How to Read an Electric Motor Nameplate: Complete Guide for Beginner
06/11/2024
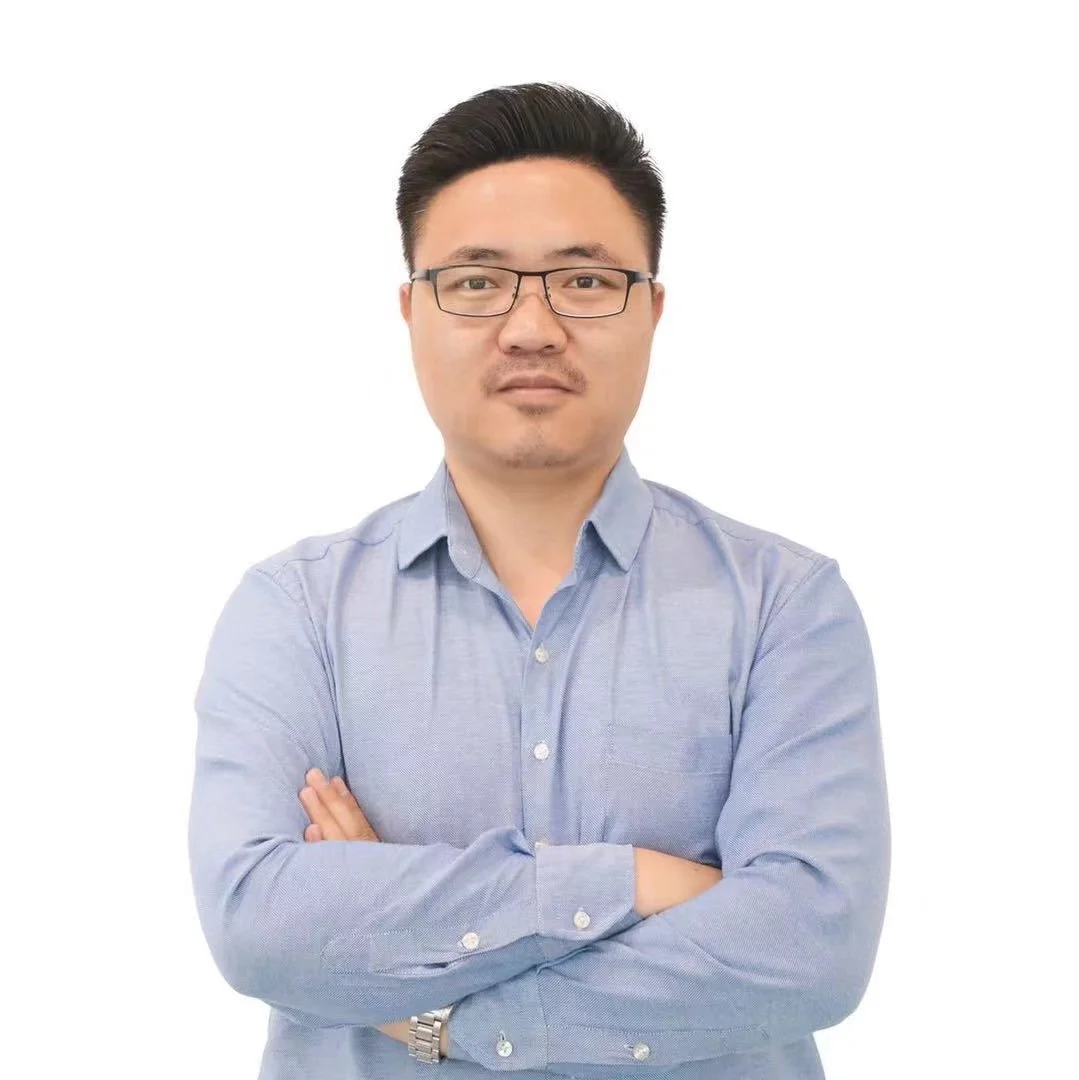
Sam Nie
Hello every one. This is Sam Nie, the CEO of LUPMOTORS. With 10 year's technical and manufacture experience in the field of 3-phase electric motor, I can provide you definitive guides in the knowledge of 3-phase industrial electric motors,which will help you a lot in selecting electric motors for your applications.
Reading an electric motor nameplate may seem simple, but it’s difficult to get clear about each parameter on it.
Without a clear understanding, it’s easy to fall into some problems—from selecting the wrong motor for your project to meeting unexpected breakdowns.
In this guide, I’ll show you how to read a motor nameplate step-by-step.
By the end, you’ll have the skills to select the right motor and avoid mistakes on your work.

Table of Contents
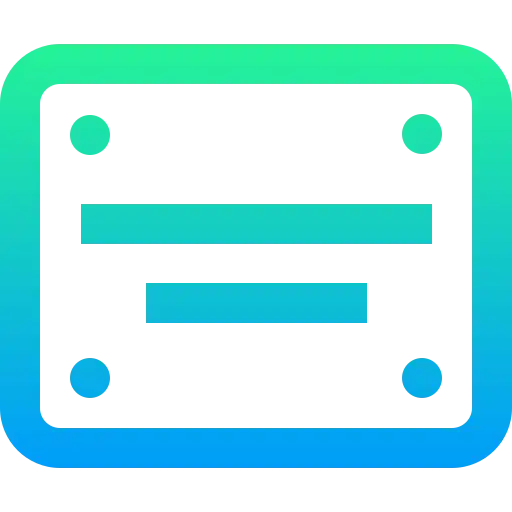
1. Key Terms Found on Electric Motor Nameplates
The first important thing to do is understanding a few key terms on an electric motor nameplate. This determine whether you can select and maintain the right motor or not. Let’s start!
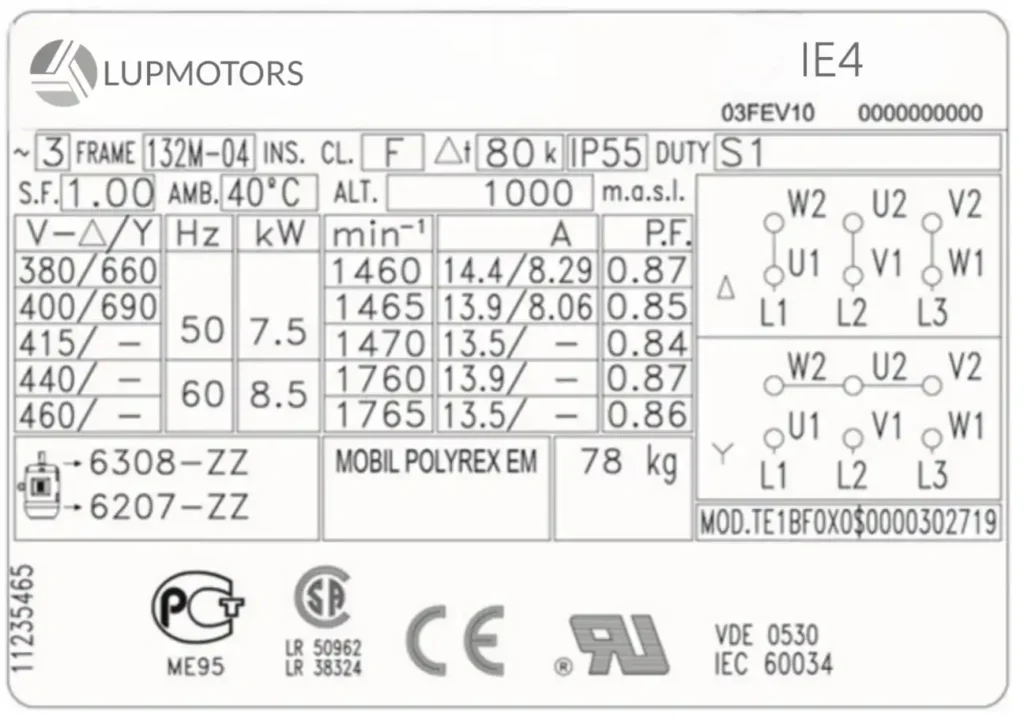
For this time we use the nameplate of LUPMOTORS for your reference. Please see the nameplate as below.
Tip: While the actual format will depend on different motor manufacturer and what standard it is followed to (IEC or NEMA). But don’t worry about that. You can be clear about other nameplate if you understand this one.
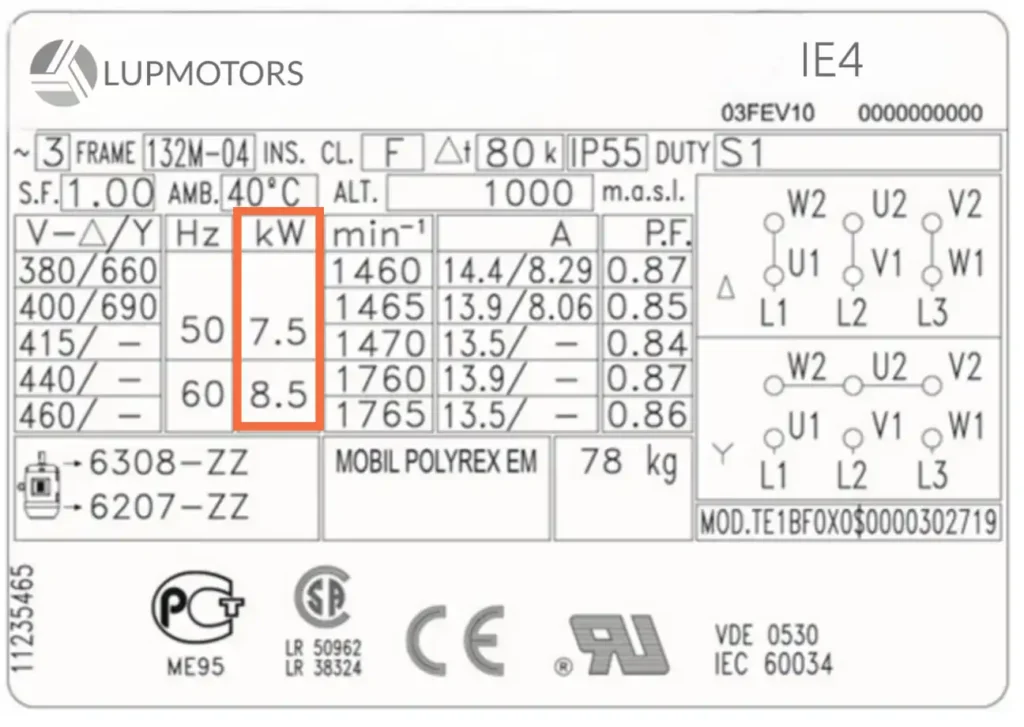
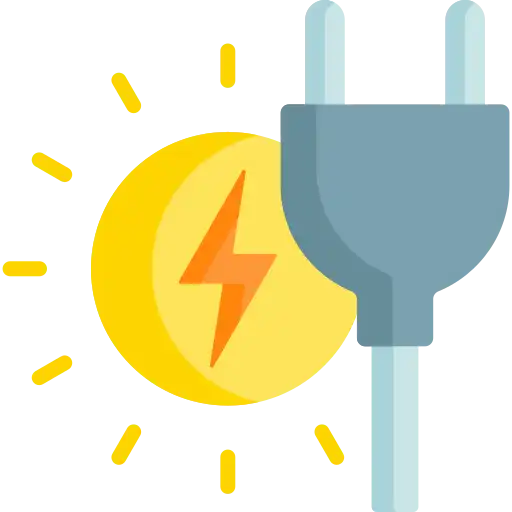
Rated Power
The rated power, often showed in kilowatts (KW) or horsepower (HP), tells us the motor’s power output capacity.
