A Selection Guide for Explosion Proof Motors
04/03/2025
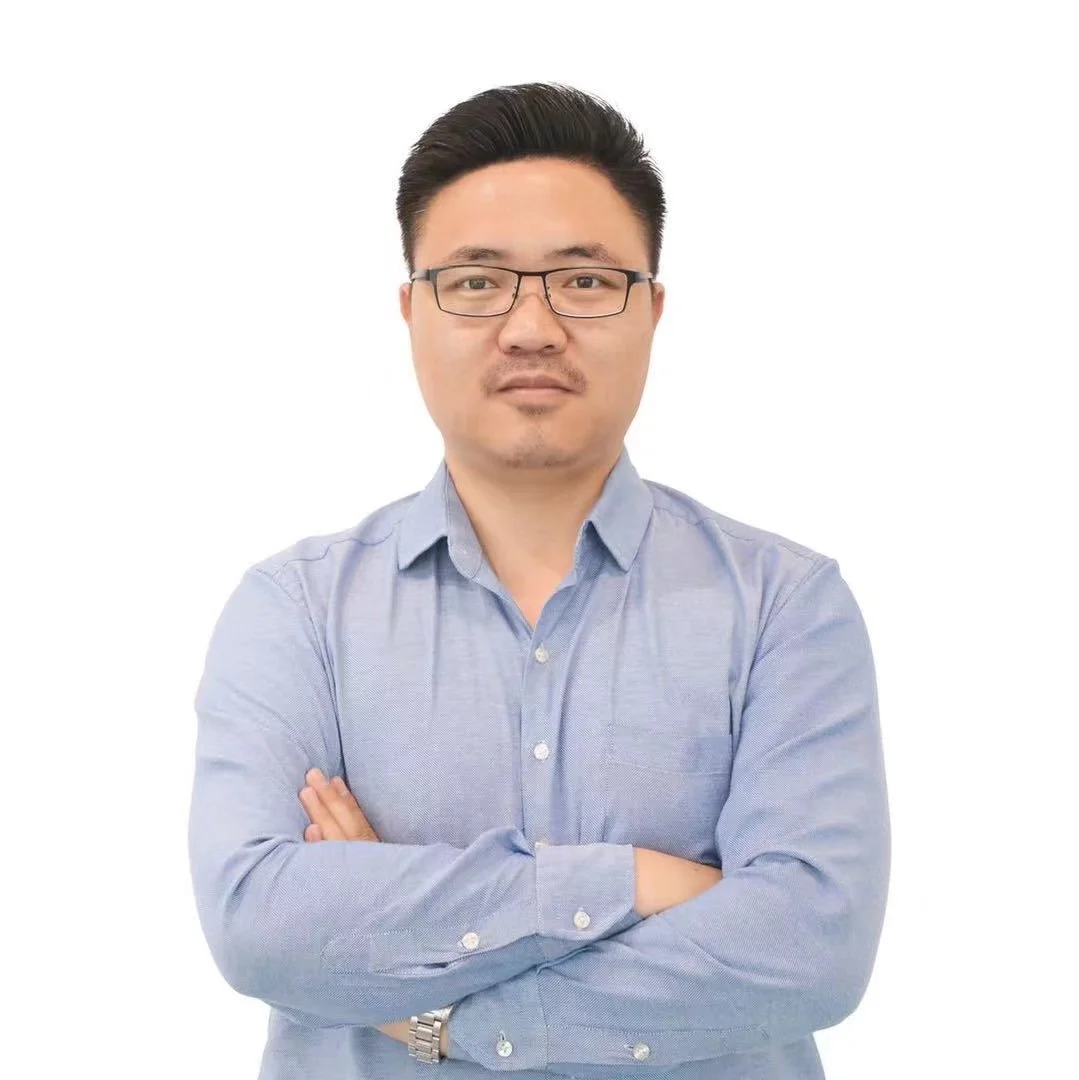
Sam Nie
Hello every one. This is Sam Nie, the CEO of LUPMOTORS. With 10 year's technical and manufacture experience in the field of 3-phase electric motor, I can provide you definitive guides in the knowledge of 3-phase industrial electric motors,which will help you a lot in selecting electric motors for your applications.
Introduction
The Problem: Choosing the Wrong Motor Can Be Dangerous
Imagine working in a refinery or a flour mill, where a single spark from an electric motor could ignite an explosion.
The consequences?
Fires, financial losses, or worse—lives at risk.
Many assume that explosion-proof means these motors prevent explosions altogether, but that’s not true.
Their real job?
To contain any internal ignition, preventing it from reaching the hazardous environment around them.
Selecting the right explosion-proof motor isn’t just a technical decision—it’s a life-or-death matter.
Whether you’re a procurement manager ensuring regulatory compliance or a maintenance engineer looking to minimize risks, making the wrong choice can lead to serious hazards, legal troubles, and costly downtime.
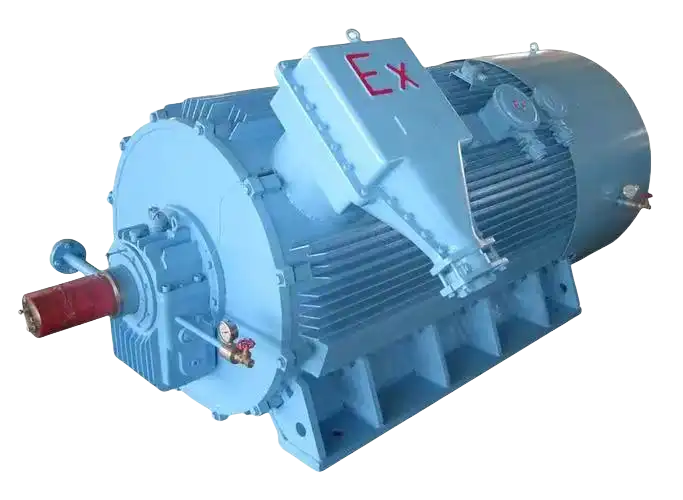
Table of Contents
Table of Contents
What Is an Explosion-Proof Motor?
