Medium & voltage High Voltage AC Motors
LUPMOTORS’ high-efficiency high-voltage three-phase asynchronous motors, developed from extensive design and manufacturing experience, offer superior performance, energy savings, and environmental benefits. They feature lower center height, higher power, greater efficiency, and lower noise, ensuring safe and reliable operation with easy maintenance. Ideal for driving fans, compressors, pumps, and various machinery, these motors are perfect for mining, steel, petroleum, chemical, and power plants, performing reliably in both indoor and outdoor environments, including high-altitude and humid climates.
Medium & voltage High Voltage AC Motors
Designed to meet your specific applications, LUPMOTORS‘ High Voltage range of motors is available in voltages from 2.3kV to 11kV, with options in cast iron and fabricated steel enclosures. We support all mounting forms, including Foot, Foot & Flange, Vertical Flange, and Vertical High-thrust. Our motors can be tailored for a variety of applications, including hazardous environments compliant with CSA Class 1, Division 2, ExnA, and Exp standards. They are also compatible with VFD operations and adhere to global specialty standards such as AP1541/547 and IEEE841.
Customize your specific applications, LUPMOTORS' High Voltage range of motors is available in a variety of enclosure types, including:
- Frame:H80~H450
- Power scope:150kW to 22,000kW
- Rated voltage:380V/ 415V/ 460V/ 490V/ 660V/ 690V
- Rated frequency:50HZ/ 60HZ
- Speed:3000rpm, 1500rpm, 1000rpm, 750rpm
- Mounting:IMB3/ IMB5/ IMB35/ IMV1
- Protection class:IP55
- Cooling type:IC411
- IC611/IC81W/(IC01)
Could not find your product? Please click here to leave message
LUPMOTORS offers all kinds of high voltage squirrel cage motors of all types – Please contact us freely.

TEFC IC01 Squirrel Cage Induction Motors
Cooling:IC81W/ IC01/IC611-CACA/IC666
Pole: 2/4/6/8/10/12 poles
Mounting:foot-IMB3/IM1001;vertical-IMV1/IM3011
Standard:IEC60034/GB755
Voltage(V):380/550/3300/
4800/5500/6000/6600/10000/11000

TEAAC IC611 Squirrel Cage Induction Motors
Cooling:IC611-CACA
Pole: 2/4/6/8/10/12 poles
Mounting:foot-IMB3/IM1001;vertical-IMV1/IM3011
Standard:IEC60034/GB755
Voltage(V):380/550/3300/
4800/5500/6000/6600/10000/11000

TEWAC IC611 Vertical Mount Squirrel Cage Induction Motors
Cooling:IC01/IC611-CACA
Pole: 2/4/6/8/10/12 poles
Mounting:vertical-IMV1/IM3011
Standard:IEC60034/GB755
Voltage(V):380/550/3300/
4800/5500/6000/6600/10000/11000

TEWAC IC81W Squirrel Cage Induction Motors
Cooling:IC81W
Pole: 4/6/8/10/12/14/16 poles
Mounting:foot-IMB3/IM1001;vertical-IMV1/IM3011
Standard:IEC60034/GB755
Voltage(V):380/550/3300/4800/
5500/6000/6600/10000/11000

TEAAC IC666 Variable Frequency AC Motors
Cooling: IC666
Pole: 4/6/8/10/12 poles
Mounting:foot-IMB3/IM1001;vertical-IMV1/IM3011
Standard:IEC60034/GB755
Voltage(V):380/550/3300/4800/
5500/6000/6600/10000/11000

TEAAC Explosion Proof HV AC Motor
Cooling:IC666
Pole: 2/4/6/8/10/12 poles
Mounting:foot-IMB3/IM1001
Standard:IEC60034/GB755
Voltage(V): 3300/4800/5500/6000
/6600/10000/11000
LUPMOTORS Display
Factory
Established in 1995, LUPMOTORS equipped with over 200 specialized machines, including various machining centers, high-speed punches, automatic winding machines, vacuum impregnation systems, and assembly lines, we possess robust in-house component manufacturing capabilities. Annually, we produce up to 300,000 motors, totaling 8 million kilowatts.

Specializing in the Research, Development, Production, and Sales of high-efficiency motors
- more than 200 sets of special equipment
- various machining centers, high-speed punching, automatic wire embedding machines, vacuum dipping machines, assembly lines, etc.
- It has a strong ability to manufacture parts and components.
- It can produce 300,000 units and 8 million kilowatts of various motors including low-voltage motors, explosion-proof motors, permanent magnet synchronous motors, high-voltage motors, servo motors, etc. every year.