It’s a important indicator of the electric motor’s strength and what types of tasks it can do.
Generally, higher KW means the motor can handle more required applications, like heavy machinery in industrial settings.
For Example(Click each panel to get more information)
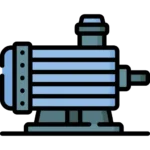
A 15 KW Motor
Click it for more contents
a 15 KW motor might be used in large conveyor systems
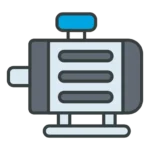
a 1.5 KW Motor
Click it for more contents
Whereas a 1.5 KW motor might be suitable for small machinery
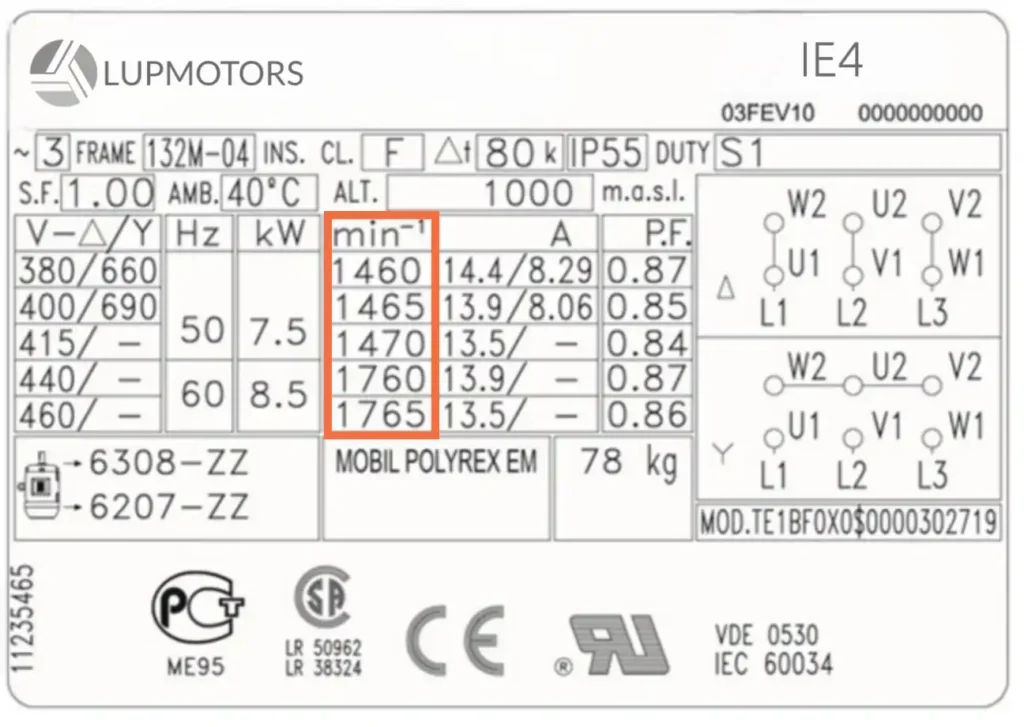
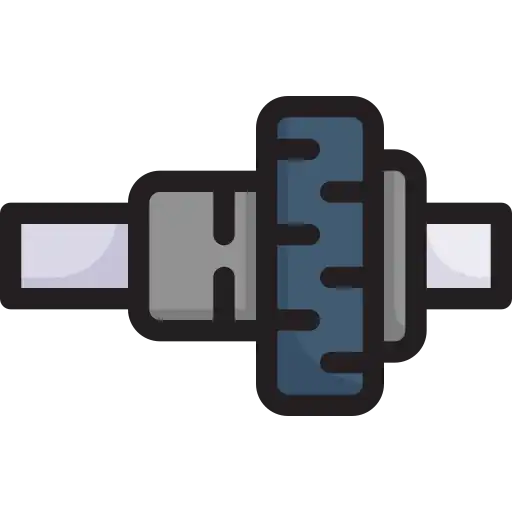
RPM

RPM, or Revolutions Per Minute, measures how fast the motor’s shaft rotates under specific conditions.
For an electric motor, Full Load Speed refers to the RPM when the motor is running at its full rated load.
This speed is typically slightly lower than the motor’s no-load speed because the load creates resistance that slows the motor down.
For Example
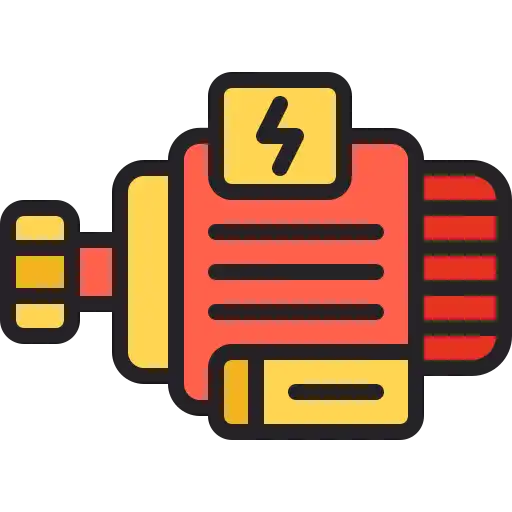
if a motor’s no-load speed is 1,800 RPM, its full load speed might be around 1,750 RPM.
This small reduction accounts for the extra effort the motor needs to drive the load. Full load speed is a critical parameter because it determines how well the motor matches the equipment’s operational needs. Using a motor with the correct RPM ensures that machines operate smoothly, efficiently, and with minimal wear, prolonging both motor and machine life.
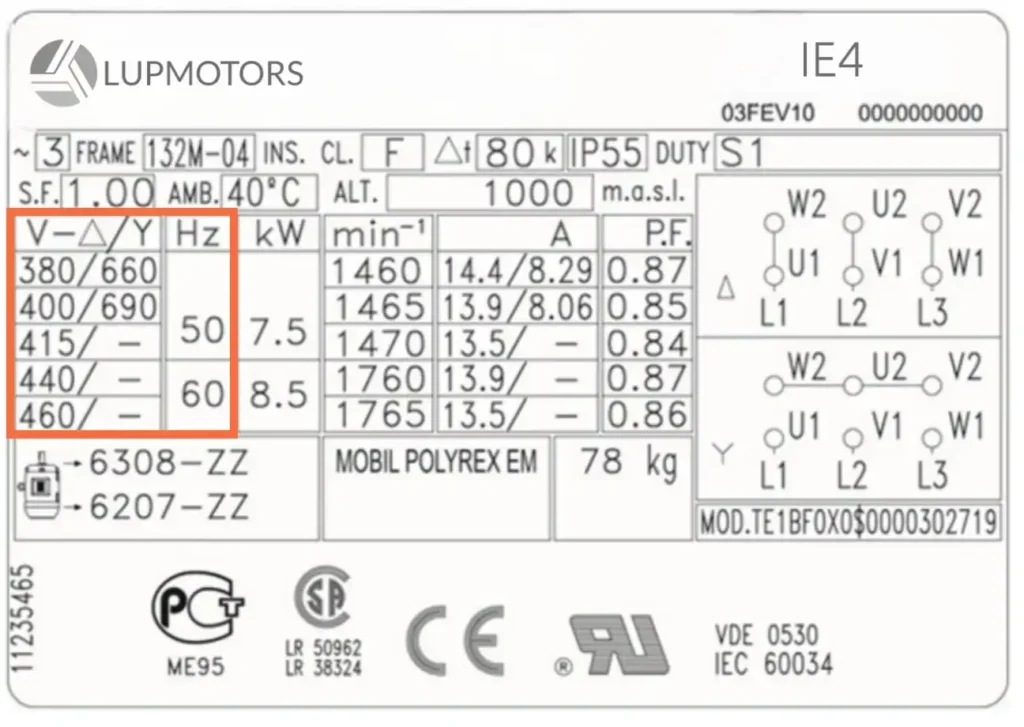
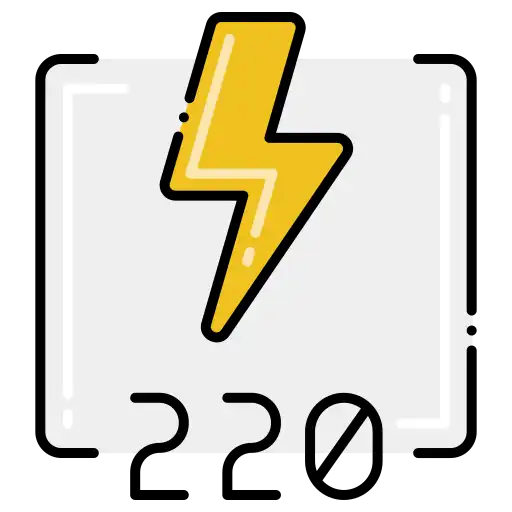
Voltage and Frequency
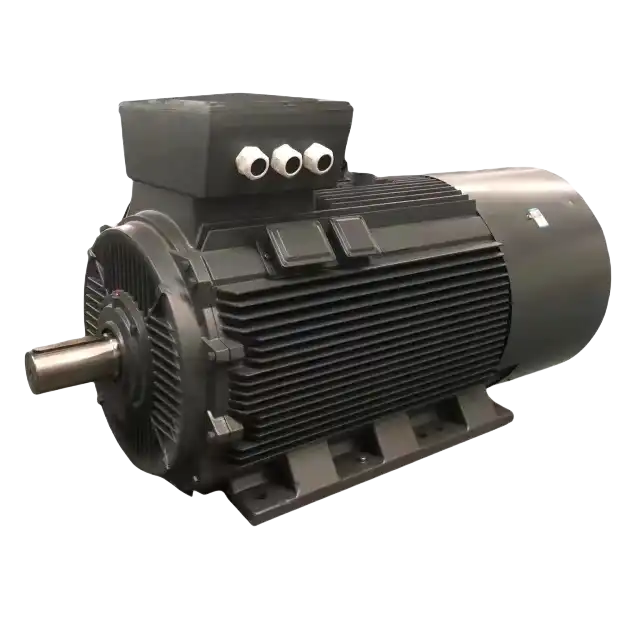
Voltage and frequency are essential specs on a motor nameplate.
