When you operate a three-phase motor in a explosive dangerous environment, safety is always your primary concern.
Lack of understanding of the classification of dangerous areas may accidentally increase the risk of you and colleagues.
Thoroughly learning explosion-proof knowledge is not only a choice, it is the key to distinguish between safety and disasters.
Therefore, you need to understand the classification of various dangerous areas in depth, which is particularly important.
This article will fully analyze different categories and levels to help you accurately identify potential explosion risks and take necessary safety measures.
Whether you are operating a three -phase or different motor or any other equipment, this comprehensive security guide will be the help of you to control these vital safety standards.
What is a Hazardous Location?
Hazardous location usually refers to areas with potential explosions or fire risks due to flammable gas, steam or flammable dust.
Typical industries involving such environments include oil and natural gas, chemical processing, flour grinding, textiles, and mining industries.
In these occasions, the classification and certification of HAZLOC materials is essential for ensuring the safe operation of equipment and preventing catastrophic accidents.
The specific classification of hazardous places is determined by various professional organizations and management agencies, providing clear operation guidance with standardized safety measures and providing clear operation guidance.
About NEC & IEC
Multiple international organizations and management agencies have clearly classified dangerous places.
The National Fire Association (NFPA) defines specific categories, levels, and groups through the National Electrical Specification (NEC).
The International Electricity Commission (IEC) provides a classification standard for areas and groups of dangerous places equipment.
Both provide clear guidance to ensure safe operation.
Division | Zone | Class
NEC divides hazardous location into
- Division
- Zone
- Class
while IEC adopts a regional and group partition system.
In order to avoid confusion, the level of NEC is determined according to the existence of danger during normal and abnormal operations, such as distinguishing daily operation and maintenance or failure to eliminate tasks.
The regional division of IEC is defined according to the frequency or duration of danger.
Overview of the Classification System for Hazardous Location
In order to ensure your safety in a dangerous environment, you can take various types and combination of preventive measures.
Here are some common preventive measures related to different NEC categories, levels, and groups. These measures include:
Classification System of Dangerous Places
Category I: Finy Gas or Vapor Environment
- Grounding and bonding: Make sure that electrical equipment and all electrical materials are correctly grounded and bonded to prevent the static accumulation from sparking.
- Explosion -proof shell: Use a dedicated shell that can withstand and close the internal explosion to ensure that the explosion does not spread outward.
- Internal safety equipment: choose low energy consumption equipment to minimize the risk of spark or overheating.
Class II: Flammable Dust Environment
- Regular cleaning and management: Keep the environment clean and clean up to reduce the accumulation of flammable dust.
- Install an effective dust collection system, timely capture and clear the dust particles in the air to prevent dust from gathering on the equipment and surface.
- Anti -spark tool: uses tools made of anti -spark materials to reduce the risk of fire caused by sparks.
Class III: Combustible fiber or flying flocculent environment (such as cotton or sawdust)
- Regular maintenance and inspection: Routine inspections, timely discover and repair potential fire sources to prevent fires from occurring.
- Correctly stored and dealt with: Save flammable fiber or flying flocculent in a specified container, and formulate procedures to prevent its accumulation and contact with fire source.
- Use flame retardant: Workers should wear flame retardant clothing to ensure that the risk of spreading the fire spreads to the minimum when unexpected fire occurs.
Gas, vapor or liquid
- Zone 0: This is a area with flammable concentrations that exceed 1,000 hours of flammable concentration every year.
- Zone 1: In this area, the annual flammable gas, steam or liquid reaches the flammable concentration between 10 to 1,000 hours.
- Zone 2: This area usually does not occur under normal operating conditions. Under normal operating conditions, flammable concentrations are reached under normal operating conditions, or the annual occurrence of less than 10 hours.
