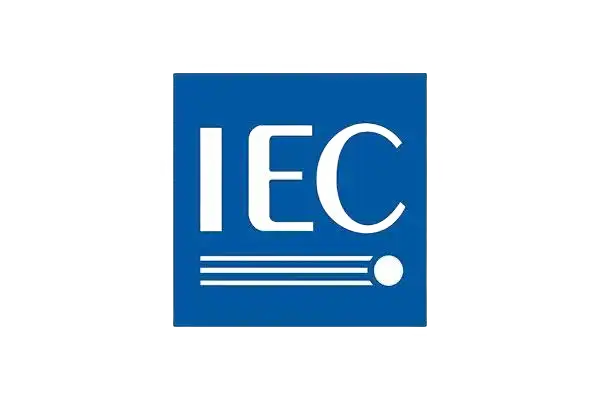
The IEC standard
-
IEC motors offer greater flexibility in mounting options. They are commonly available in foot-mounted, flange-mounted, or foot and flange-mounted configurations, catering to diverse application needs.
-
The metric-based mounting dimensions make IEC motors suitable for global markets, ensuring compatibility with international machinery.
Key Differences in Mounting Practices
Feature | IEC Motors | NEMA Motors |
---|---|---|
Mounting Flexibility | More adaptable; supports multiple configurations | Primarily foot-mounted or flange-mounted |
Mounting Dimensions | Metric-based (e.g., bolt hole patterns in mm) | Imperial-based (e.g., bolt hole patterns in inches) |
Alignment Ease | Suited for international setups with precision | Best for rugged, fixed installations in North America |
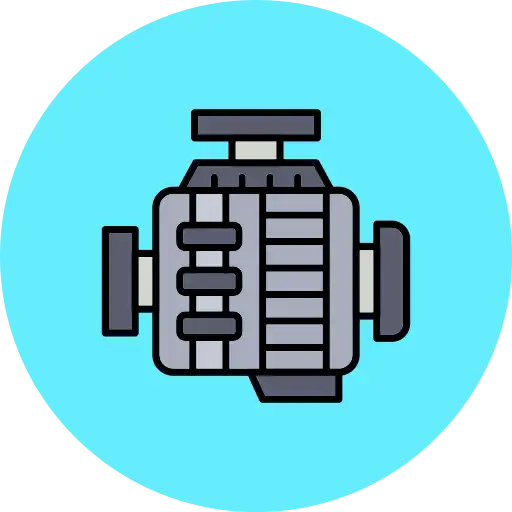
2.3 Enclosure Designs
The design and materials used in motor enclosures play a significant role in protecting internal components and ensuring performance under varying conditions. IEC and NEMA motors differ in both enclosure materials and styles, reflecting their regional design priorities and application environments.

2.3.1 Enclosure Materials

The NEMA standard
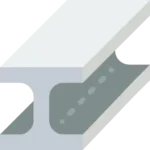
1.Heavy-duty steel
Click it for more contents
NEMA motor enclosures are often constructed from heavy-duty steel or cast iron, designed to endure harsh environments.
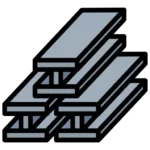
2.Steel enclosures
Click it for more contents
Steel enclosures are frequently used for their superior impact resistance, making them ideal for demanding North American industries like mining or manufacturing.
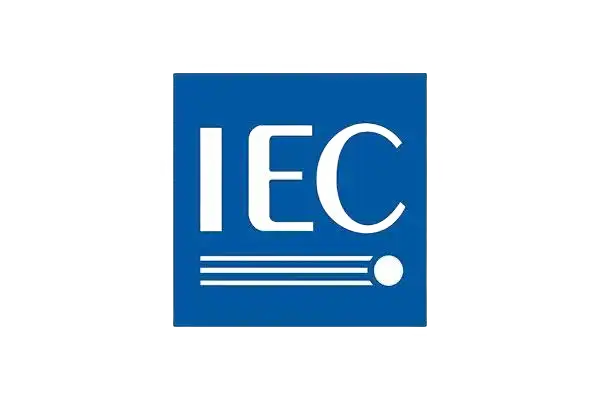
The IEC standard

1.lightweight materials
Click it for more contents
IEC motor enclosures are typically made from lightweight materials like aluminum or cast iron. Aluminum is often used for smaller frames, prioritizing weight reduction and corrosion resistance.
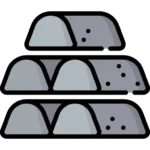
2.Cast iron
Click it for more contents
Cast iron is more common in larger IEC motors, offering enhanced durability for industrial applications while maintaining compatibility with international standards.
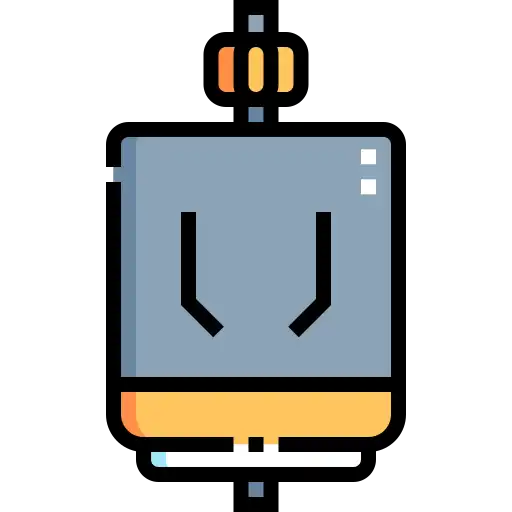
2.3.2 Enclosure Style Designs