They indicate the motor’s required operational voltage (e.g., 230V or 460V) and frequency, typically 50 Hz or 60 Hz, depending on the county or region.
It’s critical to select the correct voltage and frequency.
If a motor runs at the wrong settings, it can overheat or get the permanent damage.
For Example If you use a motor rated for 230V on a 460V power supply, it will almost lead to failure. Matching these values with your power source ensures the smooth operation and a longer lifespan for the motor.
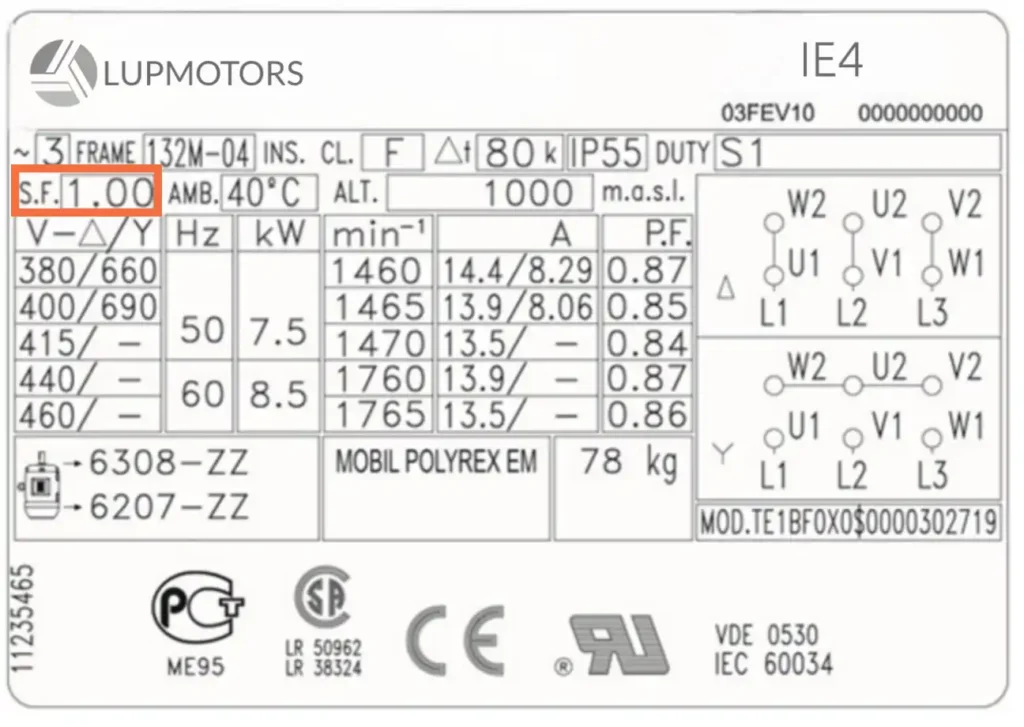
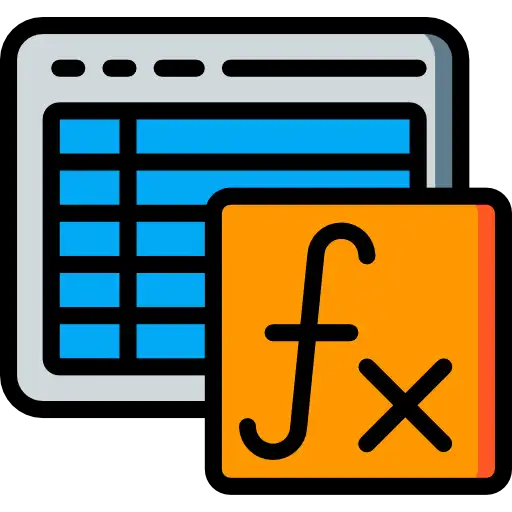
Service Factor (SF)

The Service Factor (SF) tells us how much extra load the motor can handle intermittently without damage.
It’s a measure of the motor’s resilience, particularly useful in applications where load demands can vary.
For example, a motor with a service factor of 1.15 can handle up to 15% more than its rated load under certain conditions.
A higher service factor offers flexibility and can prevent overheating during peak loads, which is invaluable in high-demand settings.
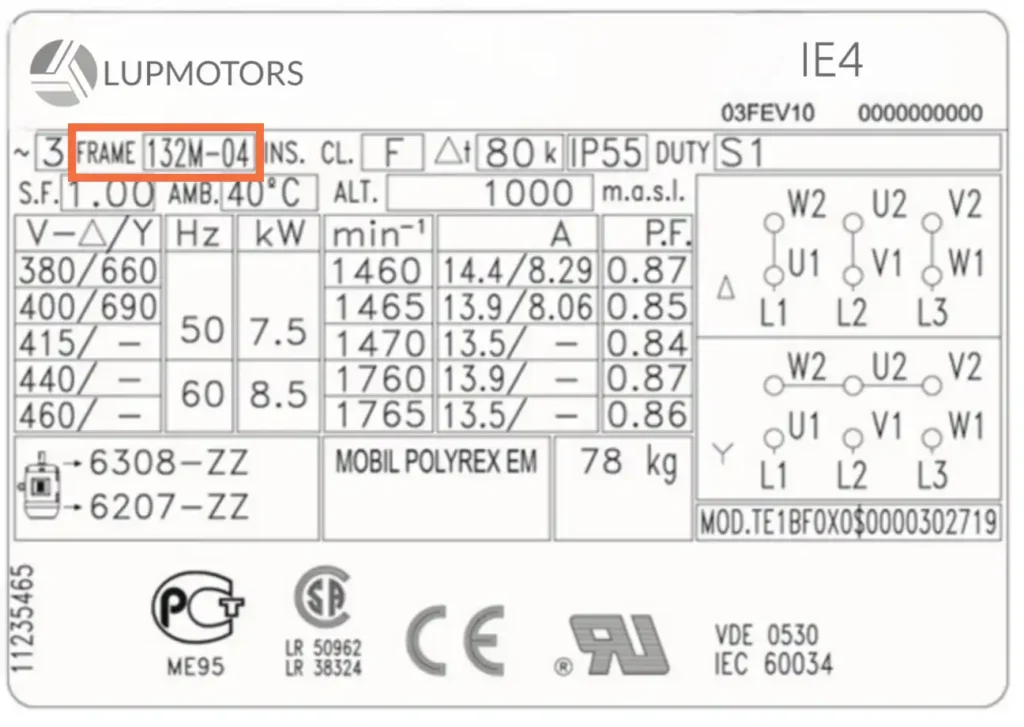
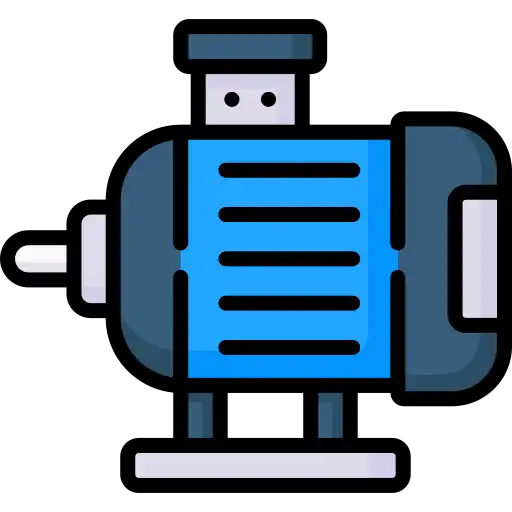
Frame Size
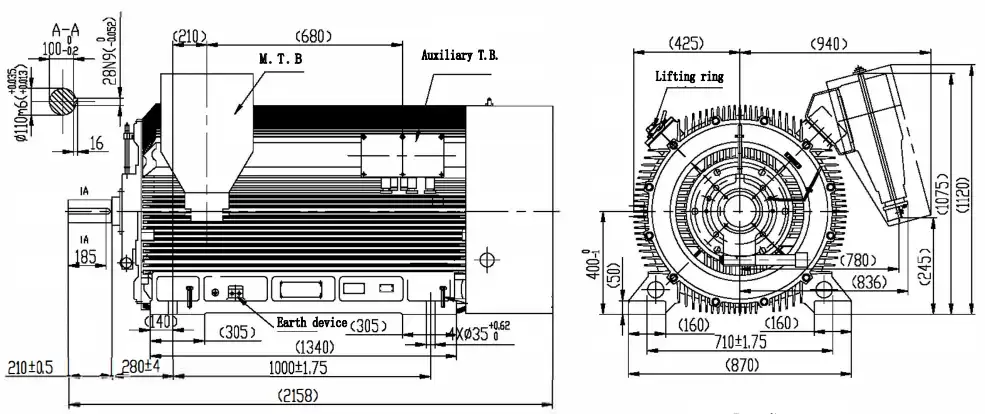
The frame size on a motor nameplate shows the motor’s physical dimensions and mounting configuration.
This includes details like the length, width, and bolt pattern, ensuring that the motor fits securely in its designated space.
Frame size is particularly important when replacing motors, as the wrong size can lead to improper mounting.