Are you looking for cost-effective energy-saving and efficiency-enhancing solutions
We can save your money!
Taking LUPMOTORS’ 55-kW motor as an example, a high-efficiency motor saves 15% more electricity than a general motor. The cost of replacing the motor can be recovered through electricity saving within one year of using an energy-saving motor.

Excellent Motors with Competitive Price.
- The motor's structural parts are made of high-quality cast iron or die-cast aluminum, and the structure is optimized to ensure the motor's structural rigidity and strength requirements.
- The stator and rotor cores are made of high-quality silicon steel plates with good surface insulation and low loss, making the motor more efficient.
- The insulation is made of excellent insulating materials, which complement the perfect insulation design, making the insulation complete and gapless. The winding end has good rigidity and can withstand higher switching and commutation strength. The F-class insulation gives the motor higher thermal stability and longer service life.
- Generally, the rotor adopts die-casting technology to make the rotor quality stable and beautiful. The rotor balancing technology includes balancing, dynamic balancing, and overall running balancing. All LUPMOTORS' motors meet the standard vibration requirements. The rotor balance is closely related to the bearing life.
- The design and selection of bearings and structures fully consider the motor type, force, speed, and lubrication method. Including the bearing, oil seal design and grease selection, etc., reliable performance and convenient maintenance. Generally, motors with a center height of 250 or less use closed bearings, and motors above that use open bearings. The bearings are equipped with non-stop oil injection and discharge devices.
- The perfect primer special coating ensures the motor's beautiful appearance and durability. The closed type uses RAL5000 matte when painted. The open type uses RAL7031 matte. Special anti-corrosion coating can be used according to customer requirements.
How to find the best motor solution for your industrial application?
LUPMOTORS offers varioust high voltage squirrel cage motors of all types – Please contact us freely and our guide will help you to select the right motors. Easy to communicate without deep technical knowledge.
LUPMOTORS' high-voltage three-phase asynchronous motor ordering instructions
- 1. If there are any special requirements for noise, please provide them to us
- 2. If there are special requirements for vibration, please provide us with them (standard values: amplitude 0.037mm; vibration speed 23mm/s)
- 3. If there is any special requirement for the number of starts, please provide it to us (the standard is 2 times in cold state and 1 time in hot state)
- 4. The direction of rotation must be informed to us (the standard is clockwise when viewed from the motor shaft end, and the motor must indicate the direction of rotation)
- 5. Please provide us with the motor load type (such as: fan, water pump, mill, crusher, compressor, rolling mill, disc mill, etc.)
- 6. If there are special requirements for the load moment of inertia, please provide it to us.
- 7. Please tell us what the transmission method is. (such as with hydraulic coupling or with gear box or direct core connection)
- 8. Please tell us what the coupling type is (such as coupling or pulley, and the belt tension is also required)
- 9. Is an encoder interface provided on the motor?
- 10. Is the motor you need used in plateaus? (Motors operating at altitudes above 1,000 meters require special designs)
- 11. Please let us know what the ambient temperature is for the motor to operate in.
- 12. Is the motor used in a hot and humid area?
- 13.Is the motor used outdoors?
- 14.Is the motor used near the sea?
- 15. Are there any requirements for corrosion protection? (e.g. F1 mild corrosion, F2 moderate corrosion, F3 severe corrosion)
- 16. What type of bearing is used? (such as rolling bearing or sliding bearing) Do you need imported bearings? (SKF, FAG, NSK, China domestic)
- 17.Does the bearing bear thrust?
- 18.Are there any insulation requirements for bearings?
- 19. Do you need us to provide a thin oil station?
- 23. Is CT required? If CT is required, where should it be installed in the main outlet box or the neutral point outlet box?
- 25. Is it necessary to install a moisture-proof heater?
- 26. Is it necessary to install a vibration sensor?
- 27.Are there any special requirements for temperature measuring components?
- 28. Are there any special requirements for rotor cage materials? (such as cast aluminum, copper bars, trapezoidal copper bars)
- 29.Does the paint color need to be specified?
- 30.Does the motor need double shaft extension?
- 31. Please make sure the location of the terminal box is clear (the standard is that the terminal box is installed on the right side when viewed from the motor shaft end to the motor)
- 34. If there are special requirements for the motor starting current multiple, please provide it to us.
- 33. If there are special requirements for the motor starting torque multiple, please provide it to us.
Are you looking for the high voltage three-phase AC Industrial motor?
LUPMOTORS offers vertical mount high voltage squirrel cage motors of all types – Please contact us freely.
REQUEST A QUOTE FOR MORE DETAILS
Your Comprehensive Guide to Selecting High voltage Induction AC Motors
Many people struggle to understand some knowledge of high voltage AC industrial motors.
This confusion often leads to costly mistakes and inefficiencies in industrial settings.
Let’s break down the basics of the high voltage AC induction motors, a crucial component in many industries, and help you avoid these common pitfalls.
All You Need To Know About the High Voltage AC Induction Motor
CHAPTER ONE
The Definition of the High Voltage AC Induction Motors