The NEMA standard
-
NEMA enclosures are designed for ruggedness and standardization. The style prioritizes durability over compactness, often resulting in larger enclosures than their IEC counterparts.
-
Typical enclosure designs include Totally Enclosed Fan-Cooled (TEFC) for industrial environments and Open Drip Proof (ODP) for less demanding applications.
-
The designs comply with specific NEMA classifications, such as explosion-proof enclosures for hazardous locations, ensuring safety and reliability in heavy-duty operations.
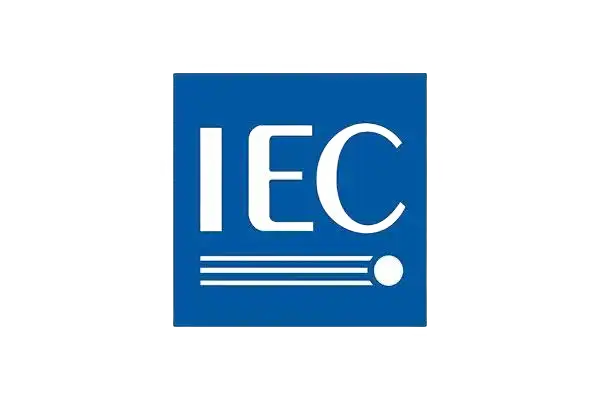
The IEC standard
-
The design of IEC motor enclosures emphasizes compactness and flexibility. This approach allows them to fit into confined spaces, a common requirement in global industrial setups.
-
IEC enclosures often feature modular designs, enabling customization for specific applications, such as additional cooling vents or specialized mounting brackets.
-
IEC standards also accommodate various protection levels (e.g., IP55, IP66), ensuring adaptability to environments ranging from dust-prone workshops to water-exposed locations.
Key Differences in Enclosure Design
Aspect | IEC Motors | NEMA Motors |
---|---|---|
Material | Lightweight aluminum or cast iron | Heavy-duty steel or cast iron |
Design Priority | Compactness, flexibility | Ruggedness, durability |
Protection Standards | IP ratings for dust and water protection | NEMA classifications for specific hazards |
Customization | Modular and adaptable | Standardized for heavy-duty environments |
Understanding these differences can help in selecting a motor that matches your operational needs. IEC motors excel in flexibility and global adaptability, while NEMA motors offer unparalleled durability for heavy-duty applications in harsh environments.
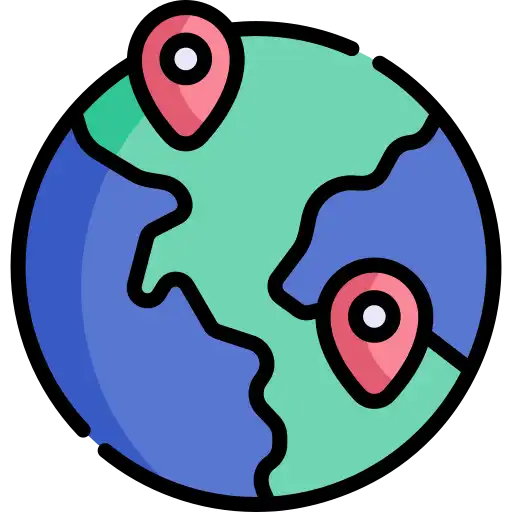
2.4 Regional Adaptability
The global demand for electric motors is shaped by regional standards and application needs. NEMA and IEC motors dominate different parts of the world, reflecting their design priorities and compatibility with local infrastructure. However, recent trends indicate a gradual shift in market dynamics.
Overview of NEMA vs. IEC Standards
NEMA Motors: Stronghold in North America
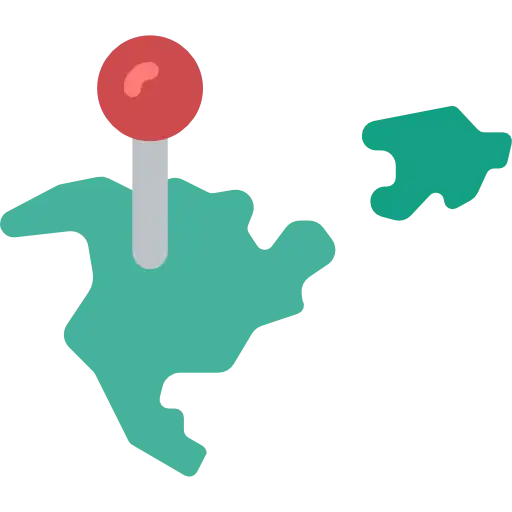
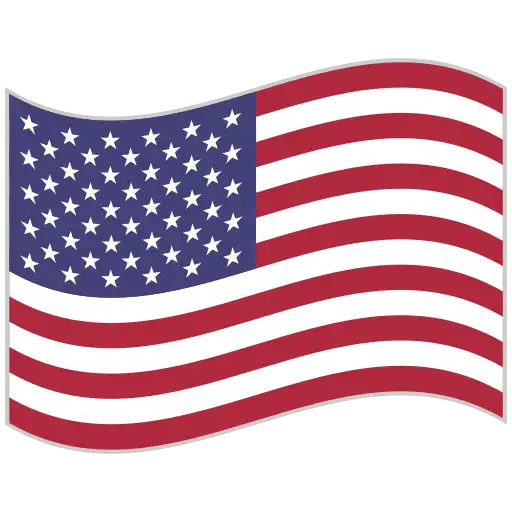
NEMA motors are predominantly used in North America, where they align seamlessly with the region’s power systems and industrial requirements. Their robust design and standardized sizes make them the go-to choice for industries such as:
- Manufacturing: Driving heavy machinery in the U.S. and Canada.
- Agriculture: Powering irrigation and processing equipment.
- Mining and Construction: Operating in harsh conditions with high starting torque demands.
Beyond North America, NEMA motors are occasionally used in Latin America and parts of Asia, where compatibility with 60 Hz power systems is critical. However, their adoption is limited in regions with 50 Hz standards.
IEC Motors: Global Dominance

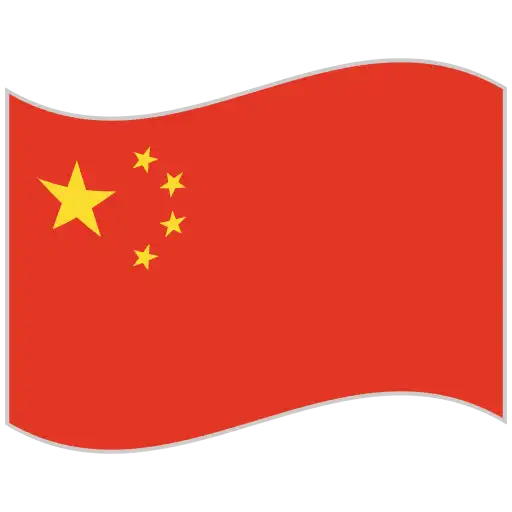
IEC motors are the global standard, with widespread adoption across Europe, Asia, Africa, and South America. These regions prioritize compact designs, energy efficiency, and compatibility with 50 Hz power systems.
- Europe and Asia: IEC motors dominate industrial sectors such as automation, renewable energy, and automotive manufacturing.
- Emerging Markets: Africa and South America are rapidly transitioning to IEC motors due to their adaptability and growing focus on energy efficiency.
The versatility of IEC motors, combined with their advanced efficiency levels (IE4, IE5), has solidified their position in international markets.
In recent years, many industries have begun transitioning from NEMA to IEC motors, driven by globalization and the need for standardized equipment in international operations. This shift is particularly evident in multinational corporations seeking compatibility across facilities in different regions.
- Energy Efficiency: The higher efficiency classifications of IEC motors (IE4 and IE5) appeal to industries aiming to reduce operational costs and meet sustainability goals.
- Market Trends: Emerging economies in Asia and Africa are rapidly adopting IEC motors due to their adaptability and cost-effectiveness.
Market Share and Dominance
IEC motors currently dominate the global market, accounting for approximately 70% of the total motor market share.
NEMA motors hold a significant share in North America, contributing to roughly 20% of global demand.
The remaining 10% is split among other regional standards.
Standard | Market Share | Primary Markets |
---|---|---|
IEC | 70% | Europe, Asia, Africa, South America |
NEMA | 20% | North America, parts of Latin America |
Other | 10% | Regional-specific standards |
IEC motors are the dominant global standard due to their flexibility, energy efficiency, and international compatibility. While NEMA motors maintain a stronghold in North America, the global trend favors IEC motors, with many industries transitioning to this standard to meet modern operational and regulatory requirements.
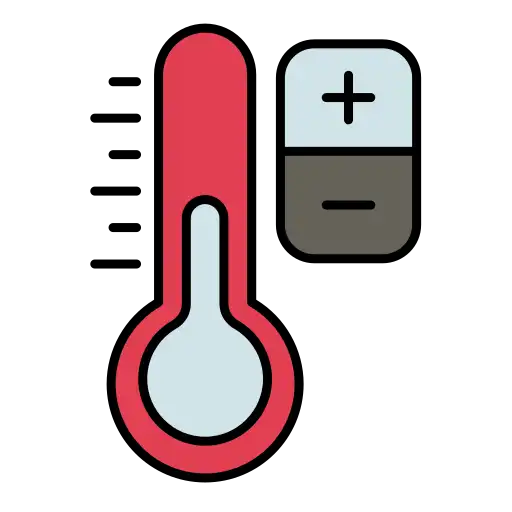
2.5 Ambient Temperature and Insulation Classes
Understanding the insulation classes and their temperature ratings is essential for selecting a motor that can operate efficiently under various environmental conditions. NEMA and IEC motors define insulation classes differently, catering to regional needs and industrial applications.