While the frame size will depend on the motor standards, which means the frame will be totally different under different standards such as IEC or NEMA.
By selecting the correct frame size, you can install the motor properly at the start.
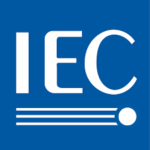
IEC Standard
Click it for more contents
The International Electrotechnical Commission (IEC) sets frame size standards for motors, primarily used outside of North America, including Europe and Asia.
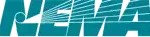
NEMA Standard
Click it for more contents
In North America, motor frame sizes are standardized by the National Electrical Manufacturers Association (NEMA).
Understanding Frame Size Numbers on Electric Motors
The frame size number on a motor nameplate provides essential information about the motor’s physical dimensions and mounting configuration. Here’s what the numbers typically represent:
1.Shaft Height: The first part of the frame size number generally corresponds to the shaft height (or center height) from the base of the motor to the center of the shaft.
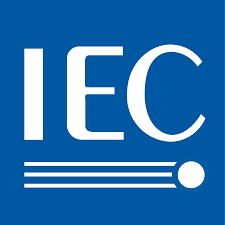
For IEC motors
This is measured in millimeters, so a frame size of "160M" indicates a shaft height of 160 mm.
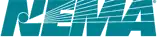
For NEMA motors
shaft height is indirectly indicated by the first two digits, divided by four.
For example, in a “143T” NEMA frame, dividing 14 by 4 gives a shaft height of 3.5 inches.
2.Mounting & Bolt Patterns: The numbers and letters in the frame size also provide information about mounting hole positions and bolt pattern configurations, ensuring the motor fits securely onto equipment. IEC and NEMA standards vary in this regard, so matching the correct frame size to your system is critical to avoid misalignment.
Overview of NEMA vs. IEC Standards
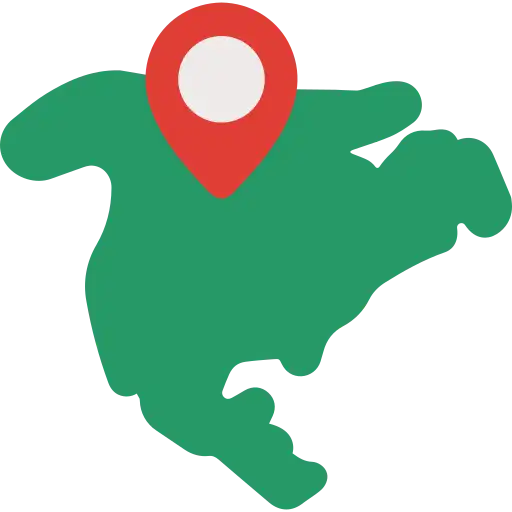
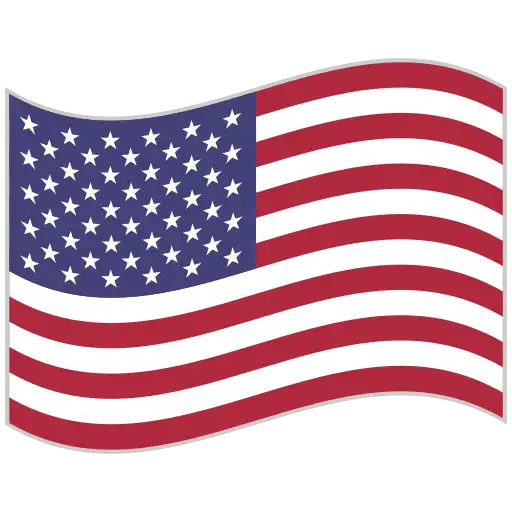
NEMA standards, mainly used in North America, define motor specifications such as efficiency, safety, and durability. Motors following NEMA standards are built to withstand more rugged conditions, making them a popular choice in industries where durability is key, like mining or heavy manufacturing.
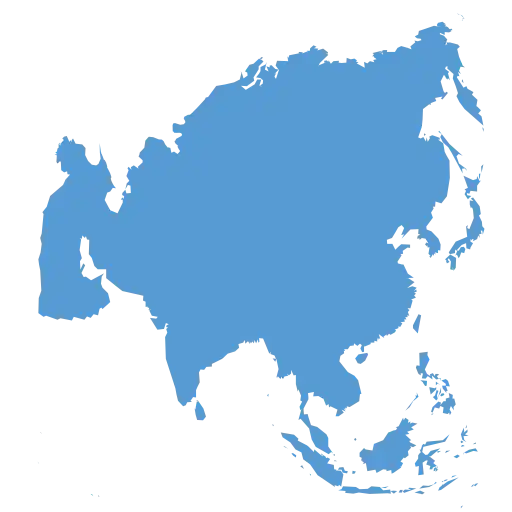
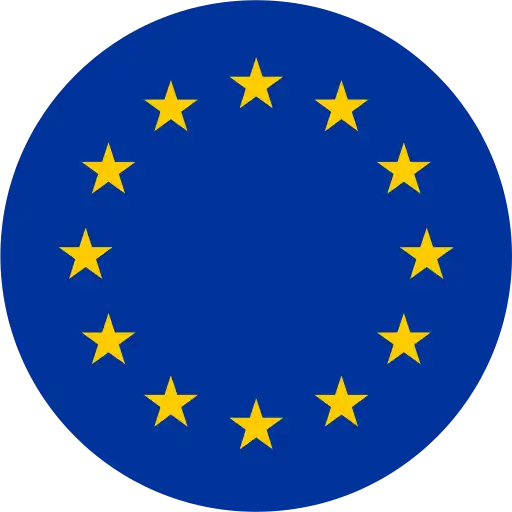
IEC standards, on the other hand, are internationally accepted and emphasize global interoperability. They focus on efficiency and sustainability, making them ideal for a broader range of applications worldwide, particularly in Europe and Asia.
Understanding the difference between NEMA and IEC standards is critical because it impacts motor selection, installation, and maintenance costs. Choosing a motor with the wrong standard could lead to issues in compatibility, efficiency, or durability, depending on the operating environment. For example, using a NEMA motor in a region that heavily regulates efficiency according to IEC standards might result in non-compliance with local energy codes.
Ultimately, the choice between NEMA and IEC should align with the operating conditions, regulatory requirements, and specific needs of the application. Properly matching standards ensures smoother operation, compliance, and optimized energy use, which directly affects operational costs and equipment longevity.
Comparison : NEMA vs. IEC Metrics
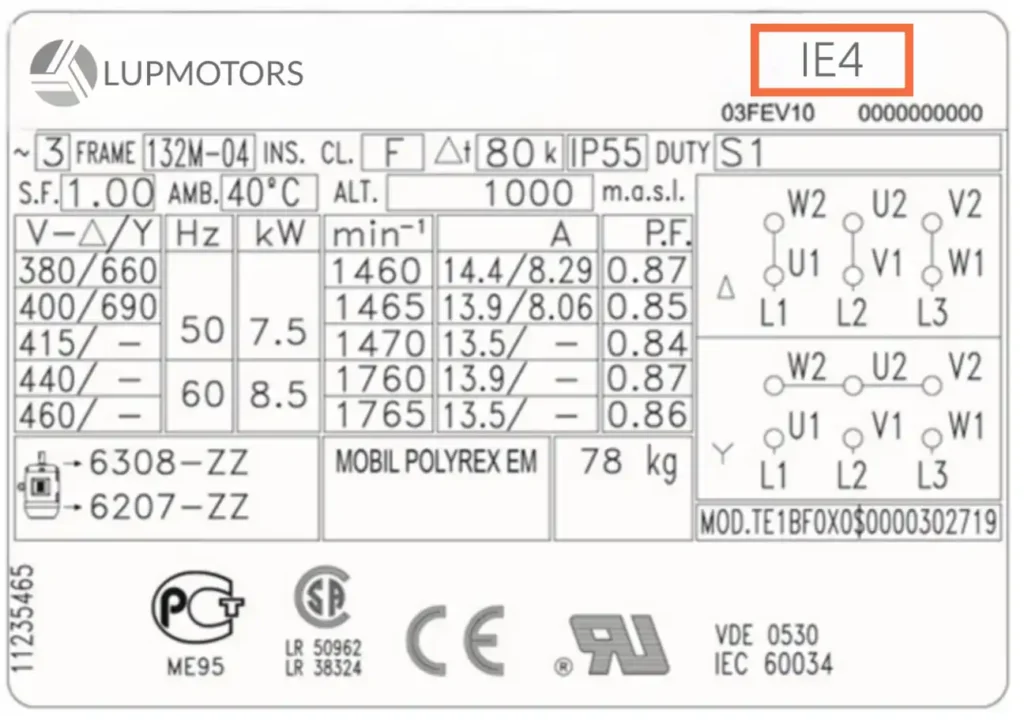
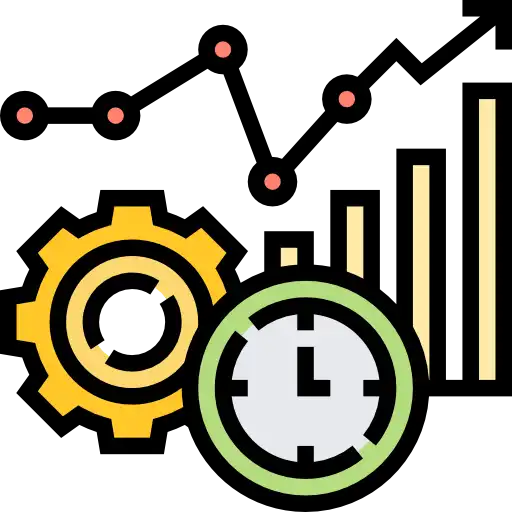
Efficiency Rating
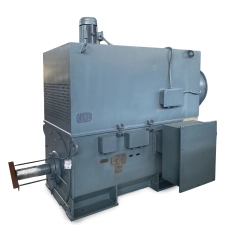
The efficiency rating indicates how effectively the motor converts electrical energy into mechanical power.
Higher efficiency means less energy waste, which reduces operating costs and is better for the environment.
In some industries with high energy demands, these savings can save much money for you.
While, there are also 2 kinds of standards(IEC & NEMA), which will indicate different efficiency rate.