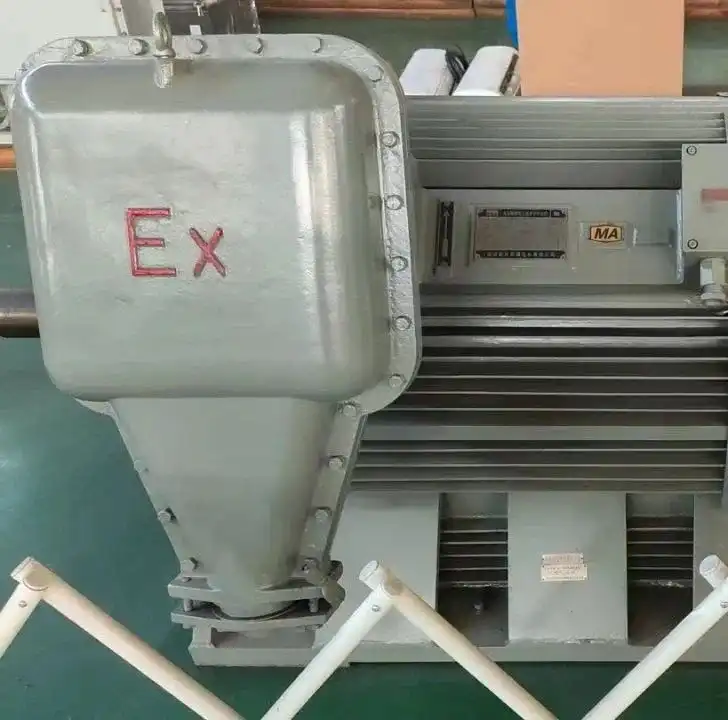
An explosion-proof motor is a specially designed electric motor that can operate safely in environments where flammable gases, vapors, dust, or fibers are present.
Unlike standard motors, these are built with sealed housings to contain any internal sparks, arcs, or heat that could trigger an external explosion.
Misconception Alert: Many think “explosion-proof” means the motor can withstand external blasts. That’s wrong. It actually means the motor prevents internal explosions from escaping.
Industries That Require Explosion-Proof Motors
Explosion-proof motors aren’t just for heavy industries—they’re mandatory in hazardous environments like:
- Oil & Gas – Refineries, offshore rigs, and fuel processing plants.
- Chemical Plants – Where volatile liquids and vapors are common.
- Food Processing – Flour mills and sugar plants prone to combustible dust.
- Mining Operations – Methane gas exposure risks.
Choosing the right explosion-proof motor is not just about compliance—it’s about protecting assets, workers, and operations.
Now that we know why explosion-proof motors matter, let’s break down how to classify them so you can select the right one.
Tip: To get more knowledge about the Explosion-Proof Motor, please read this article.
Tip: You can see our explosion-proof motor in our product page.
Tip: You can see some standard motors in our product page.
Video Resources
Tip: These 2 videos will illustrate the Working Principle of Explosion-Proof Motors.

Quiz: Test Your Knowledge of Part 1: What Is an Explosion-Proof Motor?
- A. The motor is indestructible and can survive external explosions.
- B. The motor prevents external explosions from occurring in hazardous environments.
- C. The motor is designed to contain internal sparks or explosions, preventing them from igniting external flammable substances.
- D. The motor cools itself down automatically when it detects hazardous gases.
- A. To prevent electrical components from igniting flammable gases, vapors, or dust.
- B. To comply with industry safety regulations.
- C. To improve the speed and performance of industrial equipment.
- D. To protect facilities and workers from fire and explosion risks.
- A. Oil & gas, chemical plants, and food processing.
- B. Retail stores, healthcare facilities, and schools.
- C. Textile factories, banking institutions, and software companies.
- D. Fitness centers, tourism agencies, and shopping malls.
Learn More about Electric Motors?
LUPMOTORS will send you articles to your Email every week.
100% Free! No Credit Card!
Understanding Explosion-Proof Motor Classifications
Choosing the right explosion-proof motor starts with understanding hazard classifications.
These classifications determine which motors can operate safely in hazardous environments.
One of the most recognized standards for explosion-proof motors is UL674, along with various classifications based on hazard types, divisions, and zones.
Let’s talk about it.
2.1 What is UL Certification—UL674?
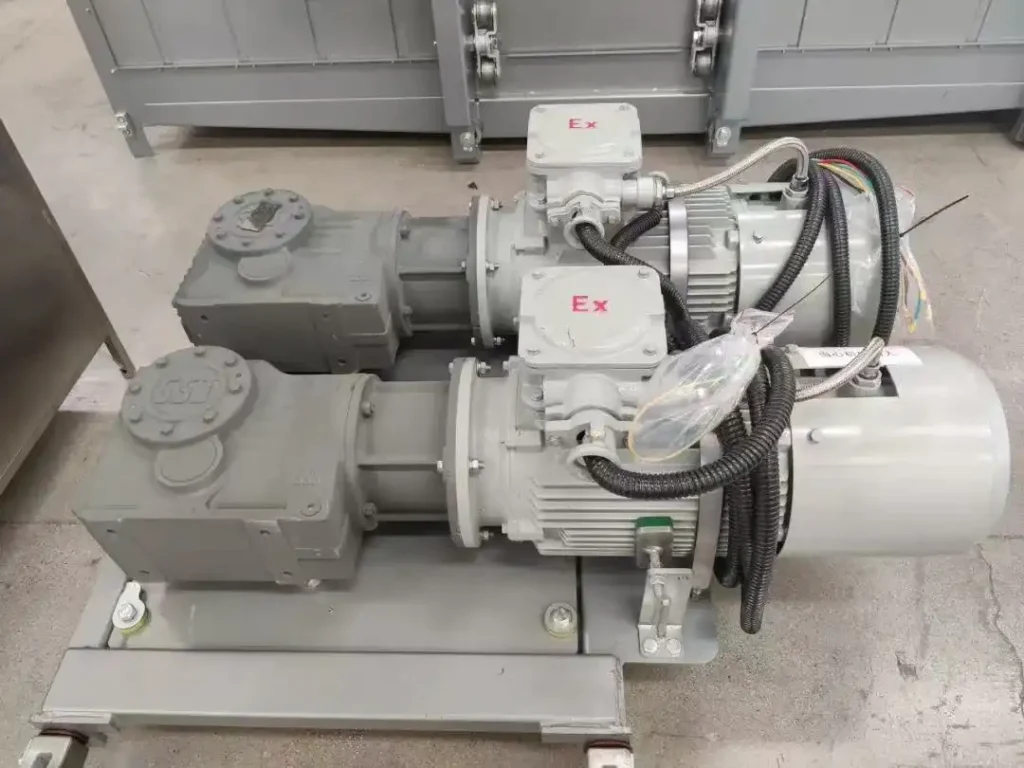
UL674 is a safety standard developed by Underwriters Laboratories (UL) for explosion-proof and dust-ignition-proof motors.
Motors that meet this certification must pass rigorous testing to ensure they can contain internal ignitions without igniting surrounding flammable substances.
Key Features of UL674 Certified Motors:
- Sealed and rugged enclosures to prevent the spread of internal sparks.
- Strict temperature control to prevent surface overheating.
- Ingress protection to keep out gases, dust, and fibers.
- Compliance with NEC (National Electrical Code) and NFPA 70 standards.