NEMA Motor Insulation Classes
NEMA motors recognize four primary insulation classes: A, B, F, and H. Each class indicates the maximum temperature the motor’s insulation can withstand without degrading over time.
-
Class A
Designed for maximum temperatures of 105°C. Suitable for low-stress environments like residential HVAC systems.
-
Class B
Rated for 130°C, commonly used in industrial motors with moderate thermal requirements.
-
Class F
Handles temperatures up to 155°C, ideal for motors in high-demand operations like manufacturing plants.
-
Class H
Withstands 180°C, making it suitable for extreme conditions, such as heavy-duty mining equipment.
NEMA Insulation Class | Maximum Temperature (°C) | Typical Applications |
---|---|---|
Class A | 105 | Residential HVAC |
Class B | 130 | Standard industrial motors |
Class F | 155 | Manufacturing, heavy machinery |
Class H | 180 | Extreme environments, mining |
Example:
A Class F NEMA motor operating in a 40°C ambient environment can handle a temperature rise of up to 115°C, ensuring safe and efficient performance.
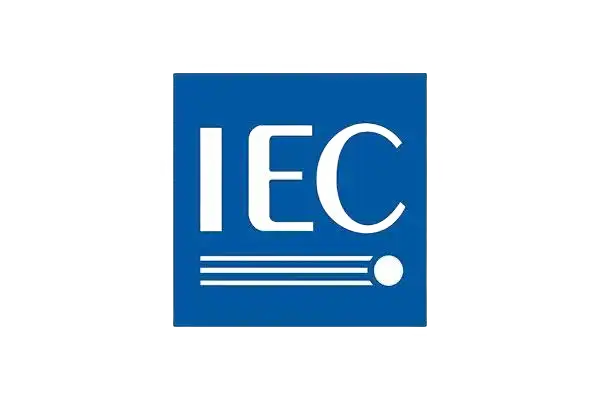
IEC Motor Insulation Classes
IEC motors define eight insulation classes: Y, A, E, B, F, H, C, and N. These classes also represent the thermal limits of the motor’s insulation, offering a more comprehensive range.
Class Y

Maximum temperature of 90°C, used in low-power or temporary motors.
Class A

Rated for 105°C, similar to NEMA Class A.
Class E

Handles temperatures up to 120°C, used in moderate-duty applications.
Class B

Matches NEMA Class B with a limit of 130°C.
Class F

Aligns with NEMA Class F, capable of 155°C.
Class H

Rated for 180°C, like NEMA Class H.
Class C

Designed for 200°C, suitable for very high-temperature applications.
Class N

Can withstand temperatures up to 220°C, used in specialized or extreme environments.
IEC Insulation Class | Maximum Temperature (°C) | Typical Applications |
---|---|---|
Class Y | 90 | Temporary, low-power motors |
Class A | 105 | Residential and light industrial use |
Class E | 120 | Moderate-duty industrial motors |
Class B | 130 | General industrial applications |
Class F | 155 | High-demand operations, manufacturing |
Class H | 180 | Extreme environments, heavy equipment |
Class C | 200 | Very high-temperature machinery |
Class N | 220 | Specialized, high-stress environments |
Example:
An IEC motor with Class B insulation operating in a 40°C ambient environment can handle a temperature rise of up to 90°C, ensuring durability and reliability.
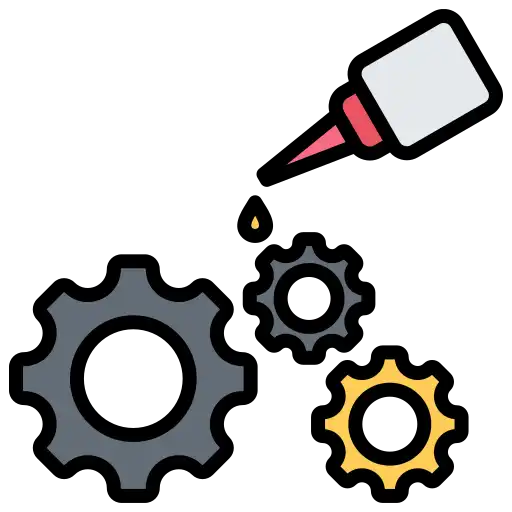
2.6 Differences in Lubricants
Proper lubrication is critical to motor performance and longevity. NEMA and IEC motors use distinct types of grease, reflecting their design and operational requirements. These lubricants are not compatible, and mixing them during maintenance can result in serious issues.