Both NEMA and IEC standards aim to improve motor efficiency, though the specific testing methods may differ slightly.
By understanding these efficiency classes, users can select motors that meet local regulatory standards and align with their energy-saving goals.
IEC Efficiency Classes | NEMA Efficiency Standards |
---|---|
IE1 | NEMA Standard Efficiency |
IE2 | NEMA Energy Efficient |
IE3 | NEMA Premium Efficiency |
IE4 | Super Premium |
IE5 | / |
For Example, an IE3 motor, recognized as a high-efficiency motor according to IEC standards, could save up to 20% on energy costs compared to a standard motor.
In some industries with high energy demands, these savings can save much money for you.
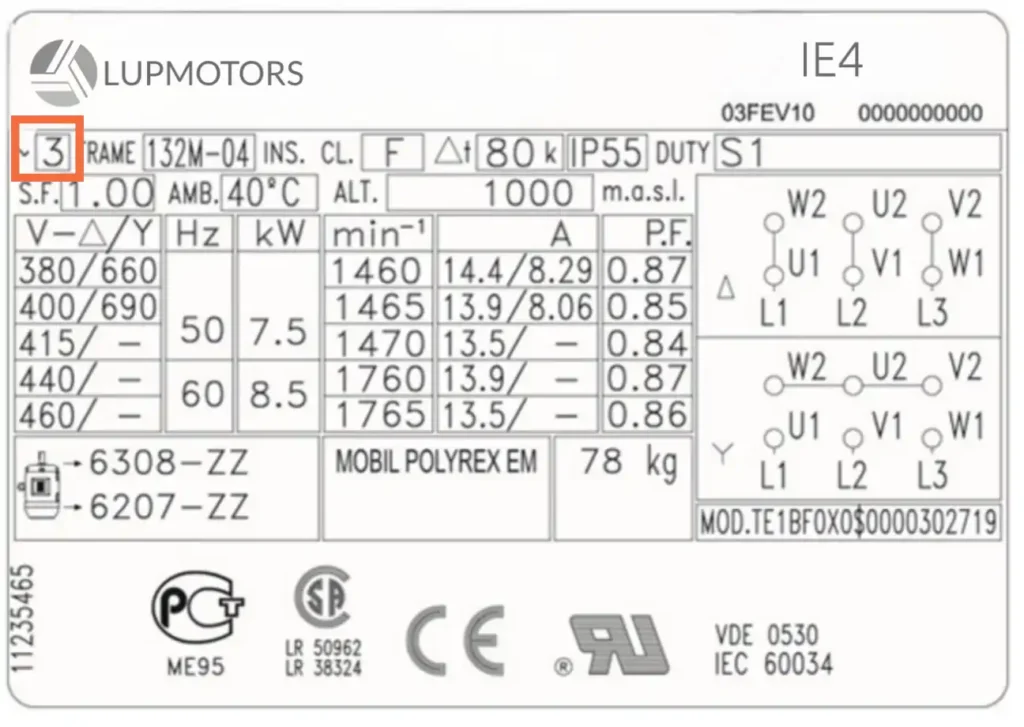
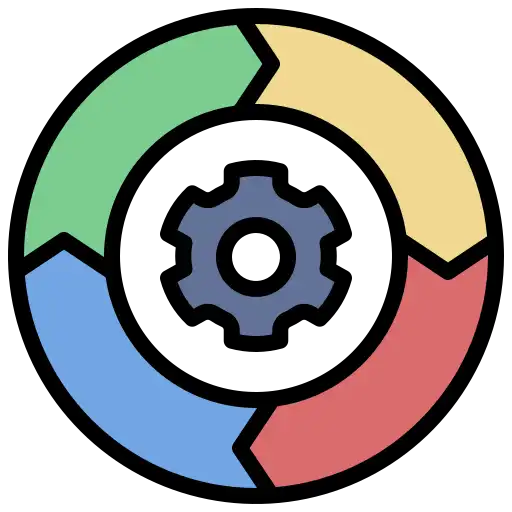
Phase (Single vs. Three-Phase)
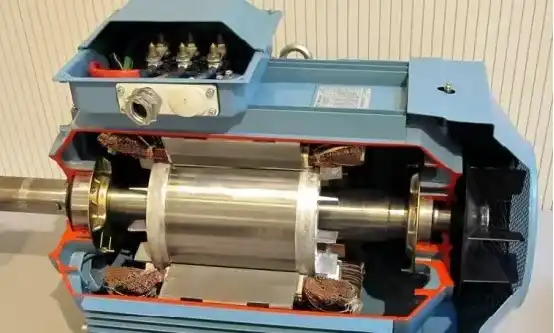
The motor phase information on a motor nameplate tells us whether the motor is suitable for a single-phase or three-phase electrical supply.
Single-phase motors are used in residential or small commercial applications, such as household appliances and small tools.
In contrast, three-phase motors are commonly used in industrial projects due to their efficiency and ability to do some higher power loads.
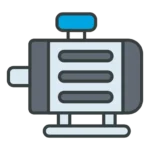
Single-phase motors
Click it for more contents
Single-phase motors are used in residential or small commercial applications, such as household appliances and small tools.
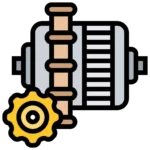
Three-phase motors
Click it for more contents
three-phase motors are commonly used in industrial projects due to their efficiency and ability to do some higher power loads.
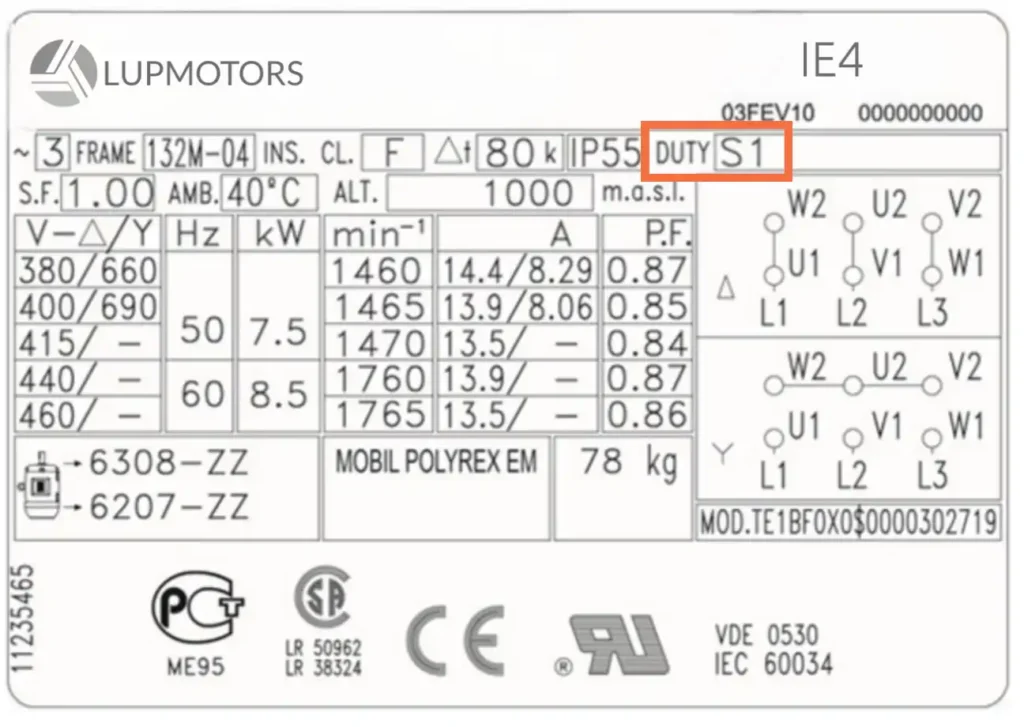

Service Duty
Service duty describes the motor’s intended operating cycle—whether it’s designed for continuous, intermittent, or short-duty use.
This rating ensures that the motor is used within its intended limits, which prolongs its lifespan and improves reliability.
Here’s a detailed table listing the different Service Duty types, or “Duty Cycles,” Each duty type (often labeled as “S” followed by a number) defines the motor’s intended operating cycle, from continuous to short bursts, and includes information about load and resting periods.
Please click each panel to get more info about the service duty.
S1 (Continuous Duty)
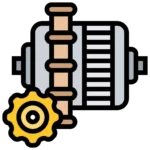
S1 (Continuous Duty)
Click it for more contents
Description
Operates at a constant load for an unlimited period without rest.
Typical Applications:
Fans, pumps, and conveyor systems requiring continuous operation.
S2 (Short-Time Duty)
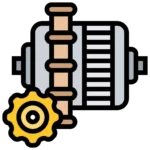
S2 (Short-Time Duty)
Click it for more contents
Description
Runs at a constant load for a limited time, then must rest to cool down.
Typical Applications:
Cranes, hoists, or other machinery that needs short bursts of work.
S3 (Intermittent Periodic Duty)
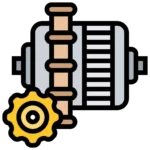
S3 (Intermittent Periodic Duty)
Click it for more contents
Description
Alternates between load operation and rest periods with sufficient cooling time in each cycle.
Typical Applications:
Machines with on/off cycles like presses or certain tools.
S4 (Intermittent Periodic Duty with Starting)
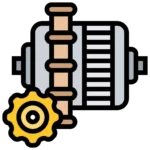
S4 (Intermittent Periodic Duty with Starting)
Click it for more contents
Description
imilar to S3 but includes a starting phase within each cycle.
Typical Applications:
Frequent-start applications like elevators and hydraulic pumps.
S5 (Intermittent Periodic Duty with Electrical Braking)
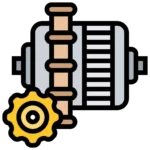
S5 (Intermittent Periodic Duty with Electrical Braking)
Click it for more contents
Description
Like S4, but includes braking periods between each load cycle.
Typical Applications:
Heavy-duty machinery that requires fast stops, such as winches.
S6 (Continuous Operation with Periodic Load Variations)
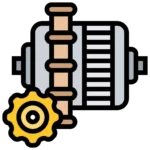
S6 (Continuous Operation with Periodic Load Variations)
Click it for more contents
Description
Operates with continuous cycling between loaded and no-load phases.
Typical Applications:
Variable-load machines like compressors and certain pumps.