For AC motors, those with a rated voltage of 1000V or above are high voltage motors; those below 1000V are low voltage motors (some materials limit it to 1140V). For DC motors, those with a rated voltage of 1500V or above are high voltage motors; those below 1500V are low voltage motors.
Your Private Decision Motor Guider
LUPMOTORS offers vertical mount high voltage squirrel cage motors of all types – Please contact us freely.
CHAPTER TWO
Advantages of using high voltage motors
The motor power can be increased, up to several thousand or even tens of thousands of kilowatts.
This is because, when outputting the same power, the current of the high-voltage motor can be much smaller than that of the low-voltage motor.
For example: 500KW, 4-level three-phase AC motor has a rated current of about 900A when the rated voltage is 380V, while it is only about 30A when the rated voltage is 10KV.
Therefore, the winding of the high-voltage motor can use a smaller wire diameter.
As a result, the stator copper loss of the high-voltage motor will also be smaller than that of the low-voltage motor.
For higher-power motors, when using low-voltage electricity, a larger area of stator slots is required due to the need for thicker wires, which makes the stator core diameter very large, and the volume of the entire motor will also become very large;

For larger capacity motors, the power supply and distribution equipment used by high-voltage motors require less overall investment than low-voltage motors, and the line loss is small, which can save a certain amount of power consumption.
In particular, 10KV high-voltage motors can directly use the power grid, so the investment in power supply equipment will become less, the use will become simpler, and the failure rate will also be reduced.
Your Private Decision Motor Guider
LUPMOTORS offers vertical mount high voltage squirrel cage motors of all types – Please contact us freely.
CHAPTER THREE
Speed regulation method of high voltage motor
1.Hydraulic Coupler
An impeller is added between the motor shaft and the load shaft, and the pressure of the liquid (usually oil) between the impellers is adjusted to achieve the purpose of adjusting the load speed.
This speed regulation method is essentially a slip power consumption method.
Its main disadvantages are that the efficiency becomes lower and lower as the speed decreases, the motor and the load need to be disconnected for installation, and the maintenance workload is large.
After a period of time, the shaft seal, bearing and other components need to be replaced.
The site is generally dirty, and the equipment grade is low, which is an obsolete technology.
Manufacturers who were more interested in speed regulation technology in the early days either because there was no high-voltage speed regulation technology to choose from or because of cost factors, had some applications for hydraulic couplings.
Such as water pumps of water companies, boiler feed pumps and induced draft fans of power plants, and dust removal fans of steel mills.
Now, some old equipment has been gradually replaced by high-voltage frequency conversion during the transformation.