Lubricants Used in NEMA Motors
NEMA motors predominantly use lithium-based grease, chosen for its robust performance under heavy-duty conditions. Key attributes include:
-
High Temperature Tolerance
Handles operating temperatures up to 150°C, making it ideal for demanding environments such as manufacturing and mining.
-
Water Resistance
Provides strong protection against moisture and contaminants, essential for rugged industrial setups.
-
Long Service Life
Reduces the frequency of reapplication, minimizing maintenance downtime.
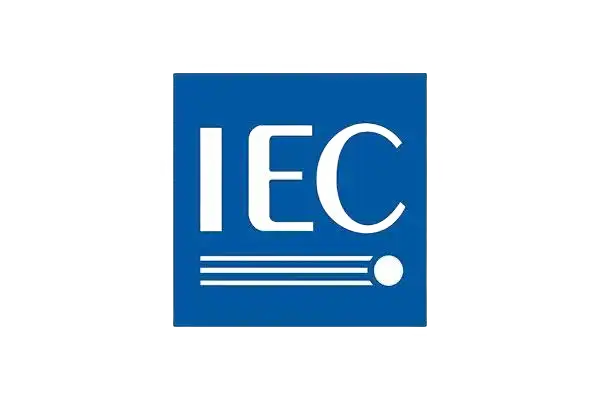
Lubricants Used in IEC Motors
IEC motors are designed for compact, efficient operation and typically use polyurea-based grease. This lubricant offers:
-
Energy Efficiency
Reduces friction and optimizes motor efficiency, aligning with IEC’s focus on sustainability.
-
Broad Temperature Range
Performs reliably between -40°C and 120°C, making it versatile for global applications.
-
Stability
Resists oxidation, extending the lifespan of bearings in motors used for automation, renewable energy, and other applications.
Incompatibility Between NEMA and IEC Lubricants
Lithium-based and polyurea-based greases are chemically incompatible. Mixing them can lead to:
- Grease Degradation: The breakdown of lubrication properties, causing increased wear.
- Bearing Failure: Accelerated component damage due to poor lubrication.
- Overheating: Increased friction and heat, potentially leading to motor failure.
Note:
By adhering to proper lubrication practices, you can protect your motors from unnecessary wear and extend their operational lifespan. Understanding these differences also helps ensure seamless transitions when upgrading or replacing equipment in mixed-standard environments.
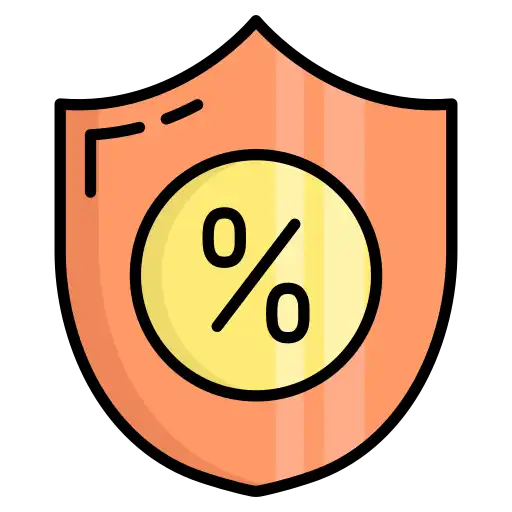
2.7 IP (Ingress Protection) Rating
Ingress Protection (IP) ratings are an internationally recognized standard that defines a motor’s ability to resist the entry of water, dust, and other environmental contaminants. While IEC motors prominently display IP ratings, NEMA motors use alternative classifications to indicate similar protection levels.

NEMA Motors and Protection Standards
NEMA motors do not display IP ratings on their nameplates. Instead, they follow specific enclosure classifications to indicate their protection levels. These classifications are widely recognized in North America and provide equivalent protection to IP ratings.
-
Totally Enclosed Fan Cooled (TEFC)
Comparable to IP54/IP55, this design prevents dust and water from entering while allowing cooling via an external fan.
-
Open Drip Proof (ODP)
Roughly equivalent to IP22, this design allows ventilation but protects against vertical water drips.
-
Hazardous Location Motors
These include explosion-proof designs for environments with flammable gases or dust, offering additional safety beyond standard IP ratings.
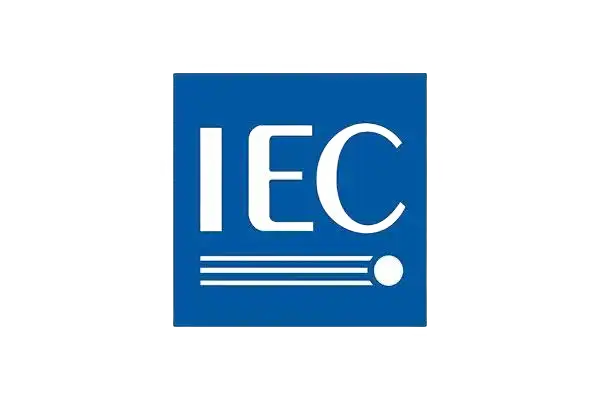
IP Ratings on IEC Motors
-
Display on Nameplate
IEC motors include IP ratings directly on their nameplates, making it simple for users to identify the motor's level of protection.
-
Definition and Structure
The IP rating system, governed by IEC 60529, uses two digits to denote protection levels: 1.The first digit (0-6) specifies protection against solid particles like dust. 2.The second digit (0-9) indicates protection against water ingress.
Examples of IP Ratings
- IP55: Protected against dust and low-pressure water jets, suitable for general industrial environments.
- IP66: Dust-tight and resistant to powerful water jets, ideal for outdoor or wet conditions.
- IP67: Dust-tight and capable of temporary immersion in water, used in specialized applications.
This clear and standardized system ensures IEC motors are suitable for a wide range of environments, from dry workshops to challenging outdoor conditions.
Note:
IEC motors clearly indicate their environmental protection capabilities through standardized IP ratings displayed on the nameplate, providing transparency for global applications. NEMA motors, while lacking IP ratings, achieve equivalent protection through their enclosure classifications, tailored to North American standards. Understanding these systems helps ensure the correct motor is chosen for specific operational environments.

2.8 Cooling Methods: IEC vs. NEMA Motors
Cooling methods ensure that motors maintain optimal operating temperatures during use. While IEC motors use IC (International Cooling) codes to define cooling methods, NEMA motors employ equivalent classifications to describe their cooling systems. Below is a detailed comparison.