S7 (Continuous Operation with Periodic Load, Starting, and Braking)
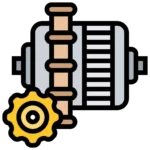
S7 (Continuous Operation with Periodic Load, Starting, and Braking)
Click it for more contents
Description
Similar to S6 but includes starting and braking within each cycle.
Typical Applications:
Heavy machinery that starts, stops, and brakes continuously.
S8 (Continuous Operation with Variable Load, Speed, and Braking)
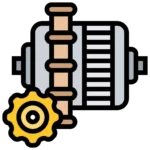
S8 (Continuous Operation with Variable Load, Speed, and Braking)
Click it for more contents
Description
Operates with continuous variation in load, speed, and braking cycles.
Typical Applications:
Complex machinery like rolling mills and textile machines.
S9 (Duty with Non-Periodic Load and Speed Variations)
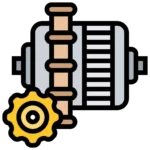
S9 (Duty with Non-Periodic Load and Speed Variations)
Click it for more contents
Description
Operates with continuous variation in load, speed, and braking cycles.
Typical Applications:
Custom applications with highly irregular duty cycles.
S10 (Duty with Discrete Constant Load Changes)
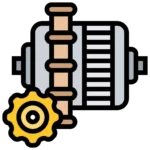
S10 (Duty with Discrete Constant Load Changes)
Click it for more contents
Description
Operates with several distinct, constant load levels within each duty cycle.
Typical Applications:
Specialized applications with multiple load levels, like testing rigs.
For Example
For example, a motor rated for continuous duty (S1) is built to run non-stop without overheating, which makse it ideal for applications like conveyor belts. On the other hand, a motor with intermittent duty (S3) is suited for tasks that involve regular stops and starts, such as in certain packaging machines. You can choose the correct service duty to avoid overheating and mechanical stress.
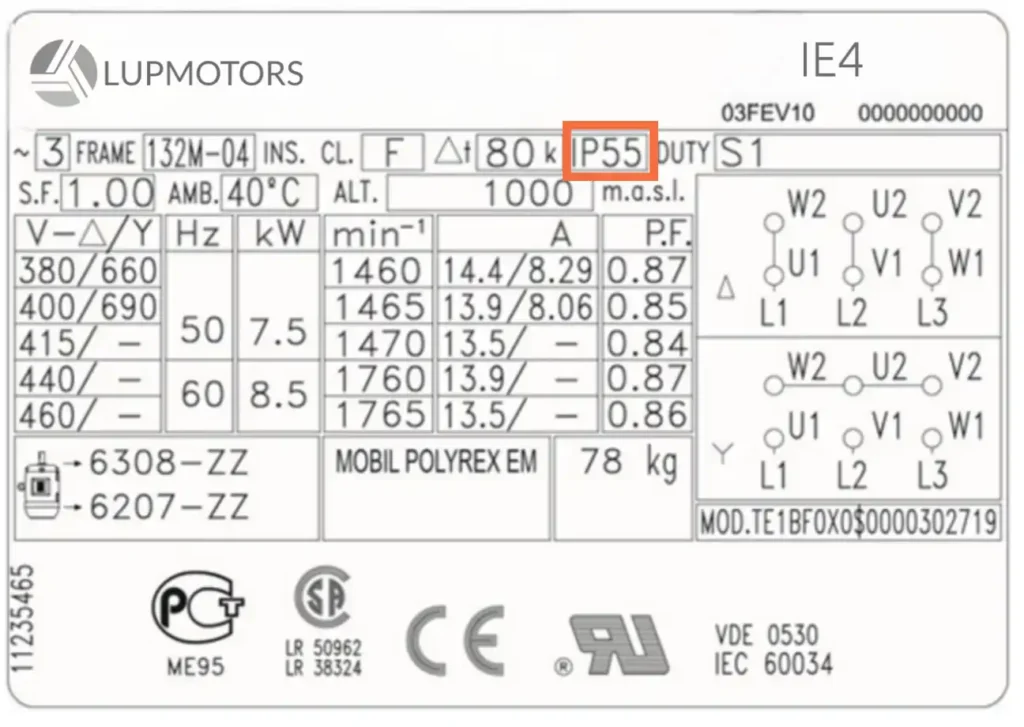
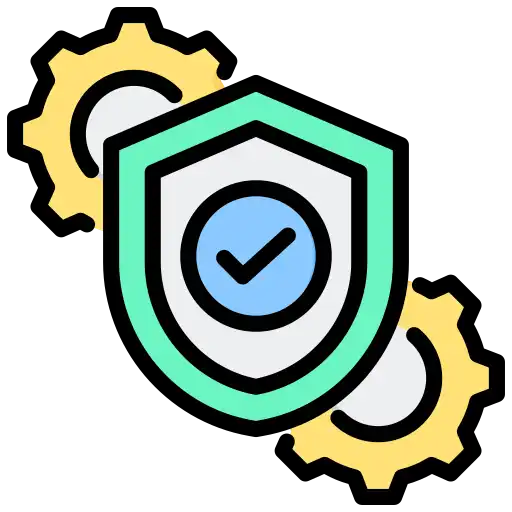
Degree of Protection (IP Rating)
The IP (Ingress Protection) rating on a motor nameplate specifies the level of protection the motor’s enclosure provides against dust and water.
This rating is especially important in outdoor or harsh environments where the motor may be exposed to contaminants.
The IP rating system is composed of two digits: the first digit indicates protection against solid objects, and the second digit indicates protection against liquids.
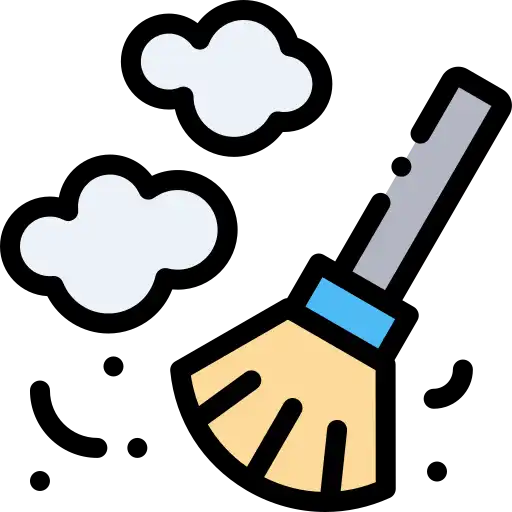
The first Number"X" (IP X1)
indicates protection against solid particles (like dust)
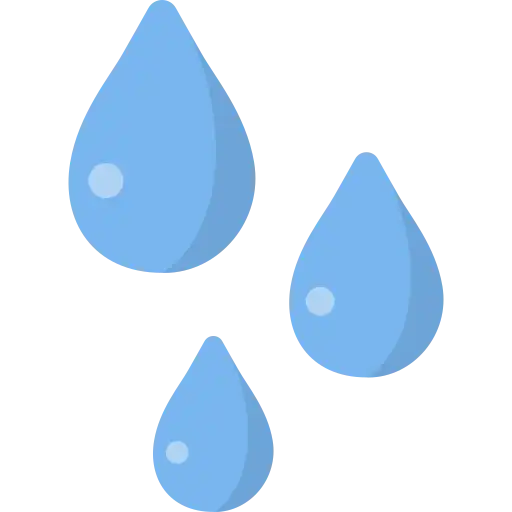
The secend Number"X" (IP 1X)
indicates protection against liquids
Here is a table listing the IP (Ingress Protection) rating codes and their meanings.
For Example
an IP55 rating means the motor is protected against dust and low-pressure water jets, making it suitable for many industrial applications. Selecting the right IP rating ensures that the motor is shielded from external damage and maintains performance over time.

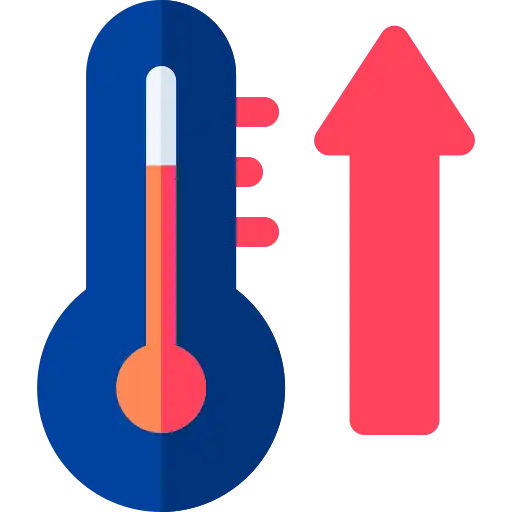
Temperature Rise
Temperature rise on a motor nameplate indicates the maximum permissible increase in temperature during operation.
It’s a critical parameter for preventing overheating, especially in environments with varying ambient temperatures.
Temperature rise is measured in degrees Celsius and helps ensure the motor runs within safe limits.
For Example
A motor with a temperature rise of 80°C can handle that level of heat increase before it risks damage. Keeping this in mind is essential for applications in hot climates or settings with limited ventilation, as it ensures the motor operates safely and efficiently without premature wear.
Here is a table of electric motor temperature rise.