2.2 Understanding Hazardous Location Classifications
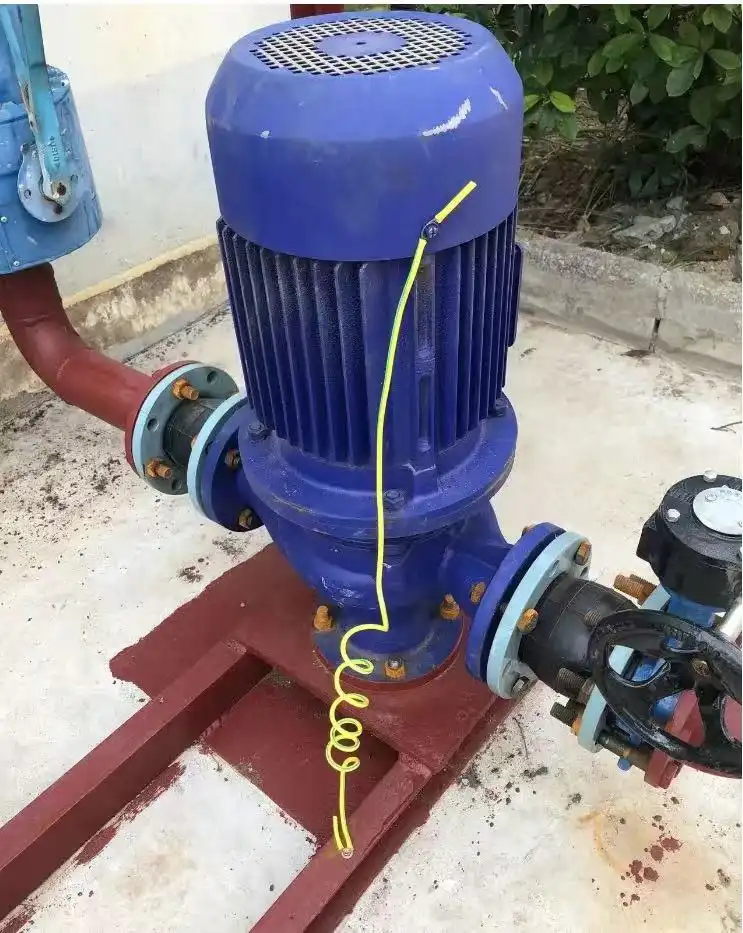
Explosion-proof motors are classified based on the type of hazards present in a facility.
These are divided into three major classes according to the National Electrical Code (NEC).
Table: Hazardous Location Classifications
Class | Hazard Type | Examples |
Class I | Flammable gases, vapors, and liquids | Oil refineries, gas plants, paint spraying booths |
Class II | Combustible dusts | Grain silos, flour mills, sugar refineries, coal plants |
Class III | Ignitable fibers & flyings | Textile mills, woodworking factories, paper mills |
How This Affects Motor Selection:
- If your facility handles gasoline vapors or hydrogen, you need a Class I explosion-proof motor.
- If your workplace generates coal dust or sugar dust, a Class II dust-ignition-proof motor is necessary.
- If fibers and flyings are present, a Class III motor prevents ignition risks.
🚀 Next Up: : Classifications go beyond just hazard type. In the next section, we’ll explore how hazardous locations are divided into Divisions and Zones, so you can choose the right motor for your environment.
2.3 Division vs. Zone System: How Hazardous Areas Are Classified
Once we define the hazard type (Class I, II, or III), the next step is to understand how hazardous the environment is.
This is done through two classification systems:
- The Division System (used in North America under the NEC standard)
- The Zone System (used in Europe under the ATEX standard)
Both systems categorize environments based on how frequently hazardous substances are present.
Division vs. Zone System (Comparison Table)
Classification | Division System (NEC – North America) | Zone System (ATEX – Europe & International) |
Continuous Hazard | Division 1: Flammable gases/dust are present regularly or continuously under normal operation. | Zone 0 (Gas) / Zone 20 (Dust): Explosive atmosphere is always present. |
Intermittent Hazard | Division 1: Hazardous material may exist under normal operation (not continuous but frequent). | Zone 1 (Gas) / Zone 21 (Dust): Explosive atmosphere exists occasionally. |
Abnormal Condition Hazard | Division 2: Flammable gases/dust are only present in abnormal conditions (leaks, spills, ventilation failure). | Zone 2 (Gas) / Zone 22 (Dust): Explosive atmosphere is unlikely and only exists for short periods. |
Example: How Class + Division Affect Motor Selection
Let’s compare two industrial sites to see how Class and Division classifications influence motor selection.
Example 1: Oil Refinery (Gas Hazard – Class I, Division 1 vs. Zone 0/1/2)
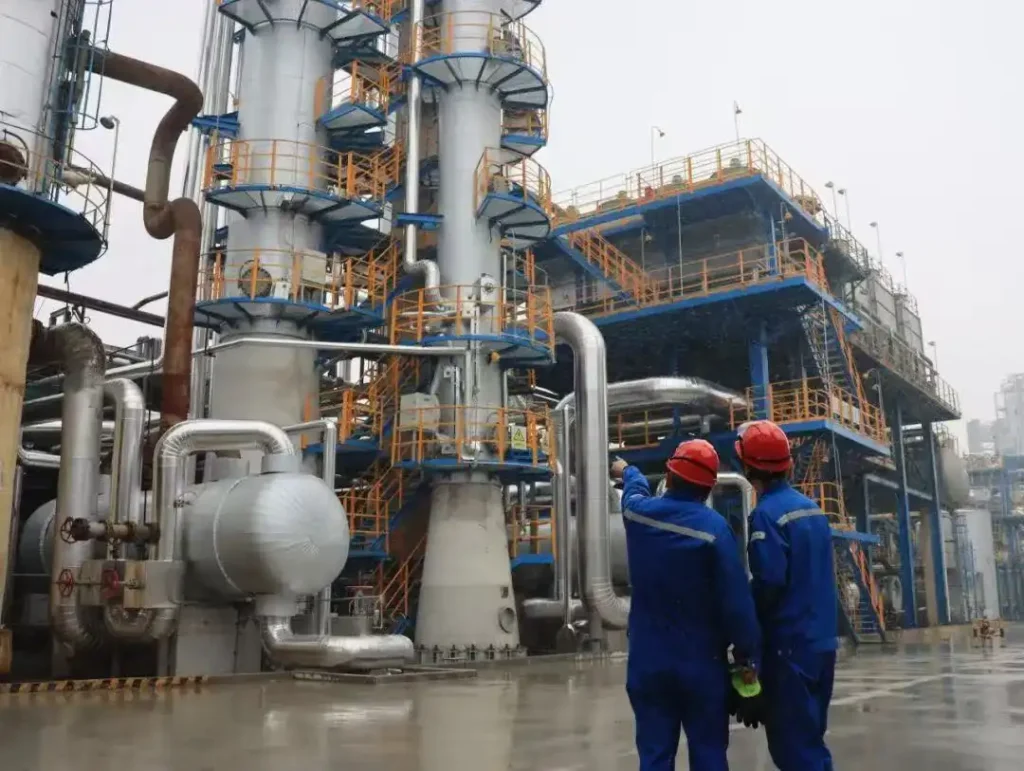
🚨 Scenario:
A petroleum refinery handles flammable gases like methane, propane, and benzene.