NEMA Cooling Methods: Equivalent Classifications
NEMA motors do not use IC codes but provide equivalent cooling classifications based on their design and intended use. Below is a comparison of IEC IC ratings and NEMA classifications:
IEC IC Code | Description | NEMA Equivalent |
---|---|---|
IC411 | Totally enclosed, fan-cooled with an external fan. | Totally Enclosed Fan Cooled (TEFC) |
IC01 | Open motor cooled by ambient air. | Open Drip Proof (ODP) |
IC611 | Closed motor cooled by internal and external fans. | Totally Enclosed Non-Ventilated (TENV) |
IC71W | Water-cooled system. | Water-Cooled Motor |
IC86W | Enclosure with independent water cooler. | Explosion-Proof, Water-Cooled |
Key Insights into Cooling Systems
-
Standardization in NEMA Motors
NEMA focuses on rugged, easy-to-maintain cooling systems, with fewer variations but broad reliability for North American industries.
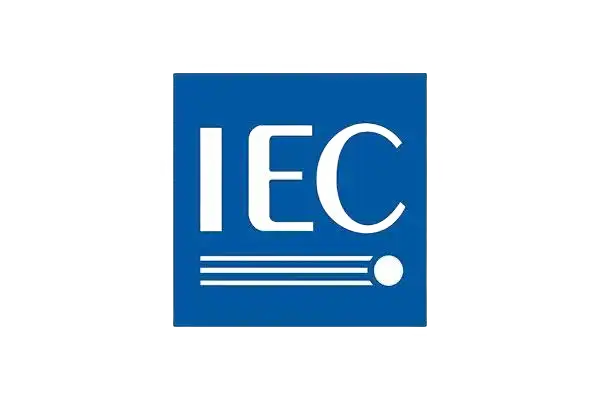
IEC Cooling Methods: IC Ratings
IEC motors follow IEC 60034-6, which uses IC codes to specify the cooling method. The IC rating consists of three to four characters that indicate the type of cooling system. Here are common IC ratings:
IC Code | Description |
---|---|
IC411 | Totally enclosed, fan-cooled with an external fan. Common for general industrial use. |
IC01 | Open motor cooled by ambient air. Suitable for clean environments. |
IC611 | Closed motor cooled by an internal and external fan. Ideal for heavy-duty environments. |
IC71W | Closed motor cooled by a water-based system. Used in applications requiring high cooling efficiency. |
IC86W | Enclosure with an independent water cooler. Often used in high-demand industries like marine or power generation. |
Key Insights into Cooling Systems
-
Flexibility in IEC Motors
The IC system offers greater detail and variety, making IEC motors suitable for highly specific cooling requirements in global applications.
Note:
While IEC motors provide a detailed IC rating system that describes precise cooling mechanisms, NEMA motors achieve similar functionality through simplified but robust classifications. Selecting the right cooling system depends on the operating environment and the motor’s application. This understanding ensures better motor performance and extended operational life.
Tip: To get more knowledge about the NEMA vs. IEC Motor Standards, please read this article.
Tip: To get more knowledge about the NEMA Motor Insulation Classes, please read this article.

Quiz: Test Your Knowledge of Part 2: "Mechanical Differences"

3. Electrical Differences

3.1 Voltage and Frequency
One of the primary differences between NEMA and IEC motors lies in their operating voltage and frequency standards:
NEMA Motors

Commonly operate at 60 Hz and standard voltages like 230V or 460V. These values are optimized for North American power grids.
IEC Motors
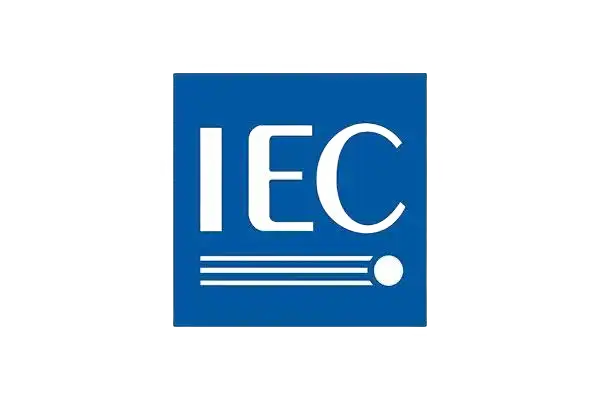
Typically run at 50 Hz and voltages such as 400V or 690V, aligning with international power standards, particularly in Europe and Asia.

3.2 Speed
NEMA Motors
Speed varies based on pole count and 60 Hz frequency, with synchronous speeds like 3600 RPM (2-pole) and 1800 RPM (4-pole).
IEC Motors
Speed is slightly lower due to 50 Hz frequency, with synchronous speeds like 3000 RPM (2-pole) and 1500 RPM (4-pole).
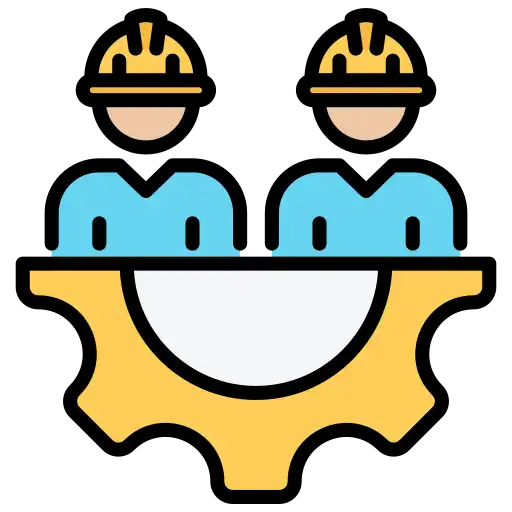
3.3 Torque: Comparing NEMA and IEC Motor Speed-Torque Curves
Torque-speed curves are essential for understanding motor performance under various load conditions. Both NEMA and IEC standards categorize these curves, but they use different designations to describe motor characteristics. Here’s a detailed breakdown:

NEMA Motor Torque-Speed Curve Classifications
NEMA motors classify torque-speed curves using design letters (A, B, C, and D), defined under the NEMA MG1 standard. Each letter represents specific performance characteristics:
-
Design A
Motors with high starting torque and low slip. Ideal for applications requiring rapid acceleration, such as compressors or fans.
-
Design B
The most common type, offering normal starting torque, low starting current, and low slip. Perfect for general-purpose applications like conveyors and pumps.
-
Design C
Provides high starting torque with low slip, making it suitable for heavy starting loads, such as crushers or elevators.
-
Design D
Features very high starting torque and high slip, designed for applications needing substantial torque at low speeds, like hoists or punch presses.
Most Common Type: Design B is widely used in industrial applications due to its balance of performance and efficiency.
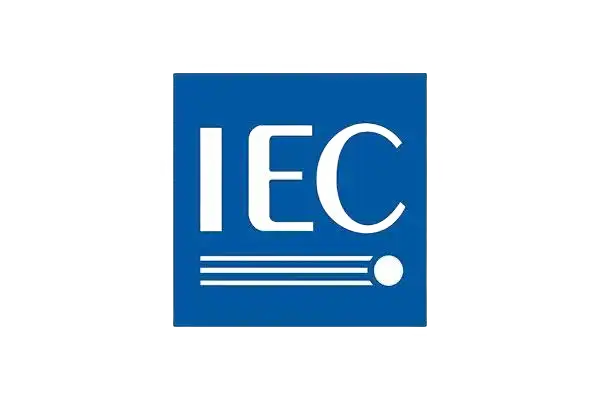
IEC Motor Torque-Speed Curve Classifications
IEC motors classify torque-speed curves using designations N, Y, NY, and HY, as per IEC 60034-12. These classifications indicate the motor’s torque and slip characteristics:
-
Design N (Normal Torque)
Motors with standard starting torque and low starting current, comparable to NEMA Design B. Commonly used for general-purpose applications.
-
Design Y (High Starting Torque)
Motors with high starting torque and moderate starting current, similar to NEMA Design C. Suitable for applications requiring higher startup torque.
-
Design NY (Very High Starting Torque)
Provides very high starting torque and higher starting current, comparable to NEMA Design D. Used in demanding startup conditions.
-
Design HY (Extremely High Starting Torque)
Offers extremely high starting torque and high starting current, designed for heavy-duty applications with significant load inertia.
Most Common Type: Design N is the standard for IEC motors, widely used for industrial and commercial setups.
Comparison of NEMA and IEC Torque-Speed Curves
IEC Designation | Characteristics | NEMA Equivalent |
---|---|---|
Design N | Normal starting torque, low starting current | Design B |
Design Y | High starting torque, moderate starting current | Design C |
Design NY | Very high starting torque, higher starting current | Design D |
Design HY | Extremely high starting torque, high starting current | No direct equivalent |
- General Applications: NEMA Design B and IEC Design N are the most common, providing balanced performance for a wide range of uses.
- Heavy Starting Loads: NEMA Design C and IEC Design Y offer high starting torque, suitable for equipment with demanding startup requirements.
- Demanding Torque Needs: NEMA Design D and IEC Design NY cater to applications with significant load inertia, such as hoists or punch presses.
Note:
By understanding these classifications, you can ensure compatibility and optimal motor performance for your specific application, whether adhering to NEMA or IEC standards.
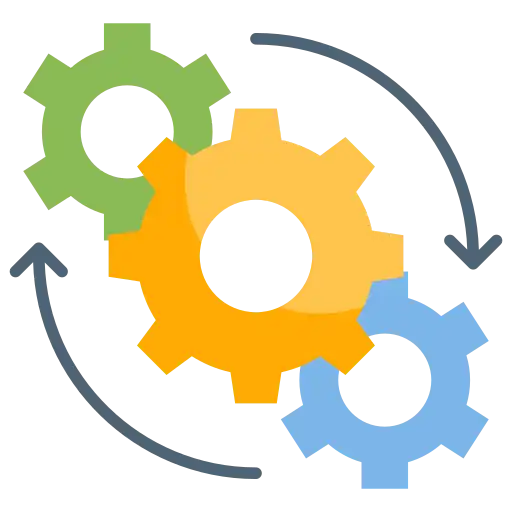
3.4 Duty Cycle: Comparing IEC and NEMA Standards
The duty cycle of a motor describes its operational pattern, including load and rest periods. Both IEC and NEMA standards classify duty cycles, but they differ in definitions and applications. Below is a detailed comparison.
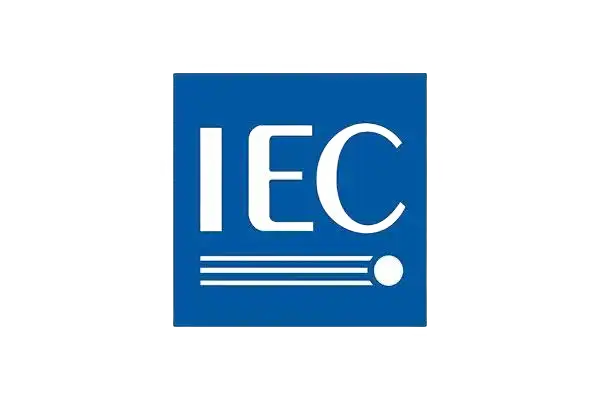
IEC Standard Duty Cycles
IEC motors classify duty cycles using codes S1 to S10, defined under IEC 60034-1. Each code describes specific operating conditions.
IEC Duty Cycle | Description |
---|---|
S1 (Continuous Duty) | Operation under constant load for a duration sufficient to reach thermal equilibrium. Ideal for industrial pumps and fans. |
S2 (Short-Time Duty) | Operation under constant load for a short time, insufficient to reach thermal equilibrium, followed by a rest period. |
S3 (Intermittent Periodic Duty) | Sequential cycles of operation and rest, with no thermal equilibrium reached. Typically expressed as a percentage of on-time (e.g., S3-40%). |
S4 (Intermittent Periodic Duty with Starting) | Similar to S3 but includes significant starting phases, common in cranes and hoists. |
S5 (Intermittent Periodic Duty with Electrical Braking) | Like S4 but includes braking phases during operation, suitable for applications like elevators. |
S6 (Continuous Duty with Periodic Load Variations) | Continuous operation with periodic load changes, such as in compressors or conveyors. |
S7 (Continuous Duty with Starting and Braking) | Continuous operation involving frequent starts and electrical braking, used in presses and heavy machinery. |
S8 (Continuous Duty with Load and Speed Variations) | Operation with continuous load and speed changes, such as in rolling mills. |
S9 (Duty with Non-Periodic Load and Speed Variations) | Non-periodic duty cycles with high overloads, used in test facilities or variable industrial processes. |
S10 (Duty with Discrete Load/Speed Changes) | Defined duty cycles with specific load and speed points, designed for highly specialized applications. |
Example:
A Class F NEMA motor operating in a 40°C ambient environment can handle a temperature rise of up to 115°C, ensuring safe and efficient performance.

NEMA Standard Duty Cycles
NEMA motors define duty cycles based on specific operational periods and conditions, with classifications that differ from IEC standards. Common classifications include:
-
Continuous Duty
Corresponds to IEC’s S1, where the motor operates continuously under a constant load until thermal equilibrium is reached.
-
Intermittent Duty
Similar to IEC’s S3, where the motor operates for a specified time followed by a rest period, often expressed as a percentage (e.g., 30 minutes ON, 30 minutes OFF).
-
Short-Time Duty
Comparable to IEC’s S2, operating under a constant load for a limited period without reaching thermal equilibrium.
-
Varying Duty
Includes conditions with load and speed variations but lacks the detailed classifications found in IEC’s S6-S10.
Unlike IEC’s detailed segmentation, NEMA provides broader classifications, focusing on general operational patterns rather than specific load and speed combinations.
Aspect | IEC Standards (S1-S10) | NEMA Standards |
---|---|---|
Continuous Duty | S1: Constant load until thermal equilibrium | Continuous Duty: Equivalent to S1 |
Short-Time Duty | S2: Limited operation under constant load | Short-Time Duty: Similar to S2 |
Intermittent Duty | S3: Cycles of operation and rest | Intermittent Duty: Similar but less detailed |
Load/Speed Variations | S6-S10: Detailed classifications for variations | Varying Duty: General variations without detailed codes |
Key Differences
- Detail and Specificity: IEC provides more detailed classifications (S6-S10) for varying loads and speeds, making it suitable for specialized applications.
- Simplicity: NEMA classifications are simpler, focusing on broader categories, which can make them easier to apply in less complex scenarios.
By understanding these classifications, you can better select a motor that aligns with your application’s operational patterns, ensuring reliability and efficiency whether adhering to IEC or NEMA standards.
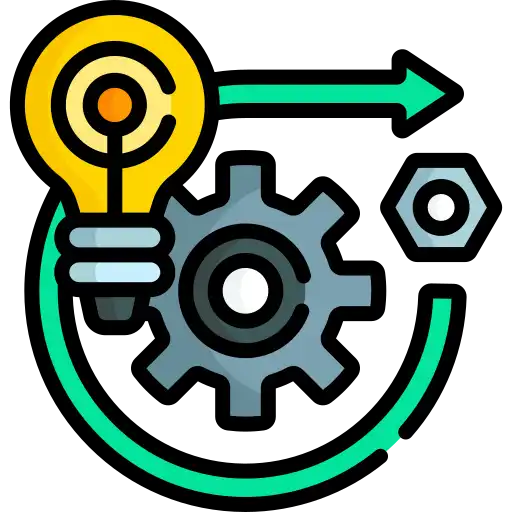
3.5 Service Factor (SF): Comparing NEMA and IEC Standards
The Service Factor (SF) is a multiplier that indicates the motor’s ability to handle occasional overloads beyond its rated capacity without overheating or experiencing damage. It provides a safety margin for motors, ensuring reliability under varying load conditions.