2.High-low-high inverter
The inverter is a low-voltage inverter, which uses an input step-down transformer and an output step-up transformer to realize the interface with the high-voltage power grid and the motor.
This was a transitional technology when the high-voltage frequency conversion technology was not mature at that time.
Since the voltage of the low-voltage inverter is low, the current cannot rise unlimitedly, which limits the capacity of this inverter.
Due to the existence of the output transformer, the efficiency of the system is reduced and the floor space is increased; in addition, the magnetic coupling ability of the output transformer is weakened at low frequency, which weakens the load capacity of the inverter at startup.
The harmonics of the power grid are large. If 12-pulse rectification is used, the harmonics can be reduced, but it cannot meet the strict requirements for harmonics; while the output transformer is stepping up, the dv/dt generated by the inverter is also amplified.
A filter must be installed to be suitable for ordinary motors, otherwise corona discharge and insulation damage will occur.
If a special variable frequency motor is used, this situation can be avoided, but it is not as good as using a high-low type inverter.
2.High and low frequency converter
The inverter is a low-voltage inverter.
A transformer is used on the input side to convert high voltage into low voltage.
The high-voltage motor is replaced with a special low-voltage motor.
The voltage level of the motor varies and there is no unified standard.
This approach uses a low-voltage inverter, and the capacity is relatively small, so the harmonics on the grid side are large. 12-pulse rectification can be used to reduce harmonics, but it cannot meet the strict requirements for harmonics.
When the inverter fails, the motor cannot be put into operation in the power frequency grid, and there will be problems in some occasions where it cannot be shut down.
In addition, the motor and cable must be replaced, and the engineering workload is relatively large.
Cascade speed inverter feeds part of the rotor energy of the asynchronous motor back to the grid, thereby changing the rotor slip to achieve speed regulation.
This speed regulation method uses thyristor technology and requires the use of wound asynchronous motors.
However, squirrel cage asynchronous motors are almost all used in industrial sites, and it is very troublesome to replace the motor.
The speed regulation range of this speed regulation method is generally around 70%-95%, and the speed regulation range is narrow.
Thyristor technology is prone to causing harmonic pollution to the power grid; as the speed decreases, the power factor on the grid side also decreases, and measures need to be taken to compensate.
Its advantage is that the capacity of the frequency conversion part is small, and the cost is slightly lower than other high-voltage AC frequency conversion speed regulation technologies.
This speed regulation method has a variation, namely the internal feedback speed regulation system, which saves the transformer of the inverter part and directly makes the feedback winding in the stator winding.
This method requires replacing the motor, and the performance in other aspects is close to the cascade speed regulation.
The cascade speed regulation motor is affected by the rotor slip ring and cannot achieve high power.
The slip ring maintenance workload is also large.
It is a backward technology from the 1970s and 1980s, and its industrial application has become less and less.
Your Private Decision Motor Guider
LUPMOTORS offers vertical mount high voltage squirrel cage motors of all types – Please contact us freely.
CHAPTER FOUR
High voltage motor installation steps and precautions
Preparation before motor installation Check all items in the motor factory packing list at the installation site.
Determine the position mark on the foundation platform and find the center line of the unit and the elevation of the foundation surface.