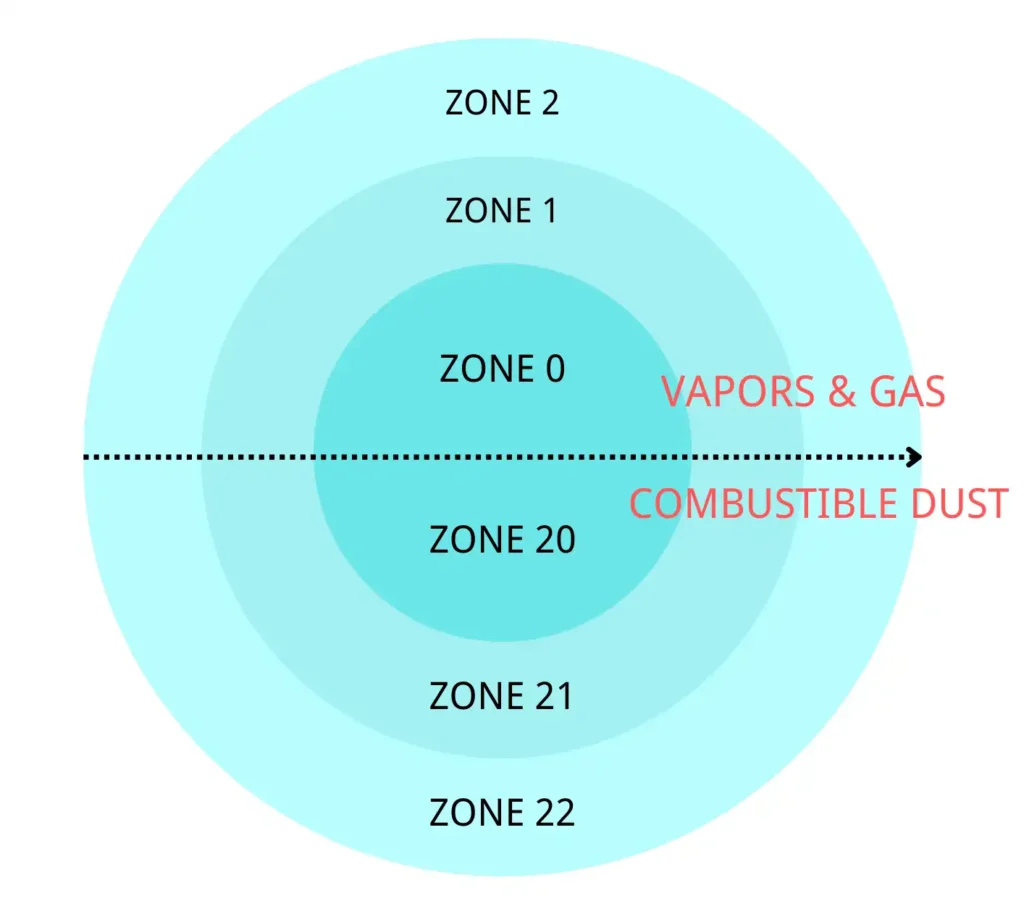
Combustible Dust
- Zone 20: This is a area where combustible dust is continuously released in the dustproof shell. The air will continue or frequently appear in the air to form an explosive environment. For example, the operating area of the milling machine or the pneumatic conveyor system.
- Zone 21: In this area, it may occasionally form an explosive environment in normal operation, usually in the form of combustible dust clouds in the air. For example, frequently open bags and check ports.
- Zone 22: This is a sub -release area. It is unlikely to form an explosive environment in normal operation. Even if it appears, it will only continue for a short time. For example, a small amount of leakage or overflow caused by improper installation of the lid.
NEC Classification for Hazardous Location
Based on the possibility and duration of hazardous substances, the dangerous areas are classified. Corresponding prevention measures include:
Class I: The environment where dangerous substances often exist
- Strict entry and exit control: By locking doors, security agreements, and comprehensive training, the entry and exit permissions are limited, and authorized personnel can be allowed to enter.
- Continuous monitoring: Gas detectors, dust monitoring systems, and automatic alerts are used to monitor potential danger in real time to ensure that response measures can be taken immediately to quickly evacuate.
- Special ventilation system: Configure explosion -proof fan, special pipeline system and airflow control device to maintain safe working conditions.
Class II: The environment where the dangerous substance exists only under abnormal conditions
- Equipment inspection and maintenance: regular inspections and maintenance equipment, identify and repair potential fire sources in time to prevent accidents.
- Regular cleaning: Keep the environment neatly clean, remove flammable dust regularly to prevent it from accumulating on the surface of the equipment and reduce the risk of fire.
- Emergency response plan: formulate detailed emergency response procedures to deal with leakage, faults or other emergencies. Ensure that employees receive full training, maintain a stable communication system, and plan clear evacuation routes.
Conditions of hazardous substances
NEC Classification
Class I | There is danger in normal operation. |
Class II | There are few dangers or only in the state of abnormal operation. |
IEC Zone
Zone 0 | Dangerous gases or dust exist for a long time. |
Zone 20 | The same as above |
Zone 1 | There may be dangerous gas or dust in normal operation. |
Zone 21 | The same as above |
Zone 2 | During the normal operation period and in a short period of time, it is unlikely to exist in dangerous gases or dust. |
Zone 22 | The same as above |
Hazardous Location Marks
The HAZLOC mark is a graphic representation to convey important information about dangerous places.