Service Factor in NEMA Motors
Definition
NEMA defines the Service Factor as the motor’s capacity to operate above its nominal horsepower rating without failure. For example, a motor with a 1.15 SF can handle 15% more load than its rated capacity.
Typical Values:
-
General-Purpose Motors
Commonly have a 1.15 SF for standard industrial applications.
-
Severe Duty Motors
Often feature higher SF values, such as 1.25, to handle more demanding conditions.
Benefits
The SF allows temporary overloads, accommodates minor power supply fluctuations, and adds an extra layer of safety for unexpected operational demands.

Application
NEMA motors with higher SF are ideal for industries with fluctuating loads, such as
- pumps
- compressors
- conveyors
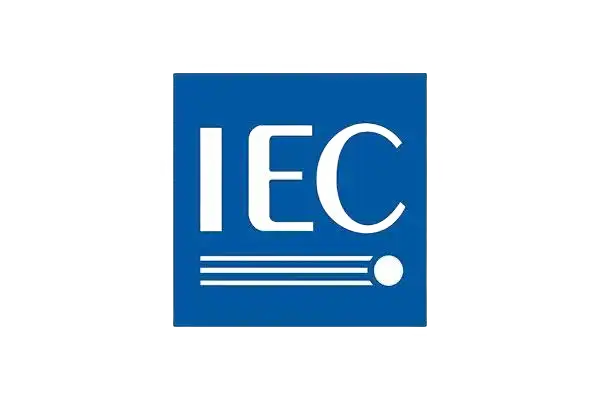
Service Factor in IEC Motors
Definition
Unlike NEMA, IEC standards do not use the concept of Service Factor as a standard parameter. Instead, IEC motors are designed to operate at their rated capacity under specified conditions without exceeding the rated temperature rise.
Approach
-
IEC motors emphasize strict adherence to performance limits rather than allowing temporary overloads.
-
Operating a motor beyond its rated load is not recommended under IEC standards, as it may lead to overheating and reduced efficiency.
Design Philosophy
IEC motors focus on efficiency and reliability, ensuring that motors operate within their defined parameters for optimal performance and longevity.
Key Differences Between NEMA and IEC Service Factors
Aspect | NEMA Motors | IEC Motors |
---|---|---|
Service Factor (SF) | Explicitly defined, typically 1.15 or higher | Not a standard parameter; operates strictly at rated capacity |
Overload Capability | Allows temporary overloads | No overload capability specified |
Design Focus | Flexibility for varying loads | Precision and efficiency within rated limits |
Application | Ideal for fluctuating loads | Best for steady, predictable applications |
Scope | loads | Best for steady, predictable applications |
NEMA motors offer greater flexibility with their Service Factor, making them suitable for operations with variable loads or occasional overloads. In contrast, IEC motors prioritize precise performance within rated limits, reflecting a design philosophy focused on efficiency and reliability. Understanding these differences ensures the appropriate motor is chosen based on the operational demands of your application.
Tip: To get more knowledge about the Duty Cycle, please read this article.
Tip: To get more knowledge about the Service Factor (SF), please read this article.

Quiz: Test Your Knowledge of Part 3: "Electrical Differences"
Question 1: What frequency are NEMA motors typically designed for?
Question 2: Which voltage range is commonly associated with IEC motors?
Question 3: NEMA motors are more likely to use which type of wire connection for low voltage?
Question 4: What is the common starting configuration for IEC motors to reduce inrush current?
Question 5: What is a key difference in voltage standards between NEMA and IEC motors?
Question 6: Which characteristic is commonly associated with NEMA Design B motors?
Question 7: IEC motors prioritize which feature in their electrical design?
Question 8: Which duty cycle classifications include variations in speed and load?
Question 9: What does the Service Factor (SF) in NEMA motors represent?
Question 10: Which motor standard is more likely to use advanced efficiency ratings like IE4 and IE5?
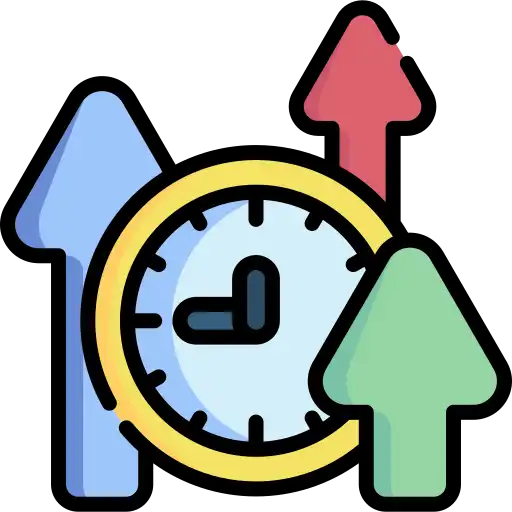
4. Efficiency Standards
Energy efficiency is a critical factor when choosing between NEMA and IEC motors. Both standards prioritize reducing energy consumption, but their approaches differ based on regional regulations and industry needs.