Application of motor positioning verification The motor should be installed in a well-ventilated place, with an ambient temperature not higher than 40 and an altitude not higher than 1000 meters, otherwise special orders are required.
Pay attention to the air inlet and outlet of the motor, and do not let the exhausted hot air enter the air inlet to produce repeated circulation, or the hot air exhausted from one motor directly enters another motor.
Make sure there is enough working space around the motor to disassemble, clean or inspect the motor.
When installing a sliding bearing motor with an oil ring, the shaft should be kept in a horizontal position to avoid oil leakage and ensure good oil ring performance.
Foundation and mounting base of the motor
The foundation must be rigid to minimize vibration of the motor and misalignment of the shaft during operation. The foundation should be on a rigid foundation with a rigid concrete pier of sufficient depth. The required dimensions of the foundation are shown in the outline drawing. If there is a pit under the motor, there should be enough working space for installation and maintenance.
Rough positioning
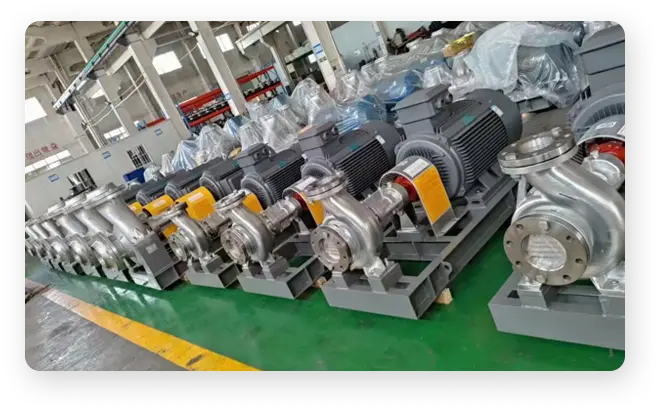
Place the motor on the steel base and align it close to the final axis. Pass the anchor bolts through the motor anchor holes and align them with the screw holes to confirm that the rotor fixing bracket has been removed.
The rotor of the sliding bearing motor should be placed at the magnetic center or the midpoint of the rotor’s axial movement (mechanical center).
It must be ensured that the motor rotor is always in the magnetic center alignment position under hot operation.
In some cases, the shaft of the driven equipment
experiences thermal expansion. When the motor is installed at room temperature, it is in the magnetic center position.
This expansion can cause the rotor axial position of the motor to shift under normal operation.
Compensate for the magnetic center offset caused by thermal expansion of the driven equipment shaft.
When installing the motor at room temperature, the stator should be moved a small distance away from the driven equipment.
The value is equal to the expansion of the driven equipment shaft between the rated operating temperature and the room temperature at installation.
This value should be provided by the manufacturer of the driven equipment.
Prevent motor bearings from being damaged by thrust loads. Due to the thermal expansion of the shaft of the driven equipment or other axial forces, the motor rotor bearings may move axially, which may cause the bearings to be damaged by thrust loads. Therefore, the coupling must be able to limit the range of rotor movement.
Assuming the total floating clearance of the sliding bearing motor is W mm, the placement of the coupling must limit the total floating value of the rotor to (0.36-0.38) W mm, and the floating centerline is at the mechanical center.
For example, if the floating clearance of the motor is W=12.7 mm, the coupling must limit the total floating value of the rotor to 0.38×12.7=4.8 mm.
When the positioning of the motor has met the requirements of axial floating, install and tighten the foot bolts.
Alignment of motor angle and position
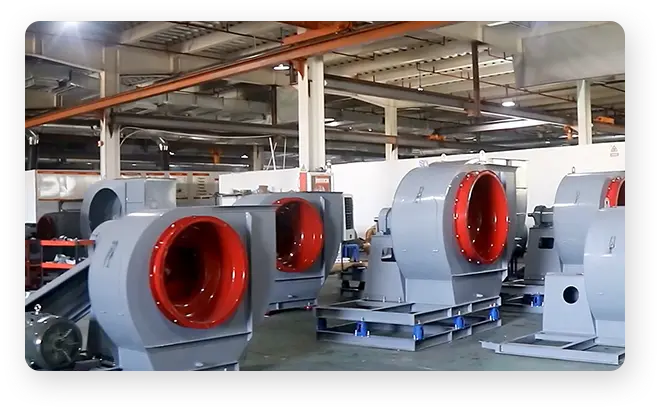
● Rough calibration
1) Use a block gauge and a feeler gauge to adjust the clearance between the motor and the driven equipment couplings to the same level with the coupling end face as the reference surface.
2) Measure the clearance at the top, bottom, left and right sides. The deviation should not exceed 0.1mm. After the base is positioned, the anchor bolts are grouted.
●Precise alignment
After the primary grouting reaches the required strength, tighten the base bolts with a torque wrench to the specified torque. Using the fan shaft as a reference, align the motor accurately by measuring the coupling between the motor and the driven equipment.
1) When measuring radial circular runout, place a micrometer in the radial direction; for end circular runout, place two micrometers symmetrically at equal distances from the center of the shaft. While measuring the radial reading (radial circular runout) in one direction, measure the axial reading (end circular runout) in the opposite two directions to eliminate the influence of the shaft movement on the axial reading during turning.
2) Compare the radial clearance (radial reading) and axial clearance value (axial reading) of the coupling with the required values, and then adjust them according to the offset. First adjust the axial clearance to make the two halves of the coupling parallel, and then adjust the radial clearance to make the two halves of the coupling coaxial.
3) The horizontal fine-tuning of the motor is done by adjusting the block installed on the base with the top screw. The vertical fine-tuning is done by adjusting the top screw on the motor base. Accurate calibration is performed by adding or subtracting shims and moving the motor until the allowable error is reached.
After the alignment is qualified, tighten the motor anchor bolts alternately, re-measure the alignment deviation, and record the measured value. After the motor is finally positioned, install the positioning pin and use a conical reamer to expand the hole to ensure that the positioning pin can be inserted by hand and is flush with the top. Screw the hexagonal bolt and washer into the conical pin to a depth of about 5mm. Use a hammer to gently tap the conical pin so that the conical pin sinks to the same depth and tighten the hexagonal bolt.
Your Private Decision Motor Guider
LUPMOTORS offers vertical mount high voltage squirrel cage motors of all types – Please contact us freely.
Learn More From FAQs
You’ll find yourself working in a true partnership, resulting in an incredible experience and a competitive end products.
We are a professional manufacturer that produces and sells a variety of motors.
No. We can accept an order just for 1 motor.
For all our customers, they may have different technical requirements, such as power, voltage, type, etc. The price also varies according to different order quantities. Therefore, it is really difficult for us to provide a price list. If you can share your detailed specifications and order quantity, we will provide the price to you.
We can provide both FOB and CIF prices.
Contact Us
Consult your motor expert
LUPMOTORS is your best choice!