Some areas always have these gases in the air, while others only experience exposure in rare leaks or malfunctions.
✅ Best Motor Choice:
- Processing Unit (High-Risk Area) → Class I, Division 1 (or Zone 0/1) motor, built to withstand constant gas exposure.
- Storage Tanks (Low-Risk Area) → Class I, Division 2 (or Zone 2) motor, since gases are only present in abnormal leaks.
Example 2: Flour Mill (Dust Hazard – Class II, Division 1 vs. Zone 20/21/22)
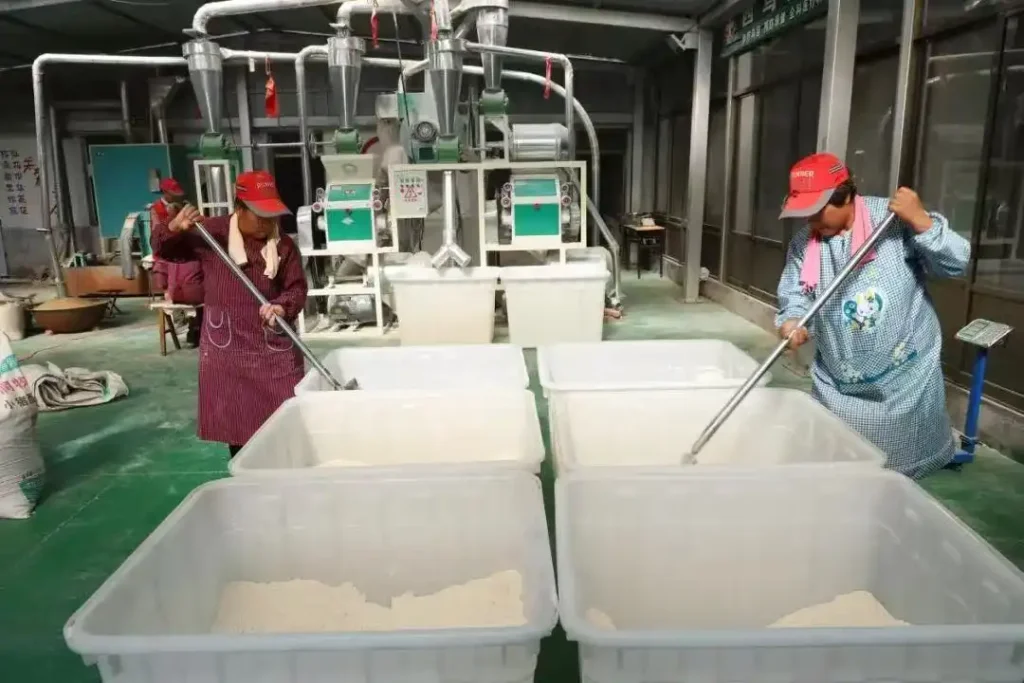
🚨 Scenario:
A flour milling plant produces fine combustible dust that lingers in the air, creating a high risk of ignition.
✅ Best Motor Choice:
- Milling Room (Constant Dust) → Class II, Division 1 (or Zone 20/21) motor because dust is always present.
- Packaging Area (Occasional Dust Exposure) → Class II, Division 2 (or Zone 22) motor since dust is present only during spills or maintenance.
🚀 Next Up: Now that we’ve classified hazards by Class, Division, and Zone, let’s look at Hazardous Groupings and how they affect motor selection.
2.4 Hazardous Groupings: How Different Substances Impact Motor Selection
Once we determine the hazard class (I, II, or III) and the Division or Zone, the next step is identifying the specific substances present.
Not all hazardous materials behave the same way—some ignite at lower temperatures, while others generate more intense explosions.
That’s why motors are further categorized into Hazardous Groups (A-G) based on the type of gas, vapor, or dust they must safely operate around.
That’s why motors are further categorized into Hazardous Groups (A-G) based on the type of gas, vapor, or dust they must safely operate around.
Hazardous Groupings (Gas & Dust Categories)
Group | Substance Type | Examples | Risk Level |
Group A | Acetylene | Welding areas, chemical plants | Highest risk – extremely explosive |
Group B | Hydrogen, butadiene | Hydrogen processing plants, refineries | High risk – very flammable gases |
Group C | Ethylene, cyclopropane | Chemical production, plastics factories | Moderate risk – common industrial chemicals |
Group D | Gasoline, acetone, propane | Gas stations, paint shops, breweries | Lower risk – widely used fuels & solvents |
Group E | Metal dusts (aluminum, magnesium) | Metal grinding, powder coating facilities | Extremely dangerous – highly combustible metals |
Group F | Carbonaceous dusts (charcoal, carbon black) | Coal processing, carbon plants | High risk – fine dust can cause explosions |
Group G | Grain, flour, plastics, chemical dusts | Food processing, pharmaceutical plants | Common risk – airborne dust ignites easily |
Why Do These Groupings Matter?
Different substances ignite at different temperatures and react differently to heat and sparks.
Selecting a motor that isn’t rated for the correct group can cause ignition, fires, and catastrophic failures.
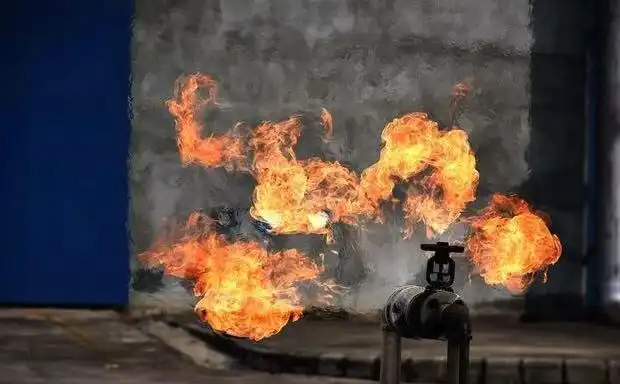
Photo: The Hydrogen explosion accident.
For example:
🔹 Hydrogen (Group B) ignites at just 560°F (293°C), meaning any exposed heat source can trigger an explosion.
🔹 Grain dust (Group G) burns slowly but builds up pressure, leading to massive secondary explosions.
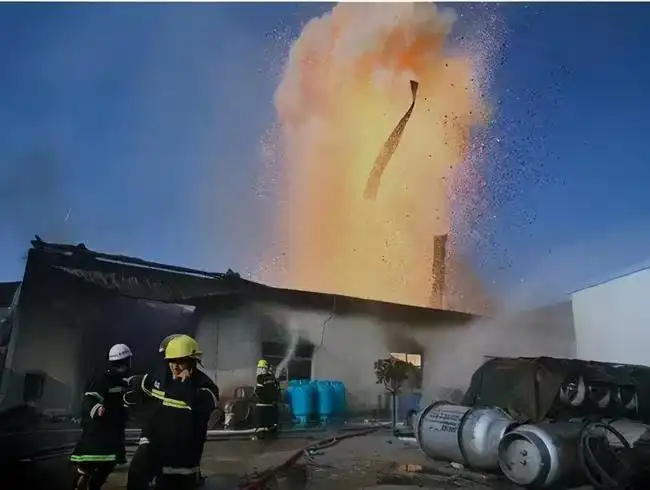
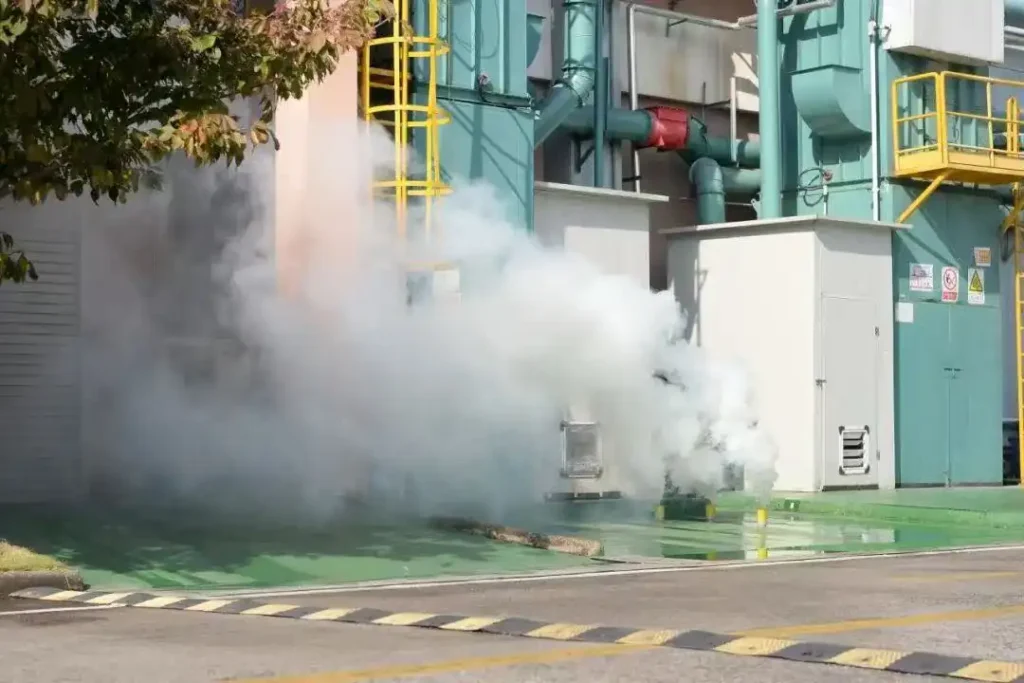
Photo: The dust explosion accidents.
Case Study: In 2017, a corn mill explosion in Wisconsin killed five workers and destroyed a large portion of the plant. Investigators traced the cause to electrical equipment not rated for Group G dust hazards. (Source: CSB)
🚀 Next Up: Now that we understand hazard classifications, let’s move on to Temperature Codes (T-Codes) and why they matter in explosion-proof motors.
Tip: To get more knowledge about the EXPLOSION PROOF ELECTRIC MOTORS: CLASS, GROUPS & DIVISIONS, please read this article.
Tip: You can see the Hazardous Area Classifications and
Protections in this page.

Quiz: Test Your Knowledge of Part Two " Understanding Explosion-Proof Motor Classifications"
1. What does UL674 certification indicate for an explosion-proof motor?
2. What is the key difference between Division 1 and Division 2 hazardous locations?
3. How does the Zone system (used in Europe and internationally) compare to the Division system (used in North America)?
4. Which hazardous material would require a Class II explosion-proof motor?
5. What is the primary purpose of Hazardous Group classifications (Groups A-G)?
How to Read Temperature Codes (T-Codes) in Explosion-Proof Motors
Choosing the right explosion-proof motor isn’t just about class, division, and group—it’s also about temperature safety.
A motor that runs too hot can ignite nearby gases, vapors, or dust particles.
That’s why Temperature Codes (T-Codes) exist—to tell us the maximum surface temperature a motor can reach without causing an explosion.
3.1 Why Do Surface Temperature Ratings Matter?
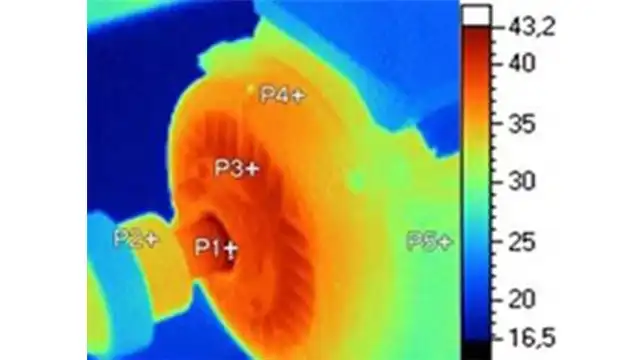
Every flammable gas or dust has an autoignition temperature (AIT)—the point at which it catches fire without a spark or flame.
If a motor’s surface temperature exceeds this limit, it can ignite the surrounding hazardous material.
Example: Hydrogen gas (Group B) has an autoignition temperature of 560°F (293°C). If a motor reaches 600°F, it could trigger an explosion just by being in the same environment.
That’s why motors are assigned T-Codes, ensuring their operating temperature stays below the ignition point of hazardous materials in the area.
3.2 T-Code Classification
T-Codes define the maximum surface temperature a motor can reach under normal operation.
Table: T-Codes
T-Code | Max Surface Temp (°C) | Max Surface Temp (°F) | Example of Flammable Substance |
T1 | 450°C | 842°F | Methanol, Hydrogen |
T2 | 300°C | 572°F | Gasoline, Ethanol |
T3 | 200°C | 392°F | Diesel Fuel, Kerosene |
T4 | 135°C | 275°F | Acetylene, Propane |
T5 | 100°C | 212°F | Ammonium Nitrate |
T6 | 85°C | 185°F | Carbon Disulfide |
Comparing T-Code Limits to Ignition Temperatures
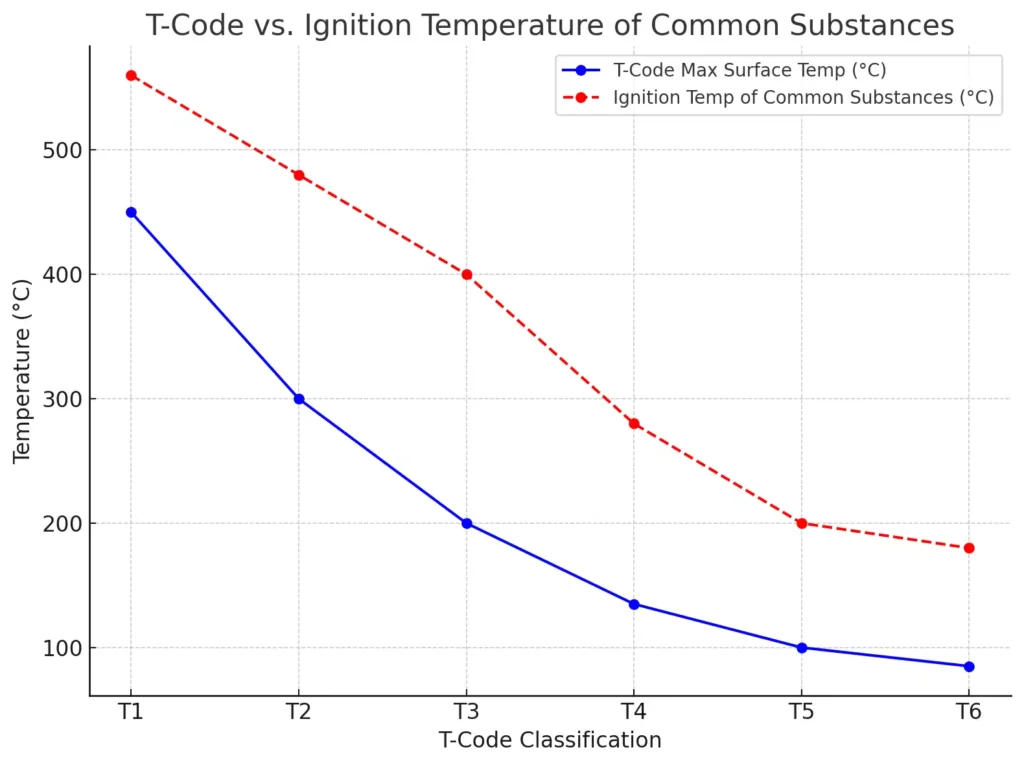
Visual Guide:
T-Code Selection Made Simple → If your hazardous substance ignites at 200°C, you need a T-Code of T3 or lower.
🚀 Next Up: Now that we’ve covered classifications and temperature safety, let’s talk about how to select the right explosion-proof motor based on your worksite conditions.
Key Factors to Consider When Selecting an Explosion-Proof Motor
Selecting the right explosion-proof motor is not just about compliance—it’s about safety, efficiency, and long-term reliability.
Choosing the wrong motor can lead to fires, equipment failure, or even catastrophic explosions.
Here’s how to make the right decision, step by step.
STEP 1: Identifying the Hazardous Environment
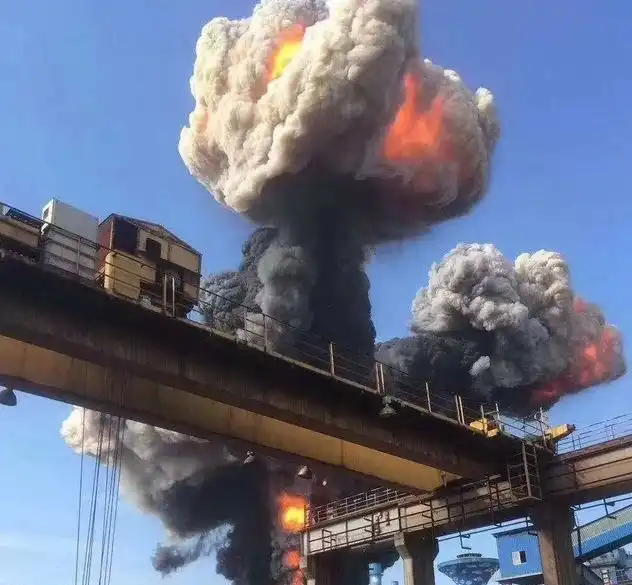
Before selecting a motor, you must assess the worksite and determine the potential risks.
Not all hazardous locations are the same.
Some environments contain constant exposure to flammable substances, while others only have occasional risks.
Checklist: Is Your Worksite Hazardous?
- Are there flammable gases, vapors, or dust present?
- How often are these substances present? (Always? Occasionally? Only in emergencies?)
- What is the autoignition temperature of these substances?
- Is ventilation present to reduce hazard concentration?
- Are motors and electrical equipment near potential ignition sources?
💡 Example: A chemical processing plant has constant exposure to hydrogen gas (Group B, Class I, Division 1). It requires a T1-rated, explosion-proof motor to prevent ignition.
STEP 2: Matching the Right Motor to the Classification
Once the hazardous environment is identified, the next step is choosing a motor that meets the necessary specifications.
Table: What to Check in an Explosion-Proof Motor?
Specification | What It Means | Why It Matters |
Enclosure Type | Sealed casing to contain internal sparks | Prevents ignition of surrounding flammable materials |
Power Ratings | Voltage, frequency, and horsepower requirements | Ensures compatibility with the industrial load |
Insulation Class | Resistance to heat and moisture | Protects motor windings from overheating |
Ingress Protection (IP Rating) | Sealing against dust and moisture | Prevents internal damage from hazardous particles |
Table: Certifications to Look For
Explosion-proof motors must be certified to comply with safety standards.
These certifications guarantee that a motor has been tested for hazardous locations.
Certification | Region | What It Ensures |
UL (Underwriters Laboratories) 674 | USA | Ensures motor meets NEC standards for hazardous locations |
CSA (Canadian Standards Association) | Canada | Certifies explosion-proof compliance for North America |
IECEx (International Electrotechnical Commission) | Global | International standard for electrical equipment in explosive atmospheres |
ATEX (Atmosphères Explosibles) | Europe | Required for hazardous locations in the EU |
FM Approved (Factory Mutual) | USA & Global | Third-party certification for explosion-proof electrical equipment |
Tip: If your facility follows North American standards, look for UL or CSA certifications. If you operate in Europe, ensure your motor is ATEX-rated.
Key Takeaways
✔ Assess your worksite before selecting a motor.
✔ Check enclosure type, power ratings, insulation class, and certifications.
✔ Match motor classification to the right hazard group, division, and temperature code.
✔ Use UL, CSA, IECEx, or ATEX-certified motors for compliance and safety.
Real-World Case Studies – How Businesses Choose the Right Explosion-Proof Motors
Selecting an explosion-proof motor isn’t just about following safety codes—it’s about preventing disasters and ensuring smooth operations.
Here are three real-world examples of companies that made the right choice—and avoided catastrophe.
Case Study 1: Oil & Gas – Preventing a Refinery Explosion
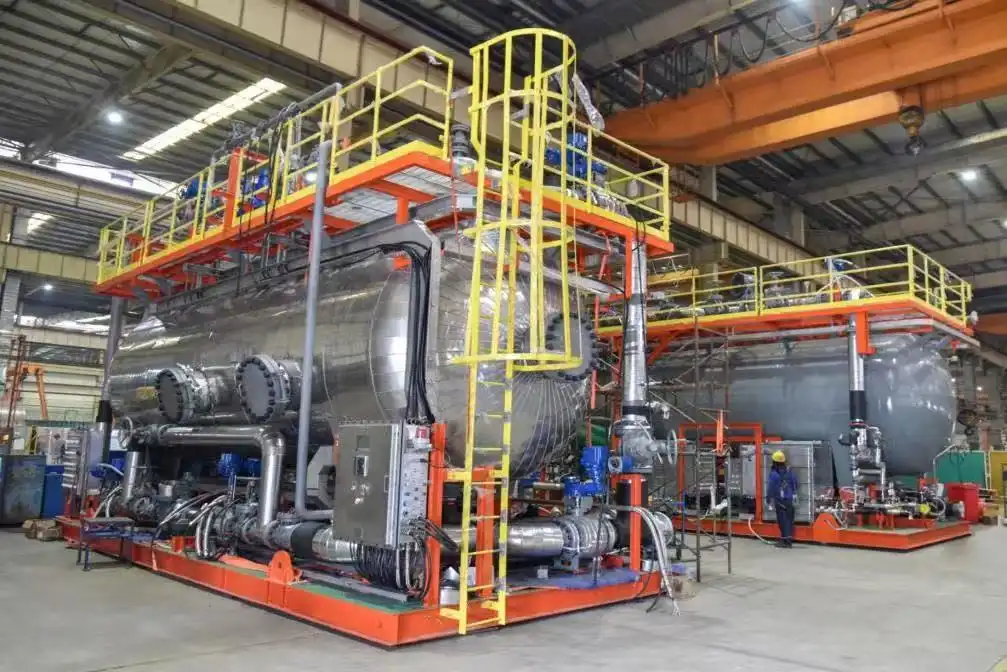
The Challenge:
A petroleum refinery processes highly flammable gases, including methane and propane.
One of its key motor-driven compressors was running with an older, non-rated motor, increasing the risk of ignition.
A single spark could have led to a catastrophic explosion.
The Solution:
The company switched to a Class I, Division 1, T3-rated explosion-proof motor, designed for continuous exposure to flammable gases. The new motor also featured:
✔ UL674 certification for explosion containment.
✔ Sealed, spark-proof enclosures.
✔ Vibration monitoring sensors for predictive maintenance.
The Results:
🔹 Zero ignition incidents since implementation.
🔹 20% increase in motor lifespan due to proper temperature regulation.
🔹 Compliance with OSHA and NFPA safety regulations, avoiding fines.
💡 Lesson: In the Oil & Gas sector, where gases are always present, using a Division 1 motor isn’t optional—it’s a lifesaving necessity.
Case Study 2: Chemical Manufacturing – Balancing Safety & Efficiency in an ATEX Zone 1 Facility
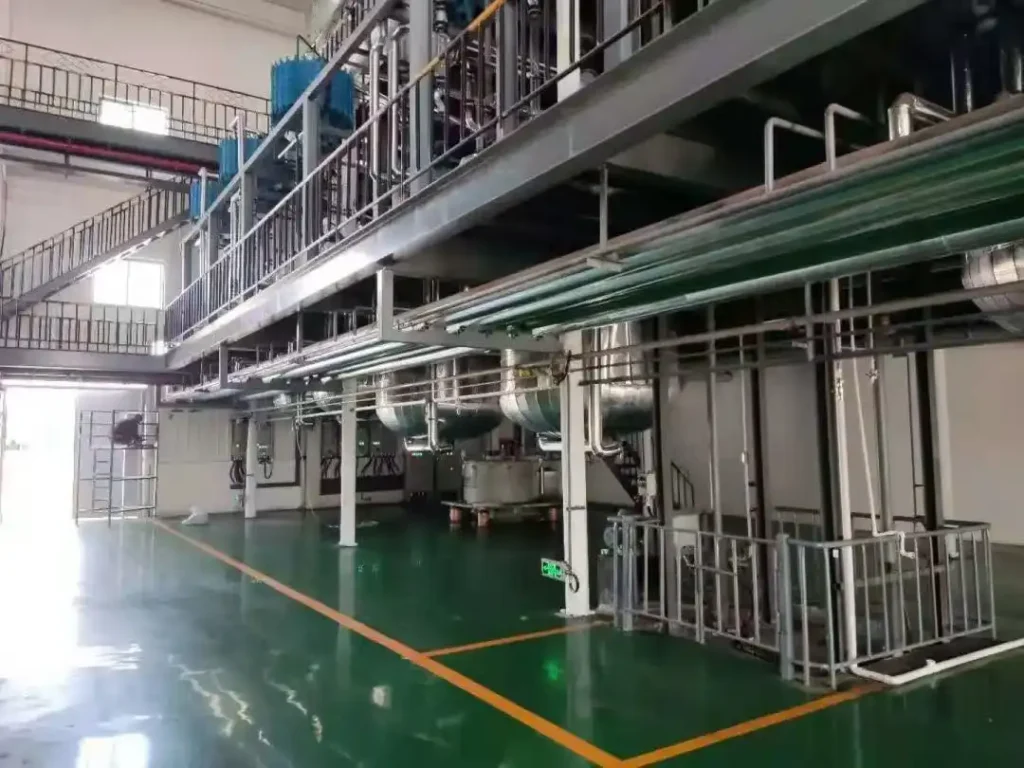
The Challenge:
A chemical plant handling ethylene and butadiene (both flammable gases) needed to upgrade its motors to meet EU ATEX safety regulations.
Their existing motors:
❌ Weren’t ATEX-rated, violating European compliance laws.
❌ Had poor energy efficiency, increasing electricity costs.
❌ Didn’t have monitoring systems, making preventive maintenance impossible.
The Solution:
The company switched to ATEX Zone 1, T3-rated explosion-proof motors, designed for occasional gas exposure.
They also installed:
✔ Variable Frequency Drives (VFDs) to optimize motor speed.
✔ Smart sensors to monitor motor health in real time.
✔ ATEX-certified enclosures to meet EU safety standards.
The Results:
🔹 30% reduction in energy consumption, saving thousands in annual costs.
🔹 Eliminated compliance risks, avoiding €500,000 in potential fines.
🔹 Extended motor lifespan by 5+ years due to real-time condition monitoring.
💡 Lesson: In Chemical Manufacturing, balancing safety and efficiency is possible. Upgrading to ATEX-certified, high-efficiency motors saves money while ensuring compliance.
FAQ
What’s the difference between explosion-proof and intrinsically safe motors?
Explosion-proof motors are designed to contain internal sparks, arcs, or flames, preventing them from igniting external hazardous gases or dust. These motors have heavy-duty enclosures that stop explosions from spreading.
Intrinsically safe motors, on the other hand, operate at energy levels too low to cause ignition. Instead of containing explosions, they prevent them from happening in the first place. These are commonly used in low-power applications like sensors and instrumentation.
👉 Key Difference: Explosion-proof = Containment | Intrinsically safe = Prevention
Can any electric motor be made explosion-proof?
No. Standard electric motors cannot simply be modified to be explosion-proof. A true explosion-proof motor is engineered from the ground up with:
✔ Sealed, reinforced enclosures to prevent explosion escape.
✔ Temperature control systems to keep surfaces below ignition limits.
✔ Certified wiring and terminals to prevent sparks.
If a facility requires explosion-proof motors, always buy factory-certified motors with UL, ATEX, or IECEx ratings—never attempt DIY modifications.
How do I verify if a motor meets ATEX or NEC standards?
🔍 Look for Certification Labels
All certified explosion-proof motors have a nameplate listing their compliance standards. Here’s what to check:
✔ For North America (NEC/NFPA 70):
- UL674 (Underwriters Laboratories)
- CSA (Canadian Standards Association)
- FM Approved (Factory Mutual)
✔ For Europe (ATEX):
- Markings like Ex II 2G Ex d IIC T4 Gb
- Zone classification (0, 1, 2, 20, 21, 22)
✔ For International Markets (IECEx):
- IEC 60079 standard compliance
👉 Pro Tip: If a motor does not have an official certification on its nameplate, it is NOT explosion-proof.
What’s the lifespan of an explosion-proof motor?
The average lifespan of an explosion-proof motor is 10-20 years, depending on:
✔ Operating conditions – Harsh environments shorten lifespan.
✔ Maintenance schedule – Regular servicing extends motor life.
✔ Load handling – Motors running at full load 24/7 wear out faster.
👉 Pro Tip: Motors in oil refineries and chemical plants experience more wear due to corrosive gases and extreme temperatures. Routine inspections help maximize lifespan.
Are explosion-proof motors more expensive than standard motors?
Yes, explosion-proof motors cost more due to their:
✔ Heavy-duty enclosures to contain explosions.
✔ Advanced heat and spark suppression features.
✔ Compliance with strict safety certifications (UL, ATEX, IECEx).
💰 Cost Comparison:
- A standard 5 HP motor: $500 – $800
- A 5 HP explosion-proof motor: $1,200 – $2,500
However, buying the wrong motor for a hazardous location can cost far more in:
❌ Fines for non-compliance (up to $500,000 in some cases).
❌ Equipment damage from explosions or fires.
❌ Downtime due to motor failure.
👉 Bottom Line: Paying more upfront for an explosion-proof motor saves money long-term by avoiding accidents and downtime.
Resources
U.S. Chemical Safety Board (CSB) – Reports on Industrial Explosions
🔗 https://www.csb.gov/Underwriters Laboratories (UL) – UL674 Certification for Explosion-Proof Motors
🔗 https://www.ul.com/services/ul-674National Fire Protection Association (NFPA) – NFPA 70 (NEC) Hazardous Location Classifications
🔗 https://www.nfpa.org/codes-and-standards/all-codes-and-standards/list-of-codes-and-standards/detail?code=70ATEX Directive (EU) – Explosion Protection Standards for Europe
🔗 https://ec.europa.eu/growth/sectors/mechanical-engineering/atex_enIECEx – International Explosion Protection Standards
🔗 https://www.iecex.com/U.S. Department of Energy (DOE) – Energy Efficiency & Industrial Motor Consumption Data
🔗 https://www.energy.gov/eere/amo/articles/advanced-electric-motorsOSHA – Explosion Prevention in Hazardous Locations
🔗 https://www.osha.gov/explosive-and-hazardous-atmospheresIEEE – Research on Electric Motor Failures & Maintenance Best Practices
🔗 https://www.ieee.org/
We offer customized motor solutions to meet your specific application requirements
LUPMOTORS offers ac low voltage 3-phase asynchronous industrial motors of all types – Please contact us freely.
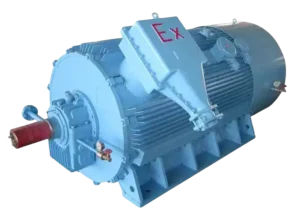
A Selection Guide for Explosion Proof Motors
Learn how to choose the right explosion-proof motor for hazardous locations. Understand classifications, T-Codes, and certifications to ensure safety and compliance!
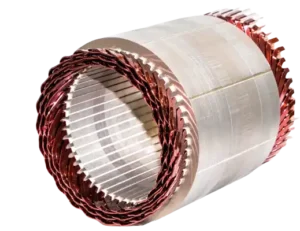
Structure of Electric Motors | The Complete Guide
Discover the structure of electric motors, from stators and rotors to windings and bearings. Learn how materials impact efficiency, performance, and lifespan!
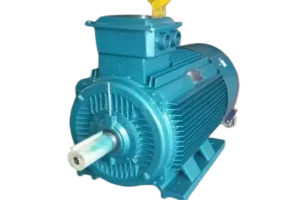
Motor Thermal Overload Protection | The Complete Guide
“Discover how motor thermal overload protection works, why it matters, and how to choose the right protector. Plus, take our quiz to test your knowledge!”
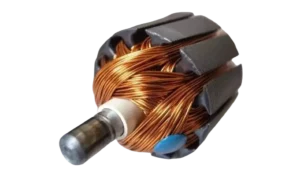
Brushed Motors vs. Brushless Motors: The Complete Guide
“Explore brushed vs. brushless motors: key differences, pros, cons, and which one fits your needs best!”
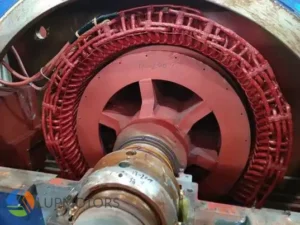
How to Test an Electric Motor: Tools, Methods & Procedures
Learn how to test electric motors with expert tools and methods. Discover step-by-step guides for insulation, resistance, and running current tests to ensure peak performance!
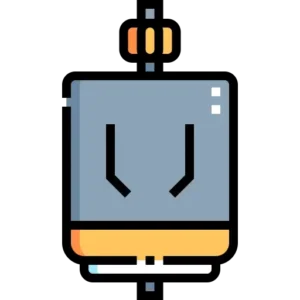
NEMA Motors vs IEC Motors: The Definitive Guide
“Explore the ultimate guide to NEMA vs. IEC motors. Learn key differences, efficiency standards, applications, and choose the right motor for industrial success.”