Insulation Class | Maximum Temperature Rise (°C) | Typical Applications |
---|---|---|
Class A | 60°C | Light-duty applications, older motor designs. |
Class B | 80°C | Standard industrial motors, general-purpose motors. |
Class F | 105°C | Heavy-duty motors, higher ambient temperatures. |
Class H | 125°C | High-performance motors, extreme environments. |
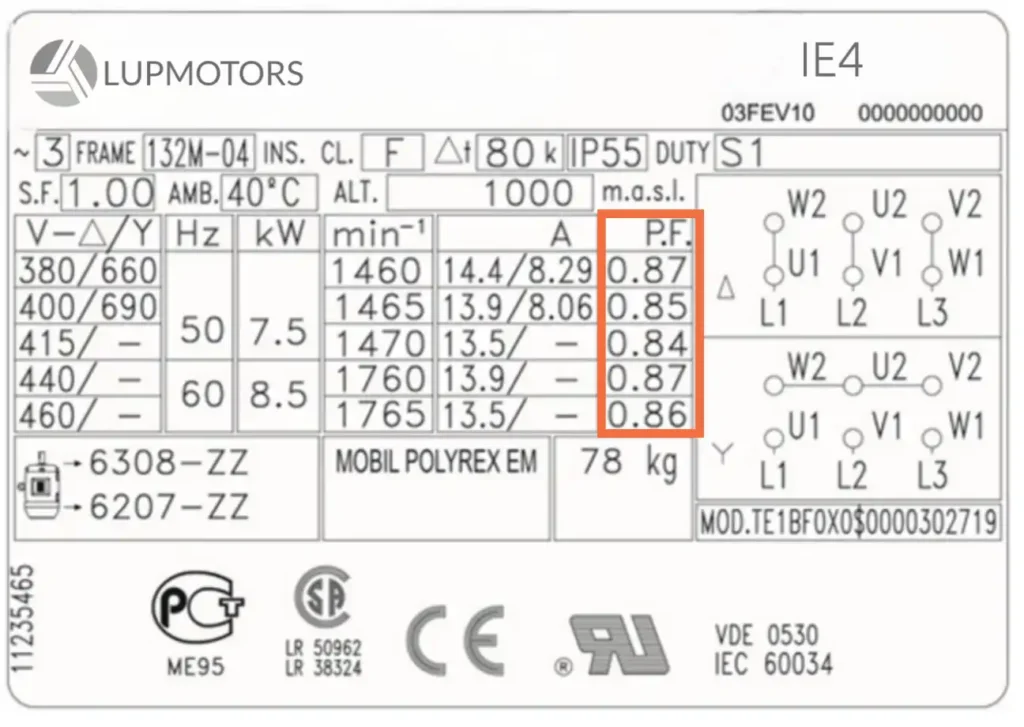
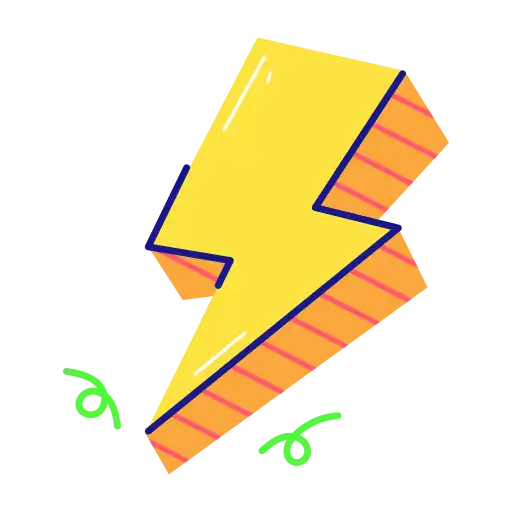
Power Factor
The power factor on a motor nameplate indicates how effectively the motor converts electrical power into mechanical energy.
A higher power factor means the motor is more efficient, resulting in lower energy costs and reduced power wastage.
For Example
A motor with a power factor of 0.9 is more efficient than one with a power factor of 0.7. High power factor motors are especially valuable in industrial applications where energy savings can make a significant financial impact over time, enhancing overall operational efficiency.
Here is the formula to calculate the electric motor power factor.
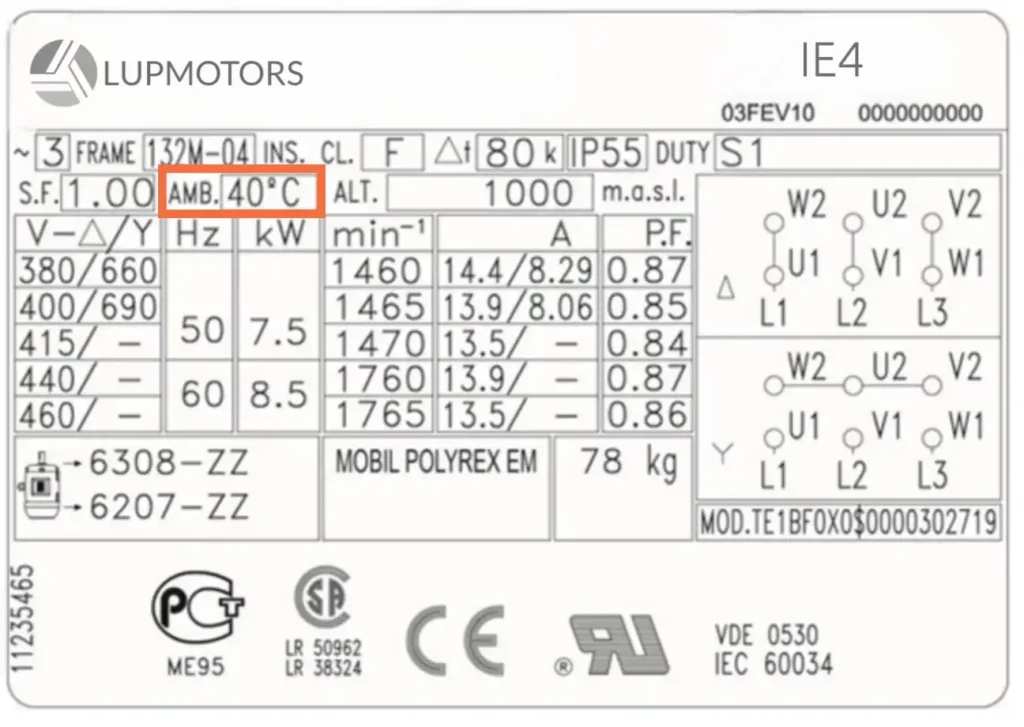
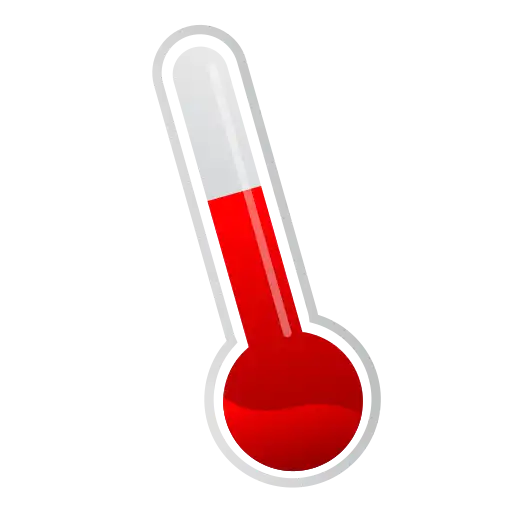
Ambient Temperature
The ambient temperature listed on a motor nameplate indicates the highest temperature in which the motor can safely operate.
If the surrounding temperature exceeds this value, the motor may overheat, reducing its lifespan and performance.
For Example
If a motor’s ambient temperature rating is 40°C, it’s designed to function optimally up to that temperature. In hotter environments, additional cooling measures might be needed to prevent overheating and ensure long-term durability.
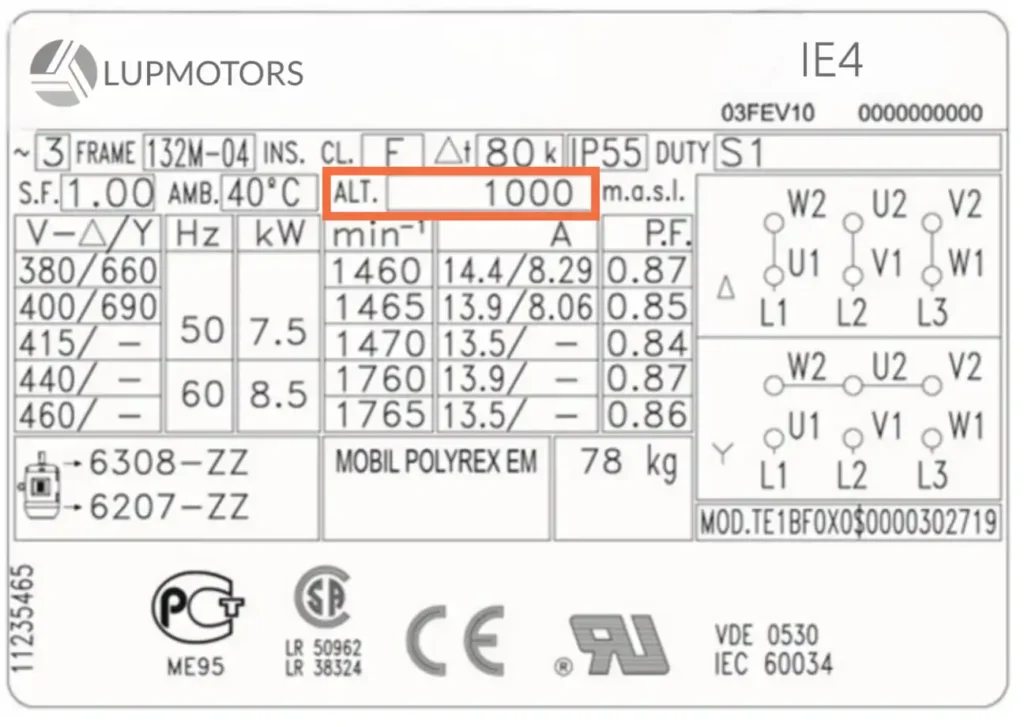
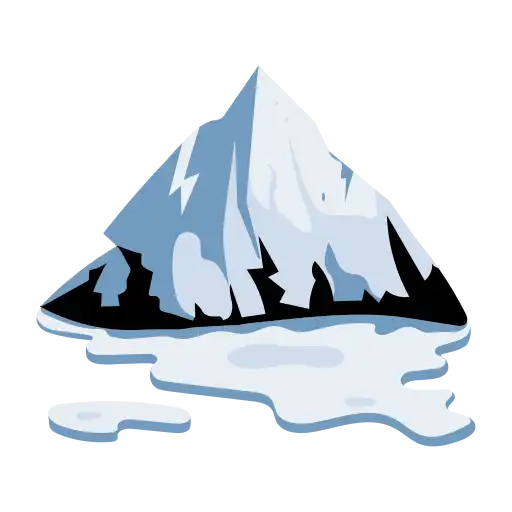
Altitude
The altitude rating on the motor nameplate specifies the maximum elevation at which the motor can function effectively.
At higher altitudes, air density decreases, which impacts the motor’s cooling capacity.
Motors running above their rated altitude may need to be “derated” or run at reduced power to avoid overheating.