NEMA Premium Efficiency
NEMA Premium motors adhere to the NEMA MG1 Standard, designed to optimize energy savings in industrial applications. These motors often exceed minimum efficiency levels set by the U.S. Department of Energy (DOE).
-
Efficiency Levels
NEMA Premium motors achieve efficiencies 2-3% higher than standard motors, particularly in sizes above 1 horsepower.
-
Key Applications
Frequently used in HVAC systems, pumps, and compressors where long operational hours amplify energy savings.
-
Regulatory Context
Compliance with U.S. DOE efficiency mandates and incentives for high-efficiency equipment adoption.
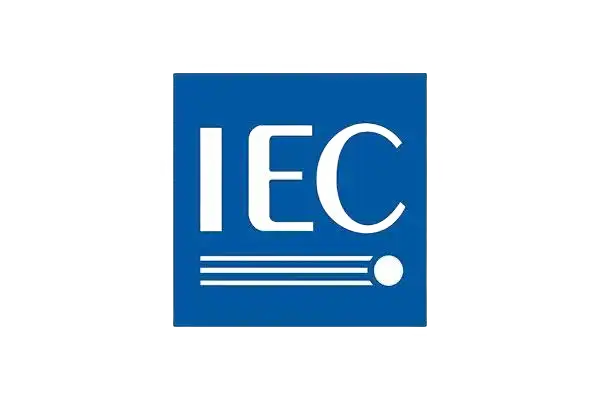
IP Ratings on IEC Motors
IEC motors follow the IE (International Efficiency) classification, which includes several levels of efficiency:
Efficiency Level | Description | Typical Applications |
---|---|---|
IE1 (Standard) | Basic efficiency | Cost-sensitive applications |
IE2 (High) | Improved efficiency | General-purpose motors |
IE3 (Premium) | Mandatory in many regions | Industrial machinery and long-duty applications |
IE4 (Super Premium) | Further improved efficiency | Energy-critical operations |
IE5 (Ultra Premium) | Cutting-edge performance | Future-focused, high-efficiency systems |
Source: IEC 60034-30-1 Guidelines
NEMA Premium Efficiency
- NEMA vs. IEC Standards: IE3 (Premium) aligns closely with NEMA Premium, offering comparable energy savings. However, IEC’s IE4 and IE5 levels push efficiency standards even further.
- Global Trends: With energy regulations tightening globally, motors at IE3 or higher are increasingly favored, particularly in regions enforcing stricter efficiency laws.
Note:
By choosing motors that align with these standards, industries can significantly cut energy costs while meeting sustainability goals. Let’s now examine the pros and cons of NEMA and IEC motors.

Quiz: Test Your Knowledge of Part 4: "Efficiency Standards"
1. Which standard defines energy efficiency levels for NEMA motors?
2. What is the highest efficiency classification for IEC motors?
3. Which efficiency level is mandatory for motors sold in many regions in Europe?
4. How do NEMA Premium motors compare to IEC motors in terms of efficiency?
5. What is one advantage of higher-efficiency motors like NEMA Premium or IEC IE4/IE5?
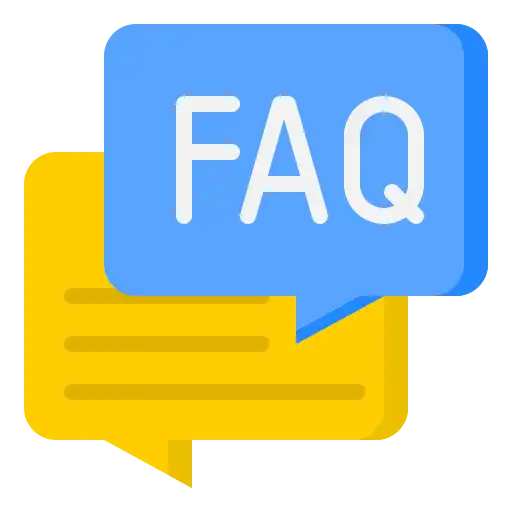
5. FAQs about Electric Motor Nameplates
What are the key differences between NEMA and IEC motors?
NEMA motors are designed primarily for North American markets, adhering to NEMA MG1 standards with a focus on robust construction and high starting torque. IEC motors, governed by IEC 60034 standards, are globally compatible, emphasizing compact design and energy efficiency. Key differences include frame sizes, voltage and frequency standards, and mounting configurations.
Which motor type is better for my industry?
It depends on your region and application needs. For heavy-duty operations in North America, such as manufacturing or mining, NEMA motors excel with their rugged build and high torque. IEC motors are ideal for global applications requiring compact designs, energy efficiency, and compatibility with international power systems.
How do efficiency standards compare?
NEMA motors follow the NEMA Premium standard, comparable to IE3 efficiency in IEC motors. However, IEC offers advanced levels like IE4 and IE5, which deliver greater energy savings. If energy efficiency is a priority, IEC motors may offer long-term cost benefits.
What are the cost differences between NEMA and IEC motors?
NEMA motors often have a higher upfront cost due to their larger size and robust materials. IEC motors, being more compact, are generally more affordable initially. However, IEC motors’ superior energy efficiency can result in lower operational costs over time, balancing the total cost of ownership.
We offer customized motor solutions to meet your specific application requirements
LUPMOTORS offers ac low voltage 3-phase asynchronous industrial motors of all types – Please contact us freely.
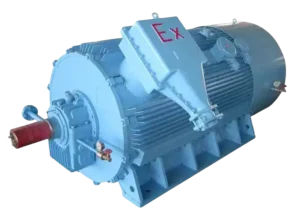
A Selection Guide for Explosion Proof Motors
Learn how to choose the right explosion-proof motor for hazardous locations. Understand classifications, T-Codes, and certifications to ensure safety and compliance!
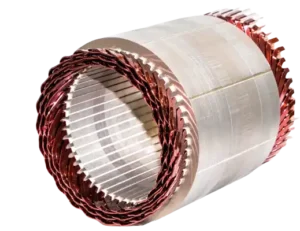
Structure of Electric Motors | The Complete Guide
Discover the structure of electric motors, from stators and rotors to windings and bearings. Learn how materials impact efficiency, performance, and lifespan!
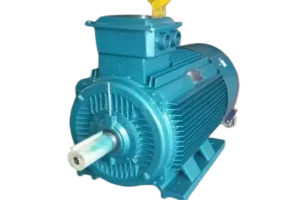
Motor Thermal Overload Protection | The Complete Guide
“Discover how motor thermal overload protection works, why it matters, and how to choose the right protector. Plus, take our quiz to test your knowledge!”
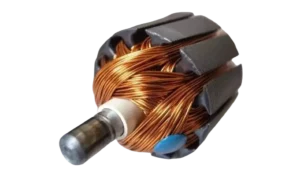
Brushed Motors vs. Brushless Motors: The Complete Guide
“Explore brushed vs. brushless motors: key differences, pros, cons, and which one fits your needs best!”
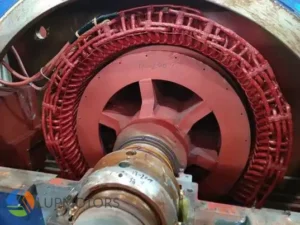
How to Test an Electric Motor: Tools, Methods & Procedures
Learn how to test electric motors with expert tools and methods. Discover step-by-step guides for insulation, resistance, and running current tests to ensure peak performance!
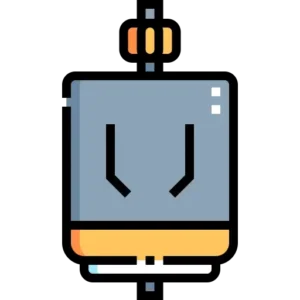
NEMA Motors vs IEC Motors: The Definitive Guide
“Explore the ultimate guide to NEMA vs. IEC motors. Learn key differences, efficiency standards, applications, and choose the right motor for industrial success.”