Generally, these marks consist of two parts: pictographs and letters numbers.
Pixel diagrams directly show the type of danger through visual symbols, such as explosions or fires, and the alphabet digital code provides more detailed information, including the category, level, and groups of hazardous materials.
Although the basic principles of the HAZLOC symbol are roughly the same in different standards, there are still some differences between NEC, ATEX and CSA in specific applications.
Types of Protection
TYPE | MARK | ZONE | DESCRIPTION |
Intrinsic Safety | ia ib ic | Zone 0 Zone 1 Zone 2 | The design restricts the energy inside the device to prevent fire caused by spark or overheating, thereby ensuring safe operation in the potential explosive environment. |
Fireproof | da db dc | Zone 0 Zone 1 Zone 2 | In order to prevent the design of flames and heat gas, ensure that any internal explosion is safely controlled inside the device. |
Increased Safety | eb ec | Zone 1 Zone 2 | By enhancing the functions of insulation, protecting the shell and temperature control, further improve the overall safety. |
Sparkless | nA | Zone 2 | There will be no equipment that is sufficient to ignite or high temperatures that ignite flames or vapor. |
Full Seal | nC | Zone 2 | There will be no equipment that is sufficient to ignite or high temperatures that ignite flames or vapor. |
Energy Limited | nL | Zone 2 | There will be no equipment that is sufficient to ignite or high temperatures that ignite flames or vapor. |
Breathing Limited | nR | Zone 2 | There will be no equipment that is sufficient to ignite or high temperatures that ignite flames or vapor. |
Dust & Ignition-proof | ta tb tc | Zone20 Zone21 Zone22 | The structure and design of the device minimize the risk of dust -related explosions or fires in dangerous places with flammable dust. |
Purged and Pressurized | pxb pyb pzc | Zone1,2 Zone1,2 Zone 2 | By maintaining positive pressure in the shell, prevent harmful gases or dust from entering the device. |
Liquid soaking | ob oc | Zone 1 Zone 2 | The equipment is soaked in protective liquids (such as oil) to prevent fire in the explosive environment outside the shell. |
Seal | ma mb mc | Zone 1 Zone 2 Zone 3 | The equipment is encapsulated in the resin material to prevent the fire from spark or overheating. |
Ignition Classification
The fire characteristics define the materials that can be used in the state of dangerous operation.
These materials are divided into different categories and groups according to the NEC classification system, and they are divided into different groups based on the IEC partition system.
Ignition Classification for NEC
Material | Classification |
Acetylene | Class I, Group A |
Hydrogen | Class I, Group B |
Ethylene | Class I, Group C |
Propane | Class I, Group D |
Methane (Mines) | / |
Metal Dusts | Class II, Group E |
Coal Dusts | Class II, Group F |
Grain Dusts | Class II, Group G |
Fibers/Flyings | Class III |
Ignition Classification for IEC
Material | Classification |
Acetylene | IIC |
Hydrogen | IIC |
Ethylene | IIB |
Propane | IIA |
Methane (Mines) | I |
Conductive Dusts | IIIC |
Non-conductive Dusts | IIIB |
Inflammable Flyings | IIIA |
Preventive measures
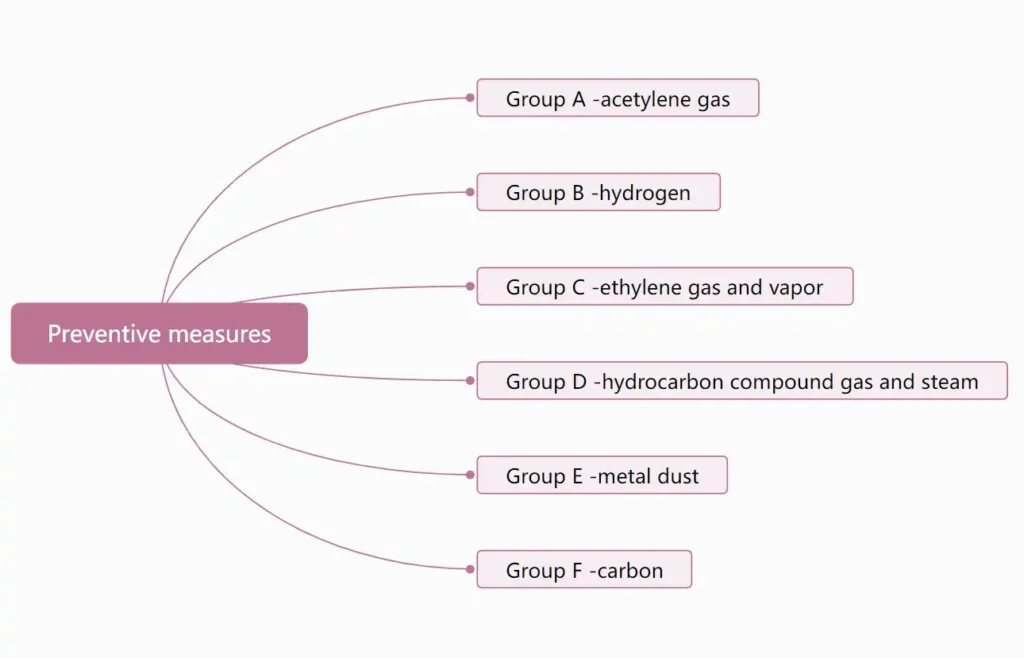
Group A -acetylene gas
- Correctly ground and bond
- Fully ventilation
- Explosion -proof shell
Group B -hydrogen
- Correctly curb and leak detection
- Continuous ventilation
- Regular inspection and maintenance equipment
Group C -ethylene gas and vapor
- Correctly ground and bond
- Use explosion -proof shell
Group D -hydrocarbon compound gas and steam, such as gasoline
- Eliminate potential fire sources
- Regular inspection and maintenance equipment
- Effective grounding and bonding
Group E -metal dust, such as aluminum or magnesium
- Effective dust collection system
- Regular cleaning equipment
- No spark tools and equipment
Group F -carbon -containing dust, such as coal, charcoal or coke dust dust
- Dust control measures
- Regular affairs management
- Dangerous material treatment
Group G -Group -E or F groups that are not covered with flammable dust, such as grain dust, wood chips and plastic dust
- Dust reduction strategy
- Regular inspection and maintenance
- Employee training and consciousness: This should cover the correct processing, storage and cleanup procedures.
Temperature Classification
Maximum surface temperature
American Standard
T1 | 450°C | 842°F |
T2 | 300°C | 572°F |
T2A | 280°C | 536°F |
T2B | 260°C | 500°F |
T2C | 230°C | 446°F |
T2D | 215°C | 419°F |
T3 | 200°C | 392°F |
T3A | 180°C | 356°F |
T3B | 165°C | 329°F |
T3C | 160°C | 320°F |
T4 | 135°C | 275°F |
T4A | 120°C | 248°F |
T5 | 100°C | 212°F |
T6 | 85°C | 185°F |
International Standard
T1 | 450°C |
T2 | 300°C |
T2A | / |
T2B | / |
T2C | / |
T2D | / |
T3 | 200°C |
T3A | / |
T3B | / |
T3C | / |
T4 | 135°C |
T4A | / |
T5 | 100°C |
T6 | 85°C |
Equipment Protection Level (EPL)
The Equipment Protection Level (EPL) is an important indicator of the potential for equipment to become a source of ignition.
According to the IEC/EN 60079 standard, the EPL is determined by evaluating the risk factors of ignition sources in the equipment under normal and abnormal operating conditions.
Material | ATEX Group | EPL | Zone |
Air | 1G | Ga | Zone 0,1,2 |
Air | 2G | Gb | Zone 1,2 |
Air | 3G | Gc | Zone 1 |
Dust | 1D | Da | Zone 20,21,22 |
Dust | 2D | Db | Zone 21,22 |
Dust | 3D | Dc | Zone 22 |
Mining | M1 | Ma | / |
Mining | M2 | Mb | / |
Regulatory Bodies of HazLoc classes
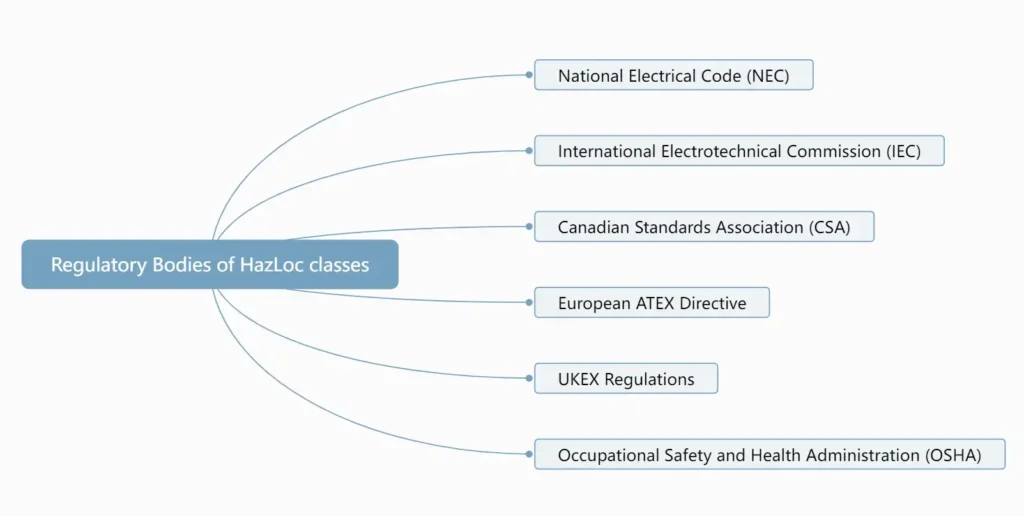
These certification and regulatory bodies play a key role in the development and standardization of HazLoc classifications, groups and classes, providing clear guidelines and requirements for ensuring the safety and compliance of equipment within hazardous areas.
Each regulatory body develops standards that meet the specific needs and regulations of its region and industry, based on their focus, coverage and jurisdiction.
National Electrical Code (NEC)
The National Electrical Code (NEC) is an industry-widely recognized standard used primarily for electrical installations in hazardous locations in the United States.
It provides guidelines and requirements for the creation of HazLoc classifications, groupings, and classifications to ensure the safe operation of electrical equipment in these environments.
A distinguishing feature among the NEC is its special focus on electrical installations while providing comprehensive coverage of various hazardous area classifications.
International Electrotechnical Commission (IEC)
The International Electrotechnical Commission (IEC) is a global organization that develops international standards for electrical equipment for use in hazardous areas.
IECEx certification issued by the IEC ensures that equipment complies with international safety requirements for HazLoc classifications, groupings and classifications.
A significant advantage of the IEC is its broad global reach and recognition, making its standards applicable to all HazLoc classifications worldwide.
Canadian Standards Association (CSA)
The Canadian Standards Association (CSA) is responsible for issuing hazardous location certifications in Canada, which are equivalent to those provided by the NEC and IECEx.
CSA standards play an important role in defining HazLoc classifications, groupings and grading across Canada.
A distinctive feature of the CSA is its special focus on Canadian regulations and requirements to ensure compliance with national safety standards.
European ATEX Directive
The European ATEX (Atmospheric Explosives) Directive sets out requirements for equipment and protective systems for use in hazardous areas within the European Union.
It provides detailed guidelines for HazLoc classification, grouping, and grading to ensure the safety of equipment in potentially explosive environments.
The distinguishing feature of the ATEX directive is its comprehensive coverage of electrical and non-electrical equipment, which can effectively deal with a variety of hazardous scenarios.
Equipment and Protective Systems Intended for Use in Potentially Explosive Atmospheres Regulations 2016 (UKEX Regulations)
Due to Brexit, the UKEX regulations, which originally complied with the European ATEX Directive, have been revised. Although ATEX and UKEX may remain similar in requirements, equipment certification now requires separate submissions to both regulatory bodies.
Occupational Safety and Health Administration (OSHA)
OSHA is the U.S. regulatory agency responsible for setting and enforcing workplace safety standards, including hazardous locations.
While OSHA has no specific focus on the classification, grouping, and grading of HazLoc, its regulations still cover general safety requirements that apply to these environments and are designed to protect workers and prevent accidents and safety incidents.
OSHA’s distinguishing feature is its broad coverage, which is not limited to hazardous locations but also includes safety regulations for various industries and various workplaces.
FAQ
What is the difference between Division 1 and Zone 1?
Both Division 1 and Zone 1 indicate that hazardous materials are present during normal operations.
However, Division 1 is used in the Class/Division system, while Zone 1 belongs to the Zone system.
The main difference is the different areas where these systems are applied.
Why is it important to understand hazardous location classifications?
Understanding these classifications helps us prevent accidents by ensuring the correct equipment is used and proper safety protocols are followed.
Conclusion
Understanding hazardous locations is essential to ensuring safety and compliance in any industry.
By applying the correct classification, we can protect workers and equipment from potential hazards.
If you have any questions or require further information, please feel free to contact us.
We are ready to help you navigate these complex safety standards.