For Example
A motor rated for 1,000 meters above sea level might need modifications if installed at 2,000 meters. This specification ensures the motor operates within safe thermal limits.
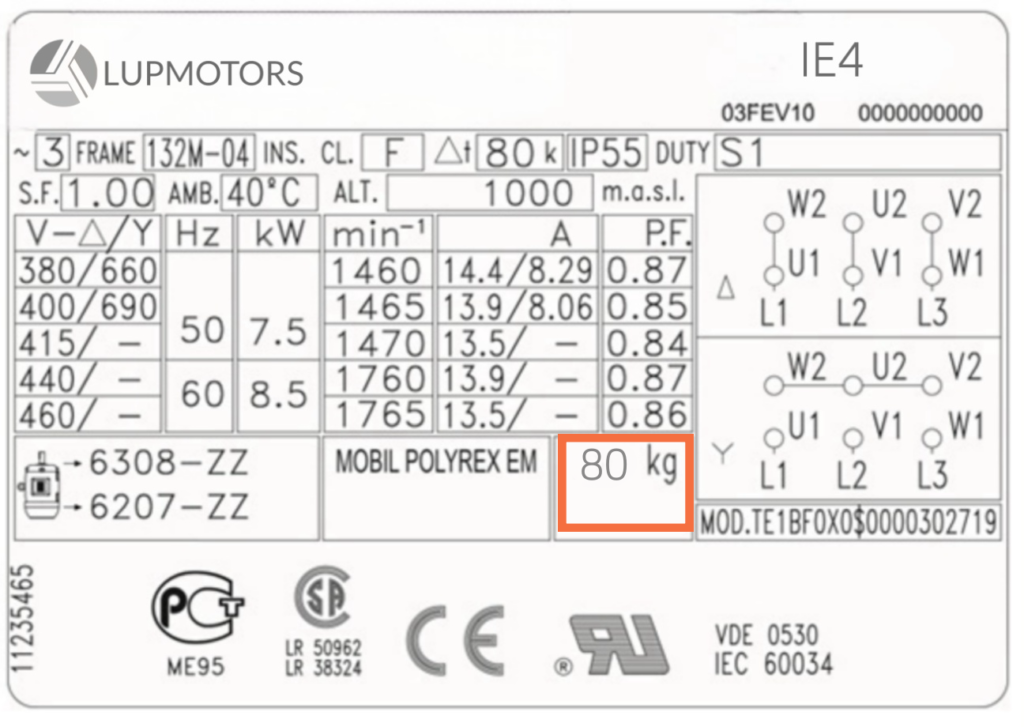
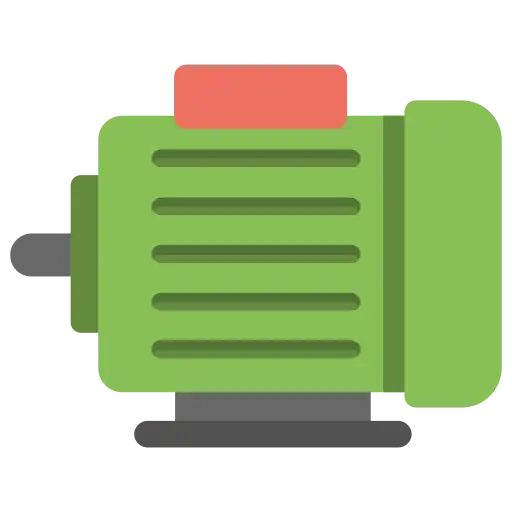
Motor Weight
Motor weight is also indicated on the nameplate and is essential for planning installation, transport, and mounting.
Knowing the weight helps determine the structural support required and the type of lifting equipment needed.
For example, the nameplate shows this motor’ weight is 80KG.
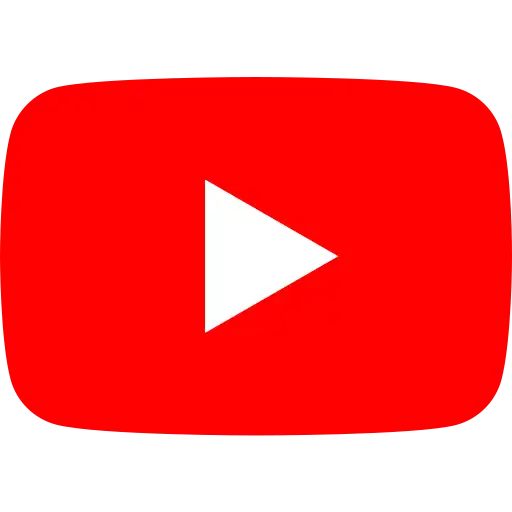
You can view this video to get more knowledge about the nameplate of an electric motor.
Tip: I recommend you to view this video. I suppose it may help you a lot. In the video the engineer explains the meaning of each pieces of information on the nameplate.
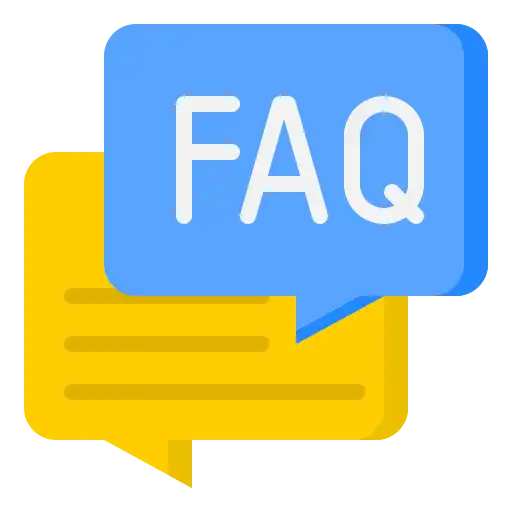
2. FAQs about Electric Motor Nameplates
What is the Service Factor on a Motor Nameplate?
The Service Factor (SF) shows how much a motor can handle above its rated load intermittently. For instance, a motor with a 1.15 SF can carry 15% more than its rated load for short periods. This flexibility is useful for handling occasional load spikes without damaging the motor. Just remember, running at higher loads consistently can reduce motor life, so it’s best to keep loads close to the rated amount.
How to Tell if a Motor is Single-Phase or Three-Phase?
You can find this information directly on the motor nameplate under “Phase.” Single-phase motors typically operate on 120V or 240V and are used in residential or light commercial settings. Three-phase motors, common in industrial applications, often require 208V, 230V, or 460V, providing greater efficiency and power.
Why is Frame Size Important?
Frame size is critical for ensuring that the motor fits correctly in its designated space. It defines the motor’s physical dimensions and mounting configuration. A mismatch in frame size can lead to installation issues, misalignment, and even vibrations that harm both the motor and connected machinery. Always match the frame size to ensure stable and secure mounting.
What are IE1, IE2, and IE3 Motors?
These are energy efficiency classes defined by the IEC. IE1 represents standard efficiency, IE2 is high efficiency, and IE3 is premium efficiency. Using motors with higher efficiency (like IE3) can reduce energy costs and lower the environmental impact. In regions with strict energy regulations, using high-efficiency motors may also be required by law.
What Information Can be Commonly Found on a Motor Nameplate?
A motor nameplate typically includes critical specifications like rated power, voltage, frequency, RPM, service factor, frame size, efficiency rating, IP rating, and ambient temperature limits. Each parameter helps determine if the motor is suitable for a particular application and ensures safe, efficient operation.
We offer customized motor solutions to meet your specific application requirements
LUPMOTORS offers ac low voltage 3-phase asynchronous industrial motors of all types – Please contact us freely.
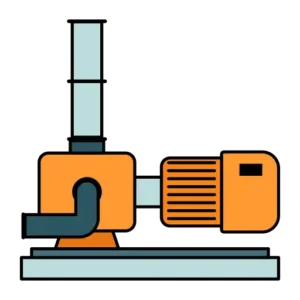
Synchronous Motor vs. Induction Motor: The Definitive Guide
“Discover the key differences between synchronous and induction motors. Learn about their structure, operation, advantages, and applications to make the right choice for your needs.”
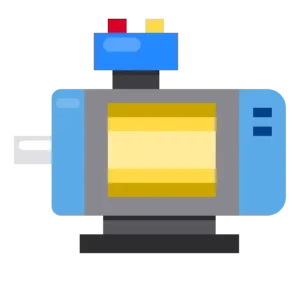
AC vs. DC Electric Motors: What’s the Difference?
Discover the key differences between AC and DC motors. Learn their working principles, advantages, and real-world applications to choose the right motor for your needs.
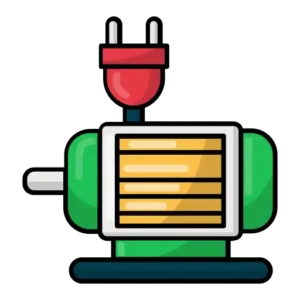
10 Duty Cycles for Electric Motors that You Need to Know
Discover the 10 essential duty cycles for electric motors! Learn how each impacts performance, efficiency, and applications. Perfect for engineers & industries.
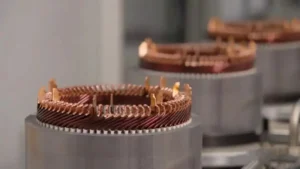
Stator vs. Rotor: Difference, Functions, Components & More
Discover the key differences between stator and rotor in electric motors. Learn their functions, components, applications, and innovations. Motor Stator vs. Rotor.
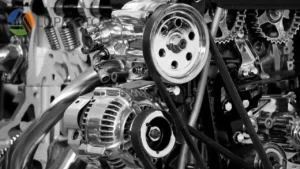
Speed Control of Three-Phase Induction Motor | 7 Methods
Discover effective methods for speed control of three-phase induction motors, including V/f control, pole changing, and rotor resistance control, to enhance efficiency and performance.
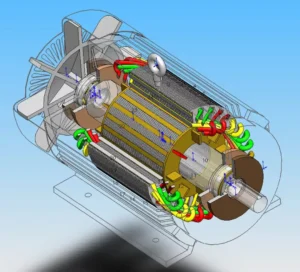
3-Phase AC Induction Motor | Working Principle, Definition & Types
Learn the working principle of 3-phase AC induction motors, their definition, structure, types, and real-world applications. A must-read for industrial insights!
very clear article.Help me a lot
This is a professional article to clarify the knowledge about motor